فهرست مطالب
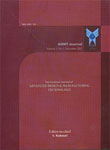
International Journal of Advanced Design and Manufacturing Technology
Volume:9 Issue: 1, Mar 2016
- تاریخ انتشار: 1395/02/20
- تعداد عناوین: 13
-
-
Page 1The metal sheets play an important role in the mechanical design, particularly in the aerospace structures. The rivet connections are frequently used to connect these sheets. The riveting quality greatly influences the rupture of the rivet and the sheet. The various parameters affect the quality of this operation. In this paper, the optimization of the parameters contributing to the riveting quality in order to minimize the value of the maximum tangential stress in the sheets is addressed. To this end, the tolerance of the hole diameter in the top and the bottom sheets, the friction coefficient, and the tolerance of the rivet diameter and the rivet length were considered as the parameters influencing the riveting quality. A total of 64 models were obtained by the permutations of the parameters two at a time. The outputs were determined using the finite element method. The objective function for the optimization is the maximum tangential stress for which there is no analytical relation. Thus, three methods including the multivariable linear regression (MLR), the artificial neural network model of the radial basis function (RBF) type, and the hybrid model of the artificial neural network and the genetic algorithm (ANN-GA) were employed to model this function. Further, the performance of the three models was compared and the most suitable one was selected to model the objective function. The regression model was used to model the values of the height and the diameter after riveting. The imperialist competitive algorithm is utilized to solve this optimization problem. The obtained value for the maximum tangential stress using the imperialist competitive algorithm is 16368 pounds per square inches. After modification, this value increased to 23440 pounds per square inches using the finite element method. . The 0.07689 inches and 0.18524 inches were obtained for the height and diameter of the rivet after riveting, respectively.Keywords: Artificial Neural Network, Finite Element Method, Genetic Algorithm, Imperialist Competitive Algorithm, Multivariable Linear Regression, Riveting
-
Page 13The aim of this article is study of tool plunge depth (TPD) effects on mechanical properties of friction stir welding of AA1100 aluminium alloy to A441 AISI steel. For this purpose the 0.1, 0.2, 0.4, and 0.6 mm TPD selected and other welding parameters kept constant. The results shows that the frictional heat increases and stir zone grain size decreases with increasing TPD at both base metals. At higher TPD, the material press out from shoulder and base metals interface. The highest tensile strength allocated to the joint which welded whit 0.2 mm plunge depth. This joint had appropriate joint efficacy, material flow and microhardness compare other joints.Keywords: Friction stir welding, dissimilar joint, tool plunge depth, mechanical properties
-
Page 23In this paper, vibration equation of a variable-length cable in longitudinal, lateral and torsional directions in a cable robot is analyzed using FE method. The cable is divided into finite elements in which the virtual work equation and Galerkin method can be imposed into the equations. As a result of the stiffness matrix, the characteristic equations and Eigen values of each element can be defined. A simulation study is done in the ANSIS on a robocrane of six degrees of freedom end-effector that is controlled by the aid of six variable-length cables in the space for two different solid and flexible end-effector approaches. Whole the cable robot flexibility is analyzed simultaneously instead of separation calculation of each cable. Not only all of its 3-D vibrating behavior is studied in this paper but also the lengths of the cables are considered variable as it should be. The results are compared for two cases showing the effect of the vibrations in the position of the end-effector and the tension of the cables in different situations.
