فهرست مطالب
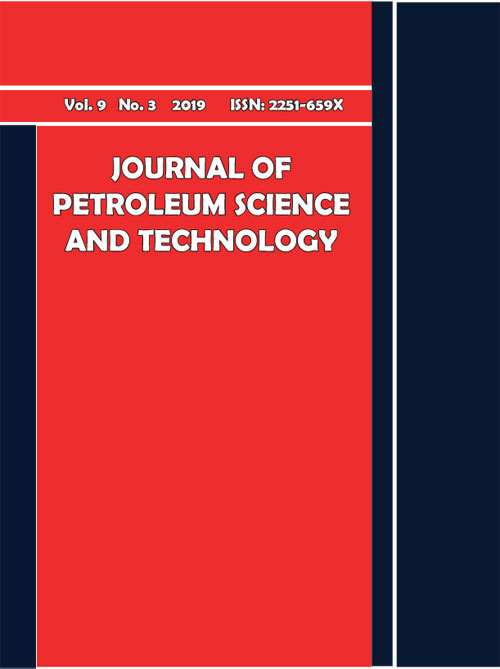
Journal of Petroleum Science and Technology
Volume:9 Issue: 3, Summer 2019
- تاریخ انتشار: 1398/05/15
- تعداد عناوین: 6
-
-
Pages 3-9Topanol A is a phenolic antioxidant additive, which is used in storage tanks for jet fuels produced in the petroleum refineries throughout the country. Topanol A mostly consists of 2,6-di-t-butylphenol. The conventional methods for the preparation of this compound involve ortho-alkylation of phenol using 2-methylpropene (isobutylene) as the alkylating agent. The compound has been prepared by ortho-alkylation of phenol using 2-methylpropene (isobutylene) as the alkylating agent and aluminum phenolate, prepared in situ using commercial grade aluminum, as the catalyst in bench and pilot plant scales and the synthetic parameters have been optimized. An alternative, cheap alkylating agent, namely Butane-Butene Raffinate (BBR) from Arak Petrochemical Complex, has also been successfully used in the synthesis. Moreover, the product has been characterized by 1H NMR spectroscopy, and its antioxidant efficiency has been evaluated. Also, the samples prepared have been blended in ATK (Aviation Turbine Kerosene) jet fuel together with another necessary antistatic additive (ASA), and the formulations have been tested by the central quality control laboratory of the National Iranian Oil Refining and Distribution Company (NIORDC). Finally, the results of quality control tests have indicated the efficiency of the prepared formulations with respect to the corresponding specifications and their comparability with authentic additive samples.Keywords: Topanol A, Jet Fuel Antioxidant, Phenol Ortho-Alkylation
-
Pages 10-26Fluid catalytic cracking (FCC) process is a vital refinery process which majorly produces gasoline. In this research, a hybrid algorithm which was constituted of Adaptive Neuro-Fuzzy Inference System (ANFIS) and firefly optimization algorithm was developed to model the process and optimize the operating conditions. To conduct the research, industrial data of Abadan refinery FCC process were carefully gathered along a definite period. Then a model based on ANFIS was developed to investigate the effect of operating variables including reactor temperature, feed flow rate, temperature of top of main column, and the temperature of bottom of the debutanizer tower on quality and quantity of gasoline, LPG flow rate, and process conversion. Moreover, statistical parameters comprising R2, RMSE, and MRE approved the accuracy of the model. Eventually, validated ANFIS model and firefly algorithm as an evolutionary optimization algorithm were applied to optimize the operating conditions. Also, three different optimization cases including maximization of Research Octane Number (RON) , gasoline flow rate, and conversion were considered. In addition, to obtain maximum target output variables, inlet reactor temperature, temperature of top of main column, temperature of the bottom of debutanizer column, and feed flow rate should be respectively set at 523, 138, 183 °C and 40731 bbl/day. Also, the sensitivity analysis between the input and output variables was carried out to derive some effective rules of thumb to facilitate operation of the process under unsteady state conditions. Finally, the obtained result introduces a methodology to compensate for the negative effect of undesirable variation of some of the operating variables by manipulating the others.Keywords: Fluid Catalytic Cracking, Adaptive Neuro-Fuzzy Inference System, Firefly Algorithm, Optimization, RON, Gasoline
-
Pages 27-45The lateral sealing ability of a normal fault is a major factor in creating hydrocarbon traps. Therefore, a methodology for assessing the sealing ability of faults in the siliciclastic sequences of subsidence basins has been established; moreover, by using this methodology, the uncertainty inherent in hydrocarbon exploration can be decreased.
