فهرست مطالب
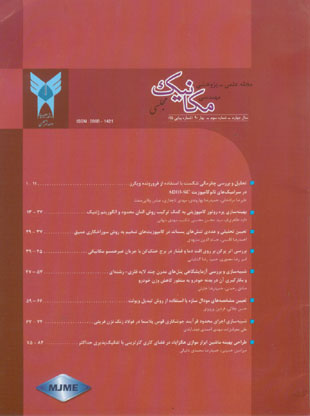
International Journal of Advanced Design and Manufacturing Technology
Volume:4 Issue: 3, 2011
- تاریخ انتشار: 1390/04/14
- تعداد عناوین: 8
-
Pages 1-11The basic trait in the ceramics is their high brittle or low fracture toughness, and the main criteria in the design and application is specifying the fracture toughness in ceramics. In this paper, a new method is proposed to determine the fracture toughness of ceramics, which is enhanced in lowering the cost of fracture toughness determination relative to the previous methods. Hence due to the low cost and case of access of alumina (Al2O3) which is extensively used in ceramics industry, it is applied as the most important source for achieving the objectives. Pure alumina has excellent properties such as refractory and high hardness on one hand, and has disadvantages such as low fracture toughness on the other hand. In order to improve its mechanical properties, various additives such as nano scale silicon carbide (SiC) powder are used. In this paper, alumina micro powder having 5% nano magnesium oxide by weight were mixed separately with silicon carbide nano particles of 2.5%, 5%, 7.5%, 10% and 15% to construct various types of ceramics, with different physical and mechanical properties. Semi experimental equation for their fracture toughness determination was presented and used for other brittle materials. This equation has minimal cost of experiments for determining fracture toughness of different brittle materials.
-
Pages 13-27In this paper, an optimization method for both weight and displacement of composite blades is presented. In order to hold issues such as aerodynamics and acoustic unchanged, airfoil shape during optimization process remained constant. To achieve the ultimate goal, only blade lamination was changed. In order to achieve minimum weight for each part of the structure, the lowest layers are forecasted according to the required strength. Hence, the blade is divided into different parts. In optimization process, while focusing on weight and displacement reduction, layers integration must be assured. For desired performance, during optimization process, mass center location must be placed ahead of the aerodynamic center of blade. Weight reduction is in contrast to the displacement changes, and reduction in each of them would lead to an increase to the other. In optimization process, any changes in lamination of each part would influence the performance of the other parts. Therefore, in this paper, by making changes in genetic algorithm and defining appropriate objective function, design variables and other constraints, all of the above requirements are satisfied. Meanwhile, the natural frequencies of the optimized blade structure were in an acceptable range. Results and performance of the optimized blade are quite acceptable in comparison to the ordinary blades.
-
Pages 29-37In this paper, deep hole drilling method for measurement of non-uniform residual stress in thick composite laminated plates is simulated. The deep hole method is a well known method for measurement of residual stress in large metallic components. In this method, first a hole is drilled perpendicular to the surface of the laminate and the hole diameter is measured accurately after wards. Then, by trepanning process the residual stresses will be released. The hole diameter is re-measured accurately and recorded. Finally, the residual stresses can be calculated through the difference in diameter of the hole. The finite element software, ANSYS 11. is used for analysis and simulation of the method. Also, for three dimensional simulation of the deep hole drilling method the three-dimensional "solid brick layered 46" is used. The hole diameter was 10mm that is smaller than other dimensions. First, convergence test has been applied to optimize the size of the mesh so that the results are reliable. Three types of loading Fx, Fy and Fxy were applied to finite element analysis. These results have been compared with Lekhnitskiiۥs solution and Savin ۥs for orthotropic materials. Lekhnitskii solved problems for stresses around different shapes of holes under different loads using series method. As it can be observed the results of this simulation are in good agreement with Lekhnitskiiۥs and Savin ۥs solution.
