فهرست مطالب
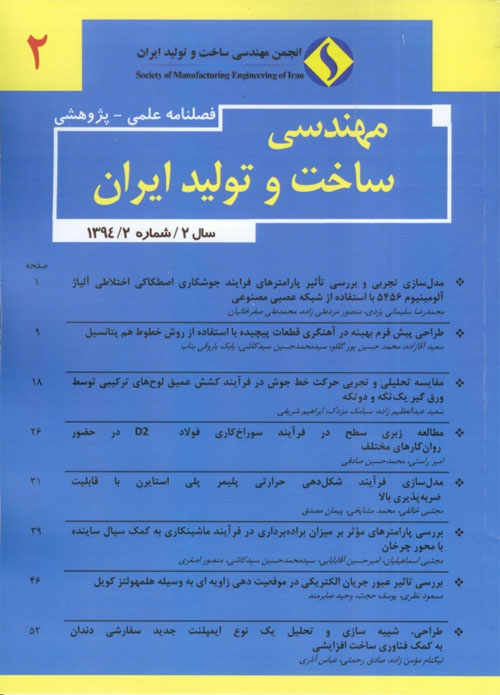
مجله مهندسی ساخت و تولید ایران
سال دوم شماره 2 (تابستان 1394)
- تاریخ انتشار: 1394/05/13
- تعداد عناوین: 7
-
-
Pages 1-8Friction stir welding is a solid state process developed by the welding institute TWI in 1991¡ as a technique for welding aluminum alloys. In this research¡ lap joint welding of 5456 aluminum alloy was carried¡ so that the hard working H321 sheet with the thickness of 5 mm was placed on an annealed sheet with the thickness of 2.5 mm and has been investigating the simultaneous effects of parameters such as rotational speed¡ feed rate¡ and tool angle¡ on failure force parameters and the hook disadvantage height in friction stir welding were investigated. After evaluation and analysis of the welded samples; the modelling of multilayer perceptron neural network was carried out using experimental results¡ and for the purpose of the trained model verification¡ several verification models was performed where the results of failure force in training model show 2.017 percent average error with respect to the experimental results. Next¡ the multilayer perceptron neural network was used for investigating the effect of welding parameters as in single or group mode on welding mode variations¡ where rotational speed parameter has the greatest effect and tool angle has the least effect than the other two parameters in lap joint friction stir welding.Keywords: Friction Stir Welding, 5456 Aluminum Alloy, Lap Joint, Artificial Neural Network
-
Pages 9-17Design of appropriate preform while considering geometry complication and maximum allowable strain into part¡ may result in appropriate die filling¡ forging load reduction¡ increasing tool life¡ and improving the material property of manufactured part. In this paper¡ preform design for long and asymmetrical steel parts using equipotential lines and mass distribution methods is performed. Then the results of the finite element simulations have been compared with the experimental tests. The electric potential difference generated between billet and final part¡ and equipotential lines between them are extracted using ABAQUS software. After design of experiments¡ and analysis in the DEFORM-3D software¡ while keeping the necessary force of forming and variance of stress and strain to minimum¡ the best preform has been selected among other preforms. Finally¡ forging die is manufactured and tested based on the designed preform using equipotential lines method. For the purpose of performance verification¡ comparison between equipotential lines and traditional mass distribution methods has been performed¡ where the results showed %45 uniformity in strain distribution¡ %12 reduction in forging loads and 137 grams saving in initial raw material.Keywords: Preform, Equipotential lines method, Design of experiments, Finite element simulation
-
Pages 18-25A tailor-welded blank (TWB) composed of two or more sheet metal with different ductility properties¡ that its main advantage is a weight loss product and production costs without compromising product safety. Tailored welded blanks are increasingly used in the automotive industry. Weld-line movement in tailored welded blanks is always considered as a challengeable problem¡ during production process. Compared to the base metal¡ the formability of tailor welded blank is less due to the presence of weld area and strength mismatch between component blanks. Weld-line movement is one of the parameters¡ having effect on sheets plasticity. The aim of this paper is compare the weld-line movement in different parts of the tailored welded blank between the blank holder blank one-piece and two-piece. For this purpose¡ in this article a three dimensional finite-element simulation has been carried out. In this regard¡ a deep drawing tool is manufactured for validation¡ and comparison has been performed between simulation and experimental results¡ being obtained from deep drawing of TWB''s¡ with having different thickness and different weld-line location. Argon welding is used for manufacturing tailor welded blanks before forming and tensile test. Finally¡ using surface response technique¡ simulation is done to investigate the effect of punch and die''s radius¡ weld-line situation and thickness rate¡ on weldline movement and thickness distribution in square TWBS.Keywords: Deep Drawing, Sections Square, Tailor Welded Blanks
-
