فهرست مطالب
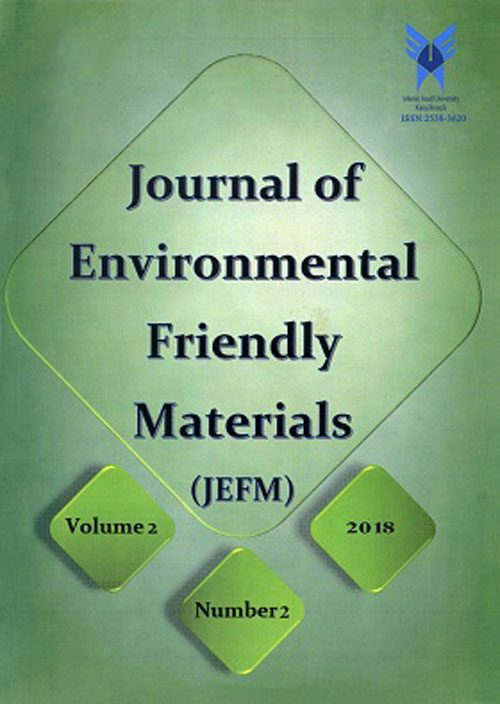
Journal of Environmental Friendly Materials
Volume:1 Issue: 2, Summer and Autumn 2017
- تاریخ انتشار: 1396/06/10
- تعداد عناوین: 8
-
Pages 1-6Titanium alloys are important bio materials which may also need to a bio compatible coating. To improve the Ti/glass-ceramic bonding is a challenging part of coating because the bonding properties play an important role in the long-term performance of medical implants. The purpose of this research is to improve the bonding strength of bioactive coating in the system of CaO-P2O5-Na2O-TiO2 using the formation of suitable oxidized layer and studying the effect of this interlayer on adhesion of coating. To achieve this goal, after surface modification, the surface of titanium samples was heat treated in 750 ˚c for 30, 60 and 90 min, to be oxidized. The results of Scanning Electron Microscopy (SEM) and Elemental concentration analysis by EDS and Atomic Force Microscopy (AFM) show that oxidized layer that was produced in 750˚c and 30 min. This oxidized interlayer has the best properties in comparison with two other samples and has the best adhesion to both substrate and coating.Keywords: Titanium Alloys, Bioactive Coating, Oxidation, heat treatment, Bonding Strength
-
Pages 15-22In this research, the friction stir welding was performed underwater in order to evaluate and improve the mechanical properties of aluminum 2024 alloy. Welding samples were compared with the samples in the air welding. The results showed that samples of the underwater welding in case the rotational speed is 1000 RPM and feed rate is in 80 mm/min, has the highest tensile strength, also they obtain the highest hardness at a rotational speed of 1000 RPM and forward speed of 100 mm/min. Also, an increase of travel speed reduces deformation of the material, heat input and soft area width during the welding process and increases hardness of TMAZ and HAZ. With increasing rotational speed, heat input and soft area width increased. This will, on the one hand, decrease the hardness of TMAZ and HAZ and, on the other hand, increase the stiffness of the disturbance area. Increasing hardness also ultimately improves the tensile strength of the welding joint.Keywords: Underwater Friction-Stir Welding, Al2024, Travel Speed, Rotational speed
-
Pages 23-32The purpose of the present study was to investigate the fatigue behavior of Al-6063 alloy using standard rotating-bending test. Corrosion-fatigue test on similar samples was also performed at stress levels corresponding to fatigue test. The samples obtained from fatigue tests were considered as control samples and the results obtained from fatigue test in air were compared to the results obtained from corrosion-fatigue test in liquid seawater. Scanning Electron Microscopy (SEM) and Optical Microscopy (OM) were used to investigate the micro-structural features and crack characteristics of the specimens. The results obtained from fatigue and corrosion-fatigue test revealed that the presence of corrosion environment decreases the fatigue life. Additionally, microstructure studies on the fracture surface due to corrosion-fatigue revealed that initiation of fatigue crack starts from the depth of corrosion steps and proliferate towards the sample center simultaneous with the penetration of liquid into the crack. Moreover, the appearance, size and propagation way of fatigue crack in corrosion-fatigue test was completely different from the cracks created in a fatigue test. The fracture surface due to corrosion-fatigue test was also different from the fatigue fracture surface. Further studies on failure levels revealed that the ratio of region area due to fatigue to the region area due to final failure was strongly decreased in the corrosion-fatigue test.Keywords: Corrosion Fatigue, Al 6063-T6 Alloys, Seawater, Crack Initiation, Striation lines
-
