فهرست مطالب
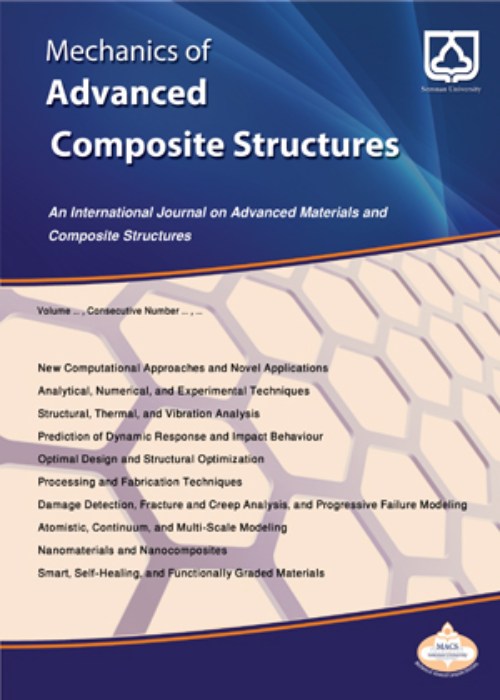
Mechanics of Advanced Composite Structures
Volume:11 Issue: 1, Winter-Spring 2024
- تاریخ انتشار: 1403/01/13
- تعداد عناوین: 18
-
-
Pages 1-9It is essential to improve thermal insulation. In this study, titanium dioxide (TiO2), magnesium oxide (MgO), and vanadium pentoxide (V2O5) were used as additives to modify phenolic novolac resin by the solution mixing method. Different weight percentages of resin nanoparticles (NPs) were added, and nanocomposites with different weight percentages were prepared. These nanocomposites were investigated by field emission scanning electron microscope (FE-SEM), X-ray diffraction spectroscopy (XRD), and oxyacetylene flame test (OFT). The FE-SEM images showed that the NPs were dispersed on the surface of the novolac resin at low concentrations. However, at high concentrations, the dispersion was suppressed in some cases by aggregation in the nanocomposites. The OFT test proved that by increasing the content of NPs in the nanocomposite, the back surface temperature of the sample decreased, thus improving the thermal insulation properties.Keywords: Novolac resin, Titanium Dioxide, Magnesium oxide, Vanadium pentoxide, Nanocomposite, Thermal insulation
-
Pages 11-40In this study, the hygrothermal flexural behavior of a nanocomposite plate reinforced with carbon nanotubes is analyzed. The Eshelby-Mori-Tanaka (EMT) technique, a micromechanical model based on two parameters, is used to calculate the nanocomposite plate's real mechanical properties. The model incorporates the effects of clustering. The virtual work notion from higher-order shear deformation theory (HSDT) is used to develop the governing differential equations. After that, a C0 continuous isoparametric Lagrangian FE model with seven nodal unknowns is used to apply the present method with the FEM. Creating the finite element code allows one to calculate the nanocomposite plate's deflection. To make sure that the method works, the results are compared to numerical results that have already been published. The flexural response of the nanocomposite plate with agglomerated carbon nanotubes (CNTs) is next analyzed by performing extensive parametric studies to determine the impacts of agglomeration degree, moisture, temperature, the volume percentage of CNTs, and various aspect ratio.Keywords: CNT, Agglomeration, high-order shear deformation theory, Hygrothermal Environment
-
Pages 41-58
This study aims to investigate the effect of functionally graded materials (FGMs) on the internal resonances of nanorods in torsional vibration. The von-Kármán type nonlinearity is considered and the governing equation of motion is derived using Hamilton's principle based on the surface elasticity theory. It is assumed that the properties of the functionally graded (FG) nanorod vary through the radius direction based on power-law distribution. Then, the multi-mode Galerkin method is implemented to convert the partial differential equation to an ordinary differential one. In the next step, the method of multiple scales is used to derive the natural frequencies as well as the conditions in which the internal resonances occur. The results are presented for two types of end conditions, fixed-fixed and fixed-free, and the effects of variations of various parameters like length, radius, and amplitude of vibration on natural frequencies are investigated. This research shows that functionally graded materials differ in the state of happening the internal resonances in the presence of the surface energy.