Moreover, the petrophysical properties of fault rocks and reservoirs are emphasized by the methodology. In addition, the petrophysical properties of fault rocks and reservoirs are mainly determined based on clay contents and compaction pressure according to experiments on manmade rock samples which are representative of the researching area.
Furthermore, by using this methodology, the petrophysical properties of fault rocks and reservoirs, which are mainly determined based on clay content and compaction pressure according to experiments on manmade rock samples representative of the researching area are emphasized.
Thus, the lateral sealing ability of the fault can be assessed as follows: First, a best-fit equation describing the displacement pressures, clay contents, and compaction pressures of the rock samples is established by us. Then, the positive pressure on the fault plane from the decomposition of effective overburden pressure is calculated; afterwards, the clay content of the fault rock (Shale Gouge Ratio) is calculated by us.
Finally, the displacement pressures of the fault rock and the juxtaposed reservoir rock are predicted. Ultimately, based on this study which has been carried out, the results for the case study of the Tangjiahe fault in Well Gang 64, in the western part of the Qikou Sag, China coincide with the exploration results, which this coincidence confirms that this methodology is capable of evaluating the lateral sealing ability of faults in certain geologic settings.
Keywords: Normal Fault, Lateral Fault Sealing, Siliciclastic Sequences, Fault Rock, Displacement Pressure -
Pages 46-63One of the factors which affects the gas lift performance is specific gravity of a lift gas (or the Molecular weight), which can influence the gas solubility in oil and has a direct effect on the gas lift performance. There are some previous researches which have included the lift gas specific gravity in their modeling, but in none of them, a comprehensive research about the effect of lift gas specific gravity in gas allocation optimization, gas lift stability, economic factors, and some other aspects of gas lift is done. This research, concentrating on lift gas specific gravity, introduces an easy and inexpensive method for increasing the oil production in gas lifted wells. In addition, the effect of injection gas specific gravity in some phenomena such as the stability of the flow in a single well and in a gas allocation optimization has been studied, and an easy way to escape the unstable flow introduced. Moreover, the result shows that changing the gas composition causes three different behaviors based on the range of changes. In a group of wells, changing the specific gravity of gas causes a different injection pattern, but its effect on total production is not huge. Finally, similar to the case of single wells, changing the specific gravity of a group of wells has changed the production in three regions and has its specific sensitivity to the change of the injection gas specific gravity in each region.
Keywords: Gas Lift, Molecular Weight, Gas Allocation, Optimization -
Pages 64-87The significant increase in using reservoir simulation models poses significant challenges in the design and calibration of models. Moreover, conventional model calibration, history matching, is usually performed using a trial and error process of adjusting model parameters until a satisfactory match is obtained. In addition, history matching is an inverse problem, and hence it may have non-unique solutions. In typical reservoir simulation problems with a large number of unknown parameters, the problem could be ill-posed. In recent years, assisted history matching approach has been offered to solve this problem hopefully. In this paper, proposes an efficient assisted history matching workflow is recommended, and its application in a full field reservoir simulation model of a mature gas-cap reservoir is presented. In addition, Sobol sequence experimental design technique, Kriging proxy modeling, and three novel metaheuristic optimization algorithms are used to assist the history match of 28 years of historical production and pressure data. Finally, the results are compared with those obtained using a manual history matching procedure and with those obtained using the most widely used assisted history matching workflow. Also, in the proposed workflow, a significant improvement in terms of match quality and solution time is shown.Keywords: Assisted History Matching, Experimental Design, Proxy Modeling, Optimization Algorithms, Reservoir Simulation Workflow
-
Pages 88-101Conventionally, methane is reformed into syngas, and subsequently converted into C1-oxygenates (methanol and formaldehyde). A novel option is the catalyst-free single-step conversion of methane to C1-oxygenates. This study presents a comprehensive model of methane partial oxidation to formaldehyde as an intermediate chemical species in methane oxidation process using microreactor. The dependency of C1-oxygenates yield on operating parameters is crucial. Therefore a representative mathematical model is constructed and solved in order to investigate the effect of operating temperature, feed flow-rate, and composition on the formaldehyde yield. Fifty-four coupled of differential equations are solved by finite element method. Moreover, to simulate the process, GRI-Mech 3.0 is employed as the reaction kinetics. A good agreement was achieved when the model results were compared with experimental data from the literature in terms of formaldehyde concentration and methane conversion. Finally, results of the study are presented and discussed on the basis of a major reaction pathway proposed in this study for methane oxidation at low temperature, and the important design criteria are presented. With respect to the model results, 5.5% yield for formaldehyde per one pass of microreactor was achieved at the operating condition of T = 1000 K and O2/CH4 ratio = 17.Keywords: Methane, Formaldehyde, Microreactor, Single Step, Non-catalytic, Kinetic Study