فهرست مطالب
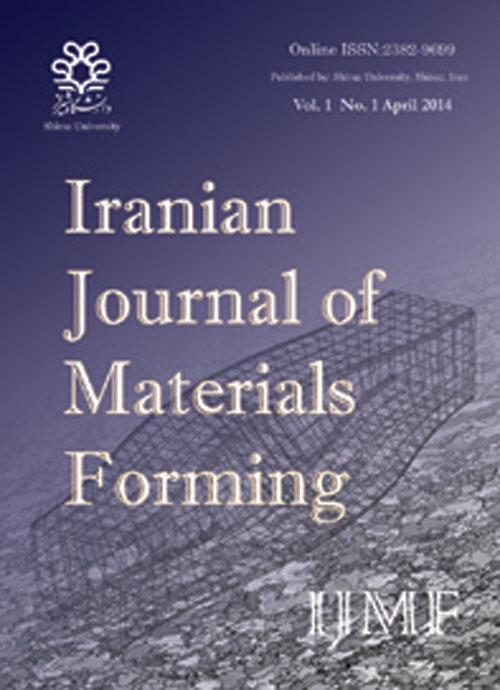
Iranian Journal of Materials Forming
Volume:5 Issue: 1, Winter and Spring 2018
- تاریخ انتشار: 1397/04/03
- تعداد عناوین: 7
-
-
Pages 1-18In this study, the incremental forming of explosively welded low carbon steel-commercially pure titanium bilayer sheet has been experimentally and numerically investigated. For this purpose, at first a finite element based analysis was proposed to predict forming force and thickness distribution to form this material by such process, that showed good agreements with the experimental results. Then, to investigate the effect of vertical step down (ΔZ) parameter on the properties of the workpiece, mechanical tests and microstructural studies were performed on the formed specimens. The results showed that increasing the vertical step down (ΔZ), hardness and tensile properties of the specimens increased but the thickness reduction in the wall of the pyramidal specimens increased and also the surface quality decreased. In addition, microstructural studies showed that increasing the vertical step down from 0.1 to 0.3, the grain structure transformed from an equiaxed state to a fibrous state and led to formation of texture in the microstructure, which mechanical properties improvements can be attributed to this issue. Therefore, if the surface quality of the inside wall of the specimen wont be important, with an increase in the amount of ΔZ besides reduction of process time, the mechanical properties of the specimen will be improved.Keywords: Incremental Forming, Explosive-welded, Bimetals, low carbon steel-CP Titanium
-
Pages 19-25A microstructure consisting of ultrafine grained (UFG) ferrite with average grain size of ~ 0.7 µm and dispersed nano-sized carbides was produced by cold-rolling and tempering of the martensite starting microstructure in a low carbon steel. Subsequently, fine grained dual phase (DP) steel consisting of equiaxed ferrite grains with average size of ~ 5 µm and martensite islands with average size of ~ 3 µm was produced by intercritical annealing of this microstructure. Coarse grained DP steel with average ferrite grain size of ~ 20 µm and average martensite island size of ~ 5 µm was also produced by intercritical annealing of the as-received ferritic-pearlitic microstructure. The UFG microstructure showed high strength, low ductility, and poor work hardening response due to intense grain refinement. The fine grained DP steel had higher tensile strength and total elongation compared with the coarse grained one, which was related to the improved work-hardening behavior by microstructural refinement.Keywords: DP steels, Microstructure, Mechanical properties, Thermomechanical processing
-
Pages 26-35Since tubes have numerous industrial applications, different attempts are focused on the severe plastic deformation processes of tubes. As an illustration, tube channel pressing (TCP) is an attractive process for this purpose since it can be used for processing of different sizes of tubes. However, more attempts are needed to improve the outcomes of TCP. For example, imposing of a greater strain besides reductions of the strain heterogeneity are the challenges of this process. This work is aimed to optimize the die geometry of TCP through a finite element simulation procedure verified by experiments in order to increase the imposed strain as well as to decrease the strain heterogeneity. Results show that the increase of die curvature radius causes decrease of imposed plastic strain and increase of strain heterogeneity. In addition, the minimum amount of die convex height for imposing of a reasonable strain through TCP is calculated considering the tube thickness and the channel angle. Besides this, the optimum die geometry is recommended in order to minimize the strain heterogeneity.Keywords: Severe plastic deformation, Finite element simulation, Strain analysis
-