Keywords: Torsional vibration, Von-Kármán type nonlinearity, Surface elasticity theory, Internal resonances, Multiple scale method -
Pages 59-72In the present paper, the effect of aspect ratio on the initial buckling response of an elastically supported rectangular FGM plate, the thin plate spline radial basis function (RBF) method can be used. This method involves the use of a thin plate spline to interpolate the displacement field of the plate, allowing for accurate analysis of the plate's behavior. The higher-order shear deformation theory (HSDT) is used for the analysis of the FGM rectangular plate resting on two parameters of elastic foundation. The displacement field consists of five unknown variables and approximately parabolic distribution of the transverse stress profile through the plate thickness and tangential stress-free boundary conditions on the plate surface. The governing differential equations (GDEs) of the plate are developed in the framework of Hamilton’s principle. The thin plate spline radial basic function-based Meshfree method is used for discretizing the GDEs. To demonstrate the accuracy and efficacy of the present approach, the results obtained by the present approach are compared with the results given in the literature. The effect of various aspect ratios, grading index, span-to-thickness ratio, and two parameters of elastic foundations on the normalized buckling load is proposed. Some new results are also presented, which may be beneficial for future research works. The novelty of the present is the effects of aspect ratio on the elastically supported FGM plates.Keywords: FGM Plate, Spline RBF, Meshfree, Buckling, Foundation, Aspect Ratio
-
Pages 73-86Cellulose is one of the most widely used and widely available materials on the planet, and it has been used for centuries in a wide range of applications. In this paper, a new source of cellulose delonix regia fruits has been explored for the extraction of cellulose at the micro and nanoscale. Cellulose is isolated from the raw delonix regia fruits by sub-sequential chemical methods such as pulping, bleaching, delignification, and acid hydrolysis. PVA/CMF and PVA/CNF composites are prepared by the solvent casting process with 1, 3, 5, 7, and 9 percentages of filler concentration. Mechanical, thermal, morphological, moisture absorption, and biodegradability properties of pure PVA, PVA/CMF, and PVA/CNF composite at different filler concentrations were evaluated using mechanical testing (tensile, flexural, and impact), TGA-DTG, SEM, moisture absorption test and soil burial test respectively. The SEM results showed that at increased filler content concentrations, signs of agglomeration began to occur, and the overall performance of the resulting composite material degraded due to which filler addition should be limited to less than 7wt%. Tensile, flexural, and impact test results revealed that nano-fillers performed better than micro-fillers, and the best performance is obtained with filler content below 7%. The degradation temperature of composites with filler content improved dramatically, according to TGA and DTG curves, and composites with nano-fillers had greater thermal stability than composites with micro-fillers. The inclusion of filler content reduced the tendency of composite materials to absorb moisture and the resulting composite materials had enough biodegradation rate together with higher lifetime and performance, according to the findings of the biodegradability test and moisture absorption test.Keywords: Bionanocomposite, Delonix Regia Fruit Fibers, Mechano-chemical treatment, SEM, Mechanical Test, Biodegradability
-
Pages 87-102Fiber-reinforced composite tubes offer numerous advantages over traditional metal tubes, including lower weight, higher strength and stiffness, corrosion resistance, and fatigue resistance. These tubes have the potential to act as energy absorbers, making it crucial to understand the factors influencing their energy-absorbing characteristics. This study focuses on experimentally investigating the crashworthiness of woven glass/epoxy composite tubes by analyzing the effects of the inner diameter and the extent of overlapping dropped-off plies. Circular cross-sectional tubes with different diameters (20, 25, and 30mm) and varying extents of ply overlap (0, ¼, ½, ¾, and 1 times the circumference) are subjected to impact loading and quasi-static compressive loading. The length-to-diameter ratio remains constant across all cases. The investigation examines the influence of the inner diameter and the extent of overlapping plies on parameters such as mean crushing force, energy absorption, specific energy absorption, crush force efficiency, and stroke efficiency, and compares the damage and failure mechanisms observed in different composite tube configurations. The results highlight that specimens with smaller diameters and a half overlap exhibit maximum crush load efficiency, contrary to specimens with larger diameters and full overlap. This study emphasizes the significance of considering the extent of overlapping and its geometry to tailor the energy absorption characteristics of composite tubes for specific applications.Keywords: Composite tubes, Energy absorbers, ply drops, Dropped-off plies, Specific energy absorption