-
Page 35The aim of this project is to fabricated an aluminium-copper bimetal through the fusion method and examine its performance. An aluminium-copper-aluminium bimetal was built by the laser cladding method. The laser power as well as the annealing time effects on its interfacial properties of the bondings formed through the laser cladding were investigated. To fabricate the multilayer bimetal, the laser beam characteristic including the beam radios, and Transverse Electromagnetic Mode (TEM), and focusing conditions were considered in a heat source model. The model was, next, integrated within SYSWELD package to predict the temperature distribution and clad bead profile during the laser cladding of the pre-placed copper powder layer on the aluminium substrate. After the samples preparation, the intermetallic compounds formed at the joints were explored through the Scanning Electron Microscopy (SEM) and Energy Dispersive Spectroscopy (EDS) processes. Based on the experimental results, a laser power increase from 1100 W to 1150 W increases the intermetallic compound width, while an increase of 1150 W to 1200 W does not have much effect on the width. Also, increasing the annealing time results, increases the intermetallic compound thickness. In addition, based on obtained experimental results, four specimens are detected at the bimetal interface, one of which has 73.4 % copper and 26.1 % aluminium. The results also indicate that, with increasing both the laser power and annealing time, the electrical resistance of the samples decrease.Keywords: Intermetallic growth, Aluminium, Copper, Laser Cladding
-
Page 49This article deals with the buckling analysis of perfectly bonded cross-ply laminated composite plates reinforced by wavy carbon nanotubes (CNTs) under in-plane loads using element free Galerkin (EFG) method based on first-order shear deformation theory (FSDT). The wavy single-walled CNTs and Poly-co-vinylene are used for the fibers and the matrix, respectively. The CNT fibers are distributed in the polymer matrix in four types of arrangements in each layer. The material properties of the laminated nanocomposite plates are estimated through a micromechanical model based on the extended rule of mixture. The minimum potential energy approach is utilized to obtain the governing equations and the stiffness matrices. Full transformation approach is employed to enforce essential boundary conditions. The accuracy and convergency of the EFG method is established by comparing the obtained results with available literature. Then, the effects of CNT volume fraction and waviness, aspect ratio and distribution type of CNTs as well as plate aspect ratio, plate width-to-thickness ratio and boundary conditions on the buckling behaviour of cross-ply laminated functionally graded carbon nanotube reinforced composite (FG-CNTRC) plates are investigated. The numerical results show that the CNT waviness and aspect ratio have significant effects on the buckling behaviour of FG-CNTRC plates.Keywords: Nanocomposite plates, Buckling, Meshfree method, Functionally graded materials
-
Page 61The abrasive flow machining technique uses a self-deforming tool, an abrasive laden media that is passed back and forth in the passage geometry of the hollow workpiece with the assistance of two hydraulically operated cylinders placed opposite to each other. The material is removed by abrasion generating finer surfaces in the area where flow is restricted. But this method has a low material removal rate. As the time advances, various variants of AFM have been developed by different researchers to increase the productivity and improve the surface finish. Thus a combination of AFM and its process variants were developed to increase material removal rate and surface finish. This article provides a comprehensive review of recent developments in the process variants of AFM and the respective media.Keywords: Abrasive flow machining, Material removal rate, Surface roughness, Hybrid process
-
Page 73In present paper, a point to point optimal path is planned for a mobile manipulator with flexible links and joints. For this purpose, a perfect dynamic modeling is performed for mobile manipulators considering large deformation in links, shear effects, elastic joints, effect of gravitation, and non-holonomic constraints. To study large deformation of links, non-linear relation of displacement-strain and Greens strain tensor are used. Optimal path is planned based on direct methods and applying meta-heuristic optimization methods. In order to get an optimal path profile, maximum load carried by manipulator and minimum transmission time are considered as the objective functions for optimization problem. To provide the parameters of optimization problem, parametric optimization problem is solved using Harmony Search (HS) and Simulated Annealing (SA) efficient methods. In order to investigate the efficiency of the proposed method, simulation studies are performed considering two-link flexible manipulator with wheeled base. The results indicate that the proposed method has a suitable power and performance when facing dynamics non-linear system. Moreover, the results of path planning for manipulators by small and large deformation models are also compared. The effect of flexibility in joints is studied when planning a point to point path.Keywords: Mobile Flexible Manipulator, Elastic Joints, Meta, heuristic Optimization, Large deformation
-