Pages 36-46The hot deformation behavior of a typical martensitic stainless steel containing 2.1% Ni was investigated by means of the compression test in the strain rate range of 0.001-1 s-1 and temperature range of 950-1150 °C. The flow behavior of the steel was evaluated using the flow stress curves and flow softening map and by microstructural investigation. Taking into account of the strain effect on the hot deformation behavior, the Z and Q maps were plotted as a function of the strain rate and the strain. In order to obtain the optimum hot deformation regime, the m-map was constructed. It was found that, all restoration mechanisms i.e. dynamic recovery and dynamic recrystallization phenomena take place at different hot working conditions. It was also found that, the dominant softening mechanism at different hot deformation domain depends upon Z parameter. According to the flow curves and also Z, Q and m maps, the optimum hot deformation conditions have been obtained as: strain range of 0.25-0.5, the temperature range of 1000-1100 °C and strain rate of 0.01-0.1 s-1.Keywords: Martensitic stainless steel, Flow curves, Processing maps, Strain effect
-
Pages 47-57Tailor-made blanks are sheet metal assemblies with different thicknesses and/or materials and/or surface coatings. A monolithic sheet can be machined to make the required thickness variations that is referred as tailor machined blanks. Due to the thickness variation in tailor machined blanks, laser bending of these blanks is more complicated than monolithic plates. In this article, laser forming of tailor machined blanks is investigated and an artificial neural network (ANN) will be configured to predict the bending angle of laser formed tailor machined blanks. The input parameters of neural network are selected as start point of scan path, laser irradiating method, laser beam diameter, laser output power and number of radiation passes. The results show that a 5×8×1 trained neural network can predict the bending angle with acceptable accuracy. Comparison of the randomly selected tests with experimental results shows 1.1% error in the prediction of bending angle by trained artificial neural network.Keywords: Tailor machined blank, Laser forming, Artificial neural network, Bending angle
-
Pages 58-70Deep drawing of two-layer sheet is a suitable way to achieve product with a desired shape and desired properties in sheet metal forming technology. Control of deep drawing parameter such as thinning is the most important challenge in this process. The most difficult part of this challenge is differences in material properties and geometry of each layer. In this paper, numerical approach has been exploited to plan and control of two layer deep drawing process. For this purpose, the three-dimensional (3D) finite element has been used. ST14 Al1100 (A.I. and S.I. lay-up) were selected as materials of two layer sheet metal. The results of simulation have been validated with experiments. Based on numerical study, effect of process parameters on the percentage of thinning, maximum plastic strain, rupture, required forming force and blank holder force (BHF) has been studied. This study has also been done on one-layer sheet metal and differences between deep drawing of one-layer and two-layer sheets have been comprehensively investigated. The results showed that maximum thinning is occurred in the upper layer of die radial region as well as in the lower layer of punch radial region. Also, the maximum equivalent plastic strain in the lower layer is more than the maximum of equivalent plastic strain in the upper layer.Keywords: Deep drawing, two layer sheet, Finite element method, Equivalent plastic strain, Forming Force
-
Ten years of severe plastic deformation (SPD) in Iran, part I: equal channel angular pressing (ECAP)Pages 71-113The superior properties of ultrafine-grained materials fabricated by severe plastic deformation (SPD) have attracted the attention of many researchers around the world. Among the top-ranked countries that are active in this field, Iran is interesting because of the late beginnings of SPD in this country and, subsequently, the highest rate of growth in the number of publications during the last decade. The first Iranian work published in the field of equal-channel angular pressing (ECAP) goes back to 2007, meaning that SPD research covers a period of only about ten years. Nevertheless, since that time there has been an increasing growth rate in the number of Iranian publications dealing with ECAP and especially the introduction of new methods based on ECAP and simulation of the method. The present overview is designed to summarize the main contributions from Iran in the field of ECAP processing. Interestingly, the main contribution of Iranian researchers in ECAP is focused on simulation/modelling and the introduction of new methods of SPD based on ECAP.Keywords: Severe plastic deformation, Equal-channel angular pressing, Ultrafine-grained materials, Mechanical properties