Pages 31-38Thermoforming process is one of the common and low cost methods of forming thermoplastic polymers and producing high quality products. This method is used for producing industrial products and packaging products such as food storage containers. In this research¡ finite element modeling of the thermoforming process is carried out and the effects of process parameters on the quality of final product are investigated. In this research¡ Maxwell viscoelastic constitutive equation is adopted and simulation of a high impact polystyrene (HIPS) polymeric specimen with rectangular shape is carried out in ABAQUS finite element software. Constitutive equations of material behavior are implemented in a user defined material subroutine (UMAT). User subroutine verification is carried out by simulation of pure shear test in constant strain rate loading. Considering uniform thickness of the final product as criteria of product quality¡ the effects of four parameters namely¡ friction coefficient¡ plug velocity¡ sheet dimension and temperature on the quality of the final product are investigated. The results of process simulation shows that the friction coefficient between die and work piece has the most significant effects on the uniform thickness distribution of the final product.Keywords: Modeling of Thermoforming, Thermoplastic polymer, Viscoelastic behavior
-
Pages 39-45Abrasive flow machining is a new method of metal surface machining which polishes the surfaces and edges of complex or small industrial parts with high quality and close tolerances. In this method¡ a fluid containing abrasive particles passes on the surface or inside of the work piece in a reciprocating way. During the process¡ the work-piece reaches the desired surface roughness over time. The main problem in using this method is the low removal rate¡ and thus longer leadtime to carry out the process. In this study¡ abrasive flow machining process is simulated in Fluent software using discrete phase model¡ and then to increase the rate of material removal¡ centrifugal force imposed by the rotating rod is applied. Simulation was performed for the material removal of inner wall of a pipe. Moreover¡ the influence of the axis rotational speed parameters¡ the mass fraction of abrasive particles and number of removal cycles on material removal rates were evaluated. Also¡ based on the response surface method¡ a series of experiments were designed¡ and the effects of input parameters and their interactive effects on the rate of material removal were evaluated by analysis of variance method. Finally¡ a regression model is provided to predict the removal rate in the process according to the effective parameters.Keywords: Abrasive flow machining, Material removal, Rotating rod, Simulation
-
Pages 46-51In this paper¡ it has been tried to position and rotate a magnet using two pairs of Helmholtz coils. First the system was simulated by software and the impact of electric current flowing through the coils and magnetic fields that create the space between them¡ was observed. Next¡ the required equipment and coils for magnetic angular positioning and testing was designed and built. Electrical circuits¡ computer software and microcontroller are responsible for exerting the required voltage¡ and as a result the necessary current to position the proposed robot¡ which includes chip particles¡ compass and a small magnet. After applying various electric currents to the coils¡ the magnet position was determined using a rotary encoder. And eventually values obtained from tests were compared with the values obtained from the theoretical equations and the system error at different flows was evaluated. At last magnet was continuously rotated by applying sinusoidal currents¡ where rotational speed was measured up to one Hertz.Keywords: Helmholtz coill, Maxswell coil, Magnetic torque, Gradient magnetic field
-
Pages 52-58Available Online 24 February 2016 In this article a novel methodology was developed for using different dental implants sizes according to patients requirements¡ while avoiding the limitations of common standard sizes of dental implants available in world market. This research involves simulation¡ design and analysis of customized dental implants using patients jaw CT Scan images¡ used for fabrication by Additive Manufacturing Technology. Customized dental implants not only cause a more appropriate joint of jaw bone and implant¡ but also reduce the time that it takes to build an implant by AM technology. The case study in this research is a 43 years old man who needs 3 dental implants which are designed in this research for the purpose of AM¡ and are suitable alternatives for his lost teeth; because minimum stress (as compared with other designs) is exerted at the contact surface between the implant and bone. Utilizing vertical grooves on implant surface and conical thread play an important role in reduction of tension that is applied to the joint of implant and jaw. Conical thread grooves which are not cost effective to be produced via common techniques¡ are the best type of grooves for dental implants. As this design is dedicated to the additive manufacturing technology¡ hence it is the best choice for better integration between the implant and bone. Less lead-time and less human intervention during treatment are the additional benefits of this novel methodology.Keywords: Additive Manufacturing, Rapid Prototyping, Customized Implant, Abutment, Fixture, Finite Element