-
Pages 103-118Aerospace, transportation, marine, and space applications demand structural materials with low densities yet strong, hard, and high impact strength. Composites are materials that satisfy the needs of recent technology. Composites are flexible materials that meet the demands of modern technologies. Herbal fibers may be processed and need little energy. Using natural fibers as reinforcement in polymer composites to create inexpensive building materials has recently gained popularity. The experimental and FEA analysis of woven bamboo and jute fiber reinforced in epoxy composites is the main emphasis of the current work. Mechanical properties such as tensile and flexural properties are evaluated for various stacking sequences. Also, numerical analysis is done using licensed Hyper mesh software. The S1 stacking sequence's testing findings had the highest tensile strength (47.411 MPa) and tensile modulus (695.44 MPa). Additionally, it has the highest flexural strength and modulus at 80.25 MPa and 9.065 GPa, respectively. FEA results deviate by more than 10%. Excellent mechanical characteristics are achieved with a fiber volume fraction of 10% bamboo, 20% jute, and 70% matrix material. The SEM images showed the composite’s interface breakdown between the textiles' layers.Keywords: FEA, Bamboo, Jute, Stacking, Tensile, Flexural, SEM
-
Pages 119-130In this paper, the elastoplastic behavior of a rotating thick cylinder is investigated. High-order shear deformation theory (HSDT) is used to define the displacement field. The cylinder is considered to be fixed at both ends and rotates around its axis with specific angular velocity. The cylinder is also made of functionally graded material (FGM), and the properties of the material are changed gradually from the inner to the outer surface. The material is supposed to be elastic-perfectly plastic and the von Mises yield criterion is used to define the state of stress. The Prandtl-Reuss flow rule is used to express the stress-strain relation in the plastic region. The radial return mapping method is applied to compute the elastoplastic stress field. The equilibrium equations and general boundary conditions of the cylinder are derived using the energy method. The elastic limit pressure and the stress analysis of the FG rotating thick cylinders have been obtained by solving the equations derived based on HSDT. The influence of the inhomogeneity constants and angular velocity of the cylinder are studied. The results are evaluated with the finite element method using Abaqus software. The main novelty of the study is investigating shear stress in the elastoplastic analysis of cylindrical shells. The results revealed that using the HSDT with the radial return mapping method has enough accuracy for the elastoplastic analysis of clamped-clamped thick cylindrical structures.Keywords: Elastoplastic analysis, Shear Deformation Theory, Prandtl-Reuss flow rule, Radial return method, Thick cylindrical structure
-
Pages 131-148
In this paper, the nonlinear dynamic analysis of porous annular sandwich plates reinforced with graphene platelets (GPLs) under different boundary conditions is investigated. The Gaussian Random Field (GRF) alongside with Halpin-Tsai micromechanics model are used for the variational Poisson’s ratio and effective material property of the GPLs which are distributed in two forms of symmetric and non-symmetric patterns with different porosity dispersion models. Using Von-Karman nonlinear relations and different plate theories, the time-dependent governing equations are obtained and then solved using the dynamic relaxation (DR) method combined with implicit Newmark’s integration technique. Finally, some key elements namely: GPL weight fractions and distributions, porosity coefficients and dispersions, different loadings, boundary conditions, and the effects of thickness-to-radius ratio are discussed in detail. The results show that with an increase in porosity, the difference between the results of FSDT and MHSDT greatens. Also, a significant increase in plate stiffness is observed by adding a small amount of GPL to the porous core of the sandwich plate.