-
Pages 39-45Cooling towers are widely used in most industrial units to reject waste heat to the atmosphere. This paper deals with an experimental analysis of heat and mass transfer phenomena between water and air by direct contact in a cooling tower. The tower is filled with 6 type packing. In this study temperature and pressure drop and tower characteristics was used in determining experimentally the thermal performance of the cooling tower. Temperature drop decreases as water mass flow rate increases, pressure drop increases as mass flow rate ratios increases and tower characteristics increases as water mass flow rate increases. The data registered in the experimental set up were employed to obtain correlation of the tower characteristics.
-
Pages 47-57
Automobile body plays crucial role in preventing the collision energy transfer in severe accidents to the passengers. If the collision energy is dissipated or saved in bumper or chassis, the amount of damage to the occupants would be minimized. Using novel laminated panel (Fiber Metal Laminate) in auto body, and considering the characteristics such as high energy absorption, strength, high dent resistance, and very light weight, has caused significant reduction in injury to the car passengers. One of the major plans in auto industry is to lessen emission and fuel consumption using light weight material in auto body, which is recently achievable by replacing multi light layers with single metal layer panels, in auto body. These panels are usually made of two thin metal layers surrounding the core composite. The first point regarding panels is their strength against depression which is so called Dent Resistance. Weight reduction of panels should not sacrifice dent resistance of panels. The purpose of this paper is to investigate fiber metal laminate panels, dent resistance analysis and the amount of energy absorption of these panels, in order to implement in auto body. Strength, high dent resistance, and very light weight of such panels may lead into substantial reduction in crash injuries during car accidents.
-
Pages 59-66Identification of damping parameter is usually more complicated and unreliable comparing to mass or stiffness identification in structural dynamics. There are many factors such as intermolecular friction, Coulomb friction and Viscous damping affecting the damping mechanisms in a structure. Therefore it is difficult, and in some cases impossible, to describe the details of damping mechanisms by using mathematical tools. In order to overcome the difficulties arising when using different damping models, the equivalent viscous damping is used. The coefficient of equivalent viscous damping can be identified experimentally by measuring the structural response. During the past decades, many methods have been proposed for damping parameter identification employing time domain data (e.g. logarithmic decrement method) or frequency domain data (e.g. using frequency response functions). There are also time-frequency methods such as wavelet transform. This paper deals with identification of modal damping coefficients and natural frequencies of a structure using wavelet transform. The results obtained by using wavelet transform has a good agreement with those resulted from model updating in lower modes.
-
Pages 67-74In this paper, thermal effect of plasma arc welding is investigated, and temperature field of ferrite stainless steel is acquired. Thermal effect of plasma arc and subsequently the generated temperature field in the work piece is the key for analysis and optimization of this welding process, which is the main goal of this paper. Finite element simulation of welding process by SIMPLEC method and ANSYS software is achieved, using FSI solver for getting stainless steel temperature field, effect of parameters variation on temperature field, and process optimization for different situations of plasma and shielding gases (Argon, Helium, and mixture of both). Lastly, the results of other papers are used to verify the correctness of this paper’s results. The temperate field results have determined the effects of welding parameters, and are used to optimize plasma welding process for improving weld quality. Optimization results for different gases indicates that due to special heat of Helium gas, there is extra potential with respect to Argon gas to narrow the plasma arc and concentrate inlet heat over stainless steel.
-
Pages 75-84In the research, six degrees of freedom Hexapod parallel machine tool is studied and investigated. Jacobian matrix is developed by cinematic relations differentiation and using weighted coefficient method, dimensional analysis operation is carried out on Jacobian matrix. Geometric parameters of Cartesian robot workspace are optimized, considering a minimum allowable rotation about three axes, and implementing Genetic Algorithm in MATLAB software workspace. For the manipulator workspace, isotropy indices, minimum and maximum singular values are calculated. The optimization operation has lead to two different designs of manipulators, namely the isotropic design, and high resolution Cartesian workspace.