Pages 33-40The present study investigates the effects of type of shielding gas on the weld microstructure and mechanical properties of 409L ferritic stainless steel. For this purpose, Ar, Ar +20% He, Ar + 12% CO2, and Ar + 25% CO2 were used as shielding gases in gas metal arc welding (GMAW) of stainless steel. To evaluate the welds, non-destructive inspections of the specimens were followed by mechanical (hardness and tensile) tests while microstructural examinations of both the heat affected zone (HAZ) and the fusion zone were performed. Moreover, the phases produced were observed and identified by analyzing the specimens using SEM and EDS techniques. Results showed that specimens welded with Ar + 25% CO2 and Ar + 12% CO2 have the highest strength and hardness values in the fusion zone due to the formation of martensite around the ferrite grains. However, the enhancements observed in the mechanical properties of specimens welded with Ar and Ar +20% He were attributed to the reduced ferrite grain size and martensite contentKeywords: Ferritic Stainless Steels, Shielding Gas, Gas Metal Arc Welding, Microstructure, Mechanical Tests
-
Pages 41-44In this investigation, the microstructure and mechanical properties of the Al 5058 weld metals have been studied in respect of Nickel content in the range of 0.5 to 4.5 percent. Samples were produced by automatic TIG welding process in Butt weld condition with different wire feeder speed rate of pure nickel filler metal. The optical metallography and EDX analysis result shows that by increasing of the nickel content in the weld metal, the grain size decreased and the volume fraction of the inter-metallic compounds of Nickel rich phase was increased. The mechanical test results show that by increasing of the nickel content in the weld metal, the tensile and yield strength increased, whilst impact energy and elongation decreased.Keywords: nickel, Al 5000 Series, Weld Metal, Microstructure, mechanical properties
-
Pages 45-54In this paper, the thermodynamic simulation and the first and second laws analysis of an ammonia-water ejector-absorption refrigeration cycle is presented. A computer program has been applied in order to investigate the effects of parameters such as condenser, absorber, generator, and evaporator on the performance coefficient and exergy efficiency of this cycle. The results showed that in general when the temperature of different parts increases, performance coefficient and the exergy efficiency of the cycle decreases except for evaporator and generator that causes an increase in COP. The Entrainment ratio of the ejector, COP and exergy efficiency of the cycle decreases when the condenser temperature rises. Evaporator temperature increase leads to the increase of all studied parameters except exergy efficiency. Moreover, absorber and ejector have the highest exergy losses in the studied conditions. When generator temperature rises, total exergy loss and the entrainment ratio increase but leads to the reduction of the exergy efficiency.Keywords: Absorption Refrigeration, Ejector, Exergy Efficiency, COP
-
Pages 55-64Two blade samples from the first and second stages of a gas turbine were investigated to understand the reason of fracture. All samples suffered excessive heat superficially. Using a TBC layer on top of Diffusion coating will be a reasonable solution for protecting the blades. Although in case of the first stage blades cracking was postponed, the thermomechanical fatigue cracks still originated from the blade surface. It was observed that the damage of the thermal barrier coating layer would lead to the overheating of the blades, promoting the rate of creep and rafting of g¢ precipitates. This phenomenon was more severe in the second stage samples with more damaged protective layers. It was found that the chemical composition of the fuel gas may increase the potential and rate of corrosion and damage to the blades. Concurrent with physical investigation, numerical simulation was performed to study the effect of particle impact into the blade. By changing the particle radii and its position, damage area was inspected. Numerical simulation shows that particle radii and its position have an important effect on the chipping removal from the blade.Keywords: Superalloys, Precipitates, Thermomechanical Fatigue, Mercaptans, Numerical simulation