Keywords: Sandwich porous plates, GPLs, nonlinear dynamic analysis, MHSDT, Newmark’ s integration method -
Pages 149-158This study presents an analytical solution for static buckling and free vibration analysis of bi-dimensional functionally graded (2D-FG) metal-ceramic porous beams. To achieve this goal, equations of motion for the beam are derived by using Hamilton's principle and then the derived equations were solved in the framework of Galerkin’s well-known analytical method for solution of equations. The material properties of the beam are variable along with thickness and length according to the power-law function. During the fabrication of functionally graded materials (FGMs), porosities may occur due to technical problems causing micro-voids to appear. Detailed mathematical derivations are presented and numerical investigations are performed, while emphasis is placed on investigating the effect of various parameters such as FG power indexes along both directions of thickness and length, porosity, and slenderness ratios (L/h), on the non-dimensional frequency and static buckling of the beam based on new higher deformation beam theory. The accuracy of the proposed model is validated based on comparisons of the results with the accepted studies. According to the result in both buckling and vibration analysis, the presented modified transverse shear stress along the thickness has shown closer consequences in comparison with TBT.Keywords: Porosity, Computational analysis, 2D-FGM, Composite materials, Buckling
-
Pages 159-176In the present study, a functionally graded cantilever beam has been analyzed to observe its deformation behavior and stress variations. While the material properties (modulus of elasticity, modulus of rigidity, and density) have been varied along the height of the beam, Poisson’s ratio has been considered a constant. The governing equations have been derived using Hamilton’s Principle in the framework of higher-order beam theory. The derived equations are then simplified to a single equation, which is similar to that of isotropic beams. However, the work is extended to include a few higher-order terms and to study the effect of the incorporation of these terms on the resulting FG beam behavior. The development of a single governing equation for studying the statics and dynamics of an FG beam with the incorporation of higher-order terms is a unique part of the report. The solution of the governing equation is approached using approximate methods; in this work, the B-spline collocation technique is used to arrive at the results. A sixth-order B-spline basis function is used as an approximating polynomial, and the Greville abscissa has been used to generate collocation points. The obtained results have been verified against standard literature to find a satisfactory match. The results include comparative plots for normalized bending and transverse shear stresses, with and without the inclusion of higher-order terms. The results are then extended to study the effect of material index on the deformation and stress behavior of FG beams. The effect of aspect ratio on results is also studied for comparison of various beam theories.Keywords: Functionally Graded Material, Hamilton Principle, B-spline Collocation, Power law, Axial stress, Shear Stress
-
Pages 177-190This study focuses on investigating how grid-stiffened composite shells behave under external hydrostatic pressure. The critical buckling load is calculated using the first-order shear deformation theory (FSDT) and the Ritz method. Various factors, including shell thickness, angle of helical stiffeners, rib section area, and the number of stiffeners, are examined to understand their impact on the buckling load. To optimize the design, three multi-objective optimization algorithms are employed: Nondominated Sorting Genetic Algorithm II (NSGAII), Multiobjective Particle Swarm Optimization (MOPSO), and a hybrid method that combines NSGAII and MOPSO. The hybrid method intelligently divides the population into two groups and uses NSGAII and MOPSO to efficiently explore and exploit the solution space. The results yield a Pareto optimal front that showcases diverse solutions across different regions, providing decision-makers with the flexibility to select the solution that best fits their preferences. The solutions obtained through these algorithms are compared based on their diversity and distribution throughout the Pareto front.Keywords: Grid Stiffeners, Buckling load, Composite Shell, multi-objective optimization, NSGAII, MOPSO
-