Page 89Piezoelectric microcantilevers (MCs) are a new generation of microbeams used in atomic force microscopes (AFMs). Due to their miniaturization of AFMs as well as their increased imaging precision and speed, these MCs are more popular than their classical counterparts. Given the widespread application of these beams in nanoparticle topography, analysis of their vibrating motion has attracted much attention in research circles. Exact vibratiing analysis as well as study of the vibrating motion of these beams plays a key role in increasing their measuring accuracy in topography, and contribute to their optimum design. To this end, the nonlinear differential equation of vibratiing motion of a MC was initially derived through Lagranges method. Subsequently, the modal analysis and multiple time scale (MTS) methods were implemented to obtain an analytical solution to this equation. The effect on the nonlinear vibrational motion of the interaction between the nanoparticle and the probe was studied. The extended Fourier amplitude sensitivity test (eFAST) was conducted to analyze the nonlinearity sensitivity of the motion. The results obtained from this analysis made it possible to determine optimal geometric dimensions for the MC to increase its sensitivity to motion nonlinearity. Simulation results showed that, at higher inclined angles, the MC sensitivity to vibrational motion nonlinearity increased. The sensitivity analysis results revealed that the MC thickness and the length of its tip had the greatest effect on the MC sensitivity to the nonlinear force of interaction.Keywords: sensitivity analysis, spherical nanoparticle, piezoelectric microcantilever, multiple time scale method
-
Page 101This paper presents a novel formulation and numerical solutions for adhesively bonded composite joints with non-linear (softening) adhesive behaviour. The presented approach has the capability of choosing arbitrary loadings and boundary conditions. In this model adherends are orthotropic laminates that obey classical lamination theory. The stacking sequences can be either symmetric or asymmetric. Adhesive layer(s) is (are) homogenous and isotropic material. They are modeled as continuously distributed non-linear (softening) tension/compression and shear springs. In this method by employing constitutive, kinematics and equilibrium equations, sets of differential equations for each inside and outside of overlap zones are derived. In the inside of overlap zone, the set of differential equations is non-linear, that is solved numerically. By solving these equations, shear and peel stresses in adhesive layer(s) as well as deflections, stress resultants and moment resultants in the adherends are determined. Most of adhesives have non-linear behavior, therefore unlike previous methods, in which the adhesive layers are modeled as linear materials, in the presented approach the non-linear behavior is assumed for the adhesive layer and can be used to analyze the most of adhesive joints. The numerical results reveal that in the inside of overlap zone, magnitudes of shear forces are considerably large due to high rate of variation in the bending moments. The developed results are successfully compared with those obtained by finite element analysis using ANSYS. The comparisons demonstrate the accuracy and effectiveness of the aforementioned methods.Keywords: Composite, Adhesive Joint, Adherend, Peel Stress, Shear Stress
-
Page 111This paper focuses on using the recently developed extended finite element model for buckling analysis of edge cracked columns under concentric axial load. The effect of crack depth and its location on the carrying capacity of columns is studied. The effect of different boundary conditions is also investigated. Numerical examples are offered to show the efficiency and effectiveness of the proposed method. The presented results are compared with analytical and experimental works available in the literature. Good agreement with experiment is shown, although the difference with analytical results is considerable for columns with deeper cracks. The reason of this difference is discussed. It is shown that the proposed method is more accurate than the analytical methods which are developed based on rotational spring models.Keywords: Buckling, Column, Crack, XFEM
-
Page 121force convection heat transfer of turbulent nano fluid flow in 90 and 60 degree elbow is simulated by using FLUENT. Single phase model has been implemented to study such a flow field and standard .Keywords: Nano, fluid, forced convection heat transfer, Turbulent flow, FLUENT, Circular elbow
-
Page 129Induction motor bearing is one of the key parts of the machine and its analysis and interpretation are important for fault detection. In the present work vibration signal has been taken for the classification i.e. bearing is Healthy (H) or Defective (D). For this purpose, clustering based classification of bearing vibration data has been carried out using Principal Component Analysis (PCA) and Self Organising Map (SOM). From the vibration signal, twelve statistical features have been extracted from both the healthy and the defected condition of the bearing. Further, these data are subjected to PCA to extract significant features relevant to cluster structure. It is observed that out of twelve features only four features are found significant which is feed to the SOM model. The SOM based classification is able to achieve an accuracy of 100%. This cluster-based method of feature reduction and classification could be useful in assessing the induction motor incipient bearing fault detection with large data set.Keywords: Bi plot, Principal Component Analysis, Self, Organising Map, Statistical Features Vibration Signal
-
Page 137Although carbon nanotubes (CNT) have been employed as reinforcements in nanocomposites, presence of nano scale defects such as Stone-Wales and vacancy defects in carbon nanotubes (CNT) weakens the mechanical properties of these materials. In this paper the effects of defects in CNTs on nanocomposite elastic behavior are investigated using molecular dynamics. Stiffness matrices of CNT and nanocomposite indicated the transversely isotropic behaviour of nanocomposite molecular model. Longitudinal and transverse Young's moduli for both perfect and defected CNT/epoxy nanocomposites are determined. A comparison between the results illustrates that the number and type of CNT defects have significant effects on mechanical behaviour of nanocomposite. Based on molecular dynamics results, CNT defects significantly affect the Young's modulus particularly in the transverse direction. Comparison between molecular simulation predictions and rule of mixtures results indicates that some correlation factors must be incorporated when using the micromechanical theories at nano scales.Keywords: nanocomposite, defect, CNT, Stone, Wales, Vacancy