فهرست مطالب
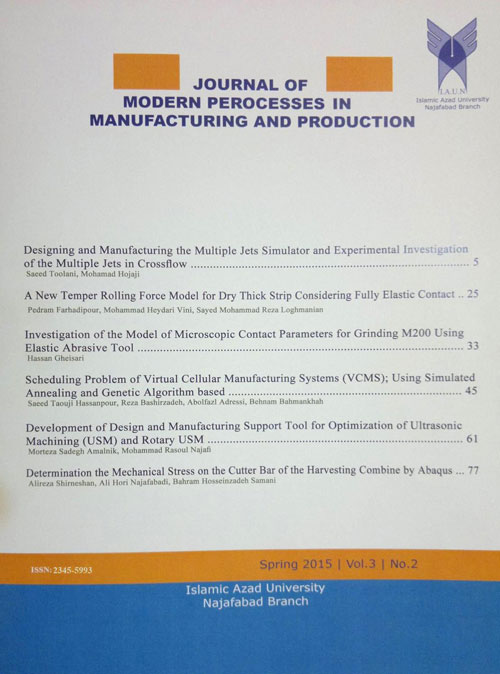
Journal of Modern Processes in Manufacturing and Production
Volume:3 Issue: 4, Autumn 2014
- تاریخ انتشار: 1393/10/18
- تعداد عناوین: 6
-
Pages 5-24Designing and manufacturing the multiple jets simulator and experimental investigation of the multiple jets in crossflow at low velocity ratios have been studied Together with design and build a low-speed wind tunnel. A specific rake is used to determine the flow field pressure and changes in static pressure measured by pressure taps in the near field of the jets. There are generally three regions on the pressure distributions whose details depend on the velocity ratio. Study the flow field and surface pressure distribution at low velocity ratios shows that by the increase the velocity ratio, the total pressure of the jet stream decreases sharply. The effects of increasing the number of jet injection nozzles showed that the influence on the jet stream in the vertical plane is significant. However, the influence of Normal multiple jets on the plate is reduced. It also increases the number of nozzles reduced the pressure coefficient rather than the single-jet injection.Keywords: Counter rotating vortex pair, Jet in crossflow, Jet simulator, Wake, Wind tunnel, Velocity ratio
-
Pages 25-32Temper rolling or skin pass rolling is one of cold rolling processes composed of a horizontal pass cold rolling mill stand. In this process, the thick strip is subjected to very light reduction (0.54%) in thickness in the presence of high friction amplitudes. One of the basic parameters of strip rolling processes is temper rolling force. A new rolling force model has been proposed for temper rolling strip mill considering the inhomogeneous stress distribution along the thickness of the strip. The contact between rolls and thick strip is totally elastic. The deformation field consists of an elastic (actually elastic) zone and that is highly non-homogeneous across the thickness of the strip. Totally elastic formulation can be used to predict the roll force. It can be used to study the stress distribution along the thickness of strip. The computing results from this model coincide the similar presented results in previous investigations done.Keywords: Temper rolling mill, rolling force, elastic contact, strip
-
Pages 33-44In this study; utilizing the elastic matrix ball has higher processing efficiency and better superficial quality than traditionalgrinding. The diversity of elastic abrasive tool characteristics contact with bend surface results in irregular wear abrasion,and abrasive tool machining status gets complicated. There is no theoretical interpretation of parameters affecting the grinding accuracy. Because of corrosion resistance, wear resistance and other characteristics of M200 material, it is often used as a material in aerospace precision components. In the study, grinding and polishing experiments has been carried out by using material of M200 to theoretically show the relationship between stress magnitude and grinding efficiency, and to predict the optimal combination of grinding parameters for effective grinding. Just in order to achieve the high abrasion resistance features of M200, the micro-contact of elastic ball abrasive tool (Whetstone) was analyzed, mathematical methods were used todeduce the functional relationship between residual peak removal rate and the main parameters which impact the grinding accuracy on the plane case. Thus they lay the foundation for the study of elastic abrasiveprediction and compensation.Keywords: Flexible abrasive tool, Hertz theory, polishing parameters, Removal rate
-
Pages 45-60In this paper, we present a simulated annealing (SA) and a genetic algorithm (GA) based on heuristics for scheduling problem of jobs in virtual cellular manufacturing systems. A virtual manufacturing cell (VMC) is a group of resources that is dedicated to the manufacturing of a part family. Although this grouping is not reflected in the physical structure of the manufacturing system, but machines are spread on the shop floor physically. In this paper, there are multiple jobs with different manufacturing processing routes. First, we develop the mathematical model for the problem, and then we present the suggested algorithms. The scheduling objective is weighed tardiness and total travelling distance minimization. The problem is divided into two branches: small scale and large scale. For small scale, the results of GA and SA are compared to GAMS. For large scale problems, due to the time limitation of 3600 seconds, the results of GA and SA are compared to each other. Computational results show that both SA ad GA algorithms perform properly but SA is likely to turn out well in finding better solutions in shorter times especially in large scale problems.Keywords: Virtual cellular manufacturing systems, Scheduling, simulated annealing, genetic algorithm, mathematical formulation
-
Pages 61-82Computer-integrated manufacturing (CIM), technologies are presented as solutions to manufacturing organizations, which need to perform well in all customer-related dimensions simultaneously. In the literature, CIM technologies providing such benefits as more frequent production changes, reduced inventory level, improved ability of producing complex parts with a high degree of accuracy and repeatability, considerable savings in scrap and rework, lower manufacturing lead-times. In this paper a general model and architecture of CIM for Irankhodro auto industry is designed. Also for each function or subsystem a model is design in CIM environment. The Model has three rings. First ring including three sections: data management, data representation and communication. Second ring is decision support system (DSS) including three sections: DSS for design, DSS for manufacturing and DSS for management. Third ring including all functional area including marketing, design, process planning, manufacturing, production planning and control, quality control, warehouse, management, Finance etc. Also For design of CIM system seven levels is considered including: at business level, at facility level, at shop floor level, at cell level, at workstation level, at machine level, at sensor level. Also CIM model of Iran is based on the seven layers of standard namely open system interconnection (OSI) defined by ISO. IranKhodro auto industry briefly introduce and its barrier and problem for implementation of CIM is discussed. The main objective of this paper is design of a CIM for Irankhodro Automotive Industry in Iran.Keywords: CIM, integration, Manufacturing, Irankhodro, Data management, Communication
-
Pages 83-92Equal channel angular rolling (ECAR) is a severe plastic deformation method that covered plastic deformation of sheets. In this study, effects of ECAR route shave been investigated on the mechanical and microstructure properties of explosive-welded Al-Cu bimetal. At first, the explosive welding process has been performed to prepare the Al-Cu bimetals. Then, to relieve the stress and preparing of samples for ECAR process, the annealing process of the samples was done. Finally, the ECAR process was performed on the samples in two routes A and C. Results showed that yield and tensile strengths and micro hardness of ECARed samples significantly increased with increasing the number of passes, whereas their ductility decreased. The yield strength of bimetals has been increased from 80 MPa to 100 MPa and 130 MPa at the routes A and C, respectively. Also, with increasing the number of ECAR passes, the grain size of the ECARed bimetals decreased to about 2μm.Keywords: ECAR, Explosive Welding, Mechanical Property