Pages 191-202Traditional engineering materials lack the necessary properties that are needed in aerospace as well as other modern industries. In order to address the aforementioned problem, a number of different materials are used in concert. With the help of functionally graded material, all the necessary characteristics can be achieved. A fast transition between two different materials can lead to debonding, thermal stresses, residual stresses, and stress concentrations; a gradual change in material properties might mitigate these problems. This work provides a comparison of the analytical solutions for the deflections in Two Dimensional Functionally Graded Taper Beam (2D-FGTB) under a uniformly distributed load, adapting Reddy’s higher-order shear deformation theory. All the material properties of the beam are graded along the thickness and length dimensions using the power-law formula. The thickness of the beam is assumed to change linearly along its length. Equations of motion are derived based on Hamilton's principle and Navier’s solutions. A parametric investigation is conducted to explore the effects of various material and geometrical parameters on the mechanics of 2D-FGTB. These parameters are found to be very significant in studying the static responses of 2D-FGTB.Keywords: Comparison of Deflection, Reddy’ s Higher Order Shear Deformation Theory, Two-Dimensional Functionally Graded Taper Beam, Hamilton' s principle, Static responses
-
Pages 203-216
Dynamic and buckling of a composite beam reinforced with a combination of carbon and aramid fibers is studied in this paper. The beam is under a thermal gradient through the thickness. Timoshenko beam is made of a polymer matrix (epoxy resin) reinforced with layers of high–strength carbon and high-toughness aramid fibers in order to create a balance between stiffness and toughness and create a type of structural composite beam with excellent strength and toughness. The mechanical and thermal properties of the hybrid composite beams are obtained based on the mixed law method. The equations of motion are extracted based on the Hamilton principle and then solved by the generalized differential quadrature method (GDQ). In this study, a thermal gradient is applied to the beam and then the vibration and buckling response of this hybrid composite beam are studied. The main contribution of this paper is the vibration and buckling responses of a hybrid composite structure strengthened by carbon and aramid fibers. The effect of the hybrid ratio as well as the stacking sequence on the free vibrations and critical buckling load are presented. The fundamental frequency and critical buckling load are largely affected by the stacking sequence. The conclusions show that the use of aramid fibers in the composite beam reinforced with carbon fibers decreases the natural frequency as well as the critical buckling load of the beam. The conclusions also show that for the symmetric hybrid composite beam, despite the critical buckling temperature being the same, the critical buckling load is different and depends on the location of the fibers.
Keywords: Carbon fiber, aramid fiber, hybrid ratio, Buckling load, vibration -
Pages 217-230The advent of metal fibers has led to the development of different fiber-reinforced composite systems via different manufacturing methodologies. Utilizing metal fibers as a single reinforcement can create completely new materials with unique physical structures and a synergistic effect on many properties. Steel, aluminum, titanium, and copper are examples of metal fibers used in industries such as aerospace, marine, automotive, and structural applications. Moreover, the possibility of combining various material systems (metal fibers - traditional fibers) to create hybrid composites allows for unlimited variation in cost and performance. In general, metals are available in the form of sheets as metal fiber metal laminate (FML), or as metal fibers in the form of fine wires, and mesh fibers. Investigation of fine wires and mesh fibers is still limited in the literature compared to the sheet metal form. Therefore, this work focuses on reviewing the processing techniques, properties, and applications of fine wires and mesh metals. In this paper, the application, methods of production, and several types and forms of metal fiber were described in detail. Moreover, the properties and applications of metal fibers reinforced polymer composite materials have been reviewed. The application of metalized fibers and the hybridization of metal fibers with synthetic and natural fibers reinforced polymer composites are also reviewed. To conclude, the potential of fine wires and mesh fiber forms, which are partially explored, seems to have excellent mechanical, thermal, and other material properties. Steel fiber is the most common metal fiber used due to its cost-effectiveness, availability in different forms, and high performance despite its heavy weight.Keywords: Metal Fibers, Steel Fibers, Hybrid composites, fine wires, mesh form
-
Pages 231-238The denier, cross-section, mass density, porosity, and depth of the nonwovens are the nonwovens' physical characteristics that depend on the thermally resistant layer. In this study, we use solid and hollow polyester fibers of various deniers to attempt to optimize these factors for extreme bulk nonwovens. An analysis of contributions has been done to determine the importance of thickness, spatial density, fiber fineness, and form. Better thermal insulation is provided by finer fibers. Nonwovens have a relatively high porosity, and their thermal resistance is particularly low for the lighter and thinner varieties. Thinner and lighter extreme cold-weather apparel is best made from hollow, finer fibers because of their higher thermal insulation. For any studied solid fiber nonwoven with constant thickness, the intrinsic thermal insulation of the nonwoven decreases with an increase in areal density. For 15 mm thick nonwoven, the maximum thermal insulation of 0.4522 m2K/W is obtained for nonwoven with an areal density of 100 g/m2 with 4 denier polyester solid fiber, and the minimum thermal insulation of 0.305 m2K/W is obtained for nonwoven with an areal density of 300 g/m2 with 10 denier polyester solid fiber. The same trends are obtained for nonwovens with thicknesses of 10 mm and 5 mm.Keywords: Nonwovens, Polyester fibres, Cold weather apparel, Thermal insulation
-
Pages 239-248Graphene was employed as filler in various formulations of jute fibers reinforced epoxy composites in this study. Graphene's influence on the physio-mechanical properties of epoxy-based polymer composite reinforced with jute was examined in terms of tensile strength, flexural strength, impact strength, hardness, and water absorption. It was found that the mechanical characteristics significantly improved. Also, a significant decrease in the proportion of water absorption was obtained. The optimal proportion of graphene filler in proposed composites is also discussed in the present study. The optimal concentration filler in the proposed composites was found to be 4%. The findings show that graphene is a promising material and graphene mixed with 36% jute in an epoxy-based composite effectively improves the composites' strength. The findings of this study demonstrate the potential of graphene powder in enhancing the physio-mechanical properties of jute-reinforced epoxy composites for automobile applications. The incorporation of graphene powder offers a promising route for the development of lightweight and sustainable materials that can meet the stringent requirements of the automotive industry in terms of strength, durabilityKeywords: Jute, Graphene, Hybrid composite, Physio-mechanical characterization, Sustainability
-
Pages 249-258
According to the properties of the pine tree trunk and its wide range of applications, finding its defects can play a vital role in reducing costs. Since the ultrasonic test is a non-destructive method, this method is an appropriate alternative to find defects in the pine tree trunks. Optimizing the ultrasonic non-destructive test is necessary because the correct choice of the ultrasonic test affecting factors increases the reliability of the test results. In this paper, at first, a simulation method for non-destructive ultrasonic tests in wooden parts using COMSOL Multiphysics software is presented. Both size and location of the defects have a considerable impact on the signal in the simulation. The defect size has a higher effect on signal amplitude and signal-to-noise ratio changes. So, the location of the defects is detected according to the amplitude of signals received in three points according to the method described in the paper. In the following, using the method of design of experiments, the effect of input factors containing frequency and signal amplitude on responses such as signal-to-noise ratio and loss of signal amplitude has been investigated. Results showed that these have an important effect on the output signal. Finally, the optimal simulation settings have been determined. According to the analysis, if the test frequency is 50 kHz and the amplitude of the input signal is 0.08 mm, the desirability value is equal to 100%, which indicates the high desirability of the ultrasonic test of wooden parts under the mentioned settings.
Keywords: Ultrasonic test, Simulation of waves, Signal-to-noise ratio, Detection of wood defects