فهرست مطالب
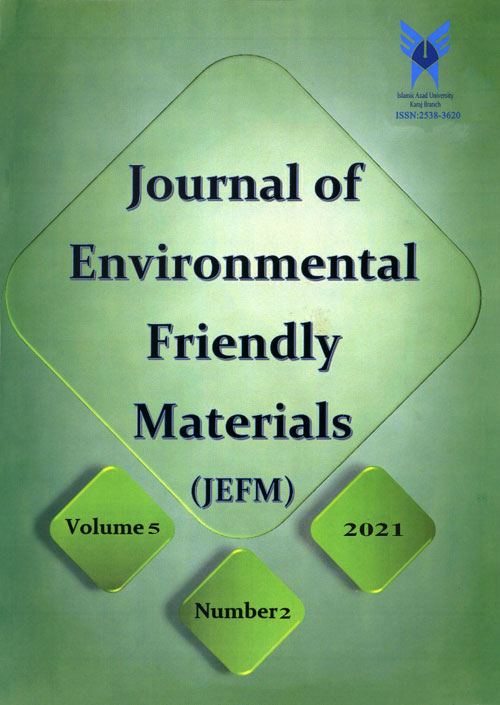
Journal of Environmental Friendly Materials
Volume:5 Issue: 2, Summer-Autumn 2021
- تاریخ انتشار: 1400/09/10
- تعداد عناوین: 10
-
Pages 1-9
In this study, the shear spinning process and the rolling process on C11000 copper metal with a thickness reduction of 50% at room temperature were performed and investigated. In the shear spinning specimen, the grains are stretched in the axis direction and elongated in the circumferential direction. In the rolled specimen, the grains are extended in the direction of rolling, and the elongation of the grains in the T-N plane is less than in the shear spinning specimen. EBSD analysis showed that the ratio of high angle boundaries to low angle boundaries in the shear spinning specimen is higher than the rolled specimen. The mechanical properties of the rolled and shear spinning specimens were investigated in three directions of zero, 45, and 90 degrees relative to the forming direction, which showed that the strength in all three directions was higher in the rolled specimen than in the shear spinning specimen. The elongation in the shear spinning specimen is more than in the rolled specimen. The highest amount of tensile strength in the rolled specimen is about 370 MPa, and the highest elongation is about 12% in the shear spinning specimen. Also, anisotropy in shear spinning specimens was less than rolled specimens.
Keywords: Spinning, Shear Spinning, Rolling, Mechanical Properties, Copper -
Pages 11-15
Metal-based nanocomposite coating prepared by plating method can exhibit unique mechanical, chemical, and physical features which have led to their extensive application in various high-tech industries. Nickel-based nanocomposite coatings can pose far lower pollution toward the environment and related staff as compared with chromium-based ones. In this research, a novel compound was developed to coat nickel-alumina nanocomposite by adding formaldehyde to the plating bath. The concentration of alumina nanoparticles (NPs) in the plating bath was 10 g/L. The nickel-alumina nanocomposite coatings were prepared by a pulsed electrical current under ultrasound turbulence in the plating bath. Two Ni bathes in combination with Watt’s compound were used with and without formaldehyde addition. Before plating, the zeta potential of alumina NPs was measured in the two different baths. After plating, the cross-section of the coatings and the alumina content participated in the coating, as well as the coating morphology, were analyzed by scanning electron microscopy (SEM) equipped with energy-dispersive X-ray spectroscopy (EDX). Based on the results, incorporation of formaldehyde into the Watt’s solution increased the zeta potential of the nanoparticles from -4.1 to +30.5 mV; consequently, the nanoparticle content of the coatings enhanced from 4.6 to 8.5 vol.%.
Keywords: Composite Electrodeposition, Nickel Alumina Nanocomposite, Formaldehyde, Zeta Potential -
Pages 17-20
Nickel oxide (NiO) thin film is metal oxide that has attracted much attention in recent years due to its environment friendliness. In addition, by doping impurities such as copper (Cu) in NiO films the properties of prepared films can be changed. In this study, Cu:NiO thin films were deposited on silicon substrates by RF reactive magnetron sputtering. Then the deposited films were annealed at different temperatures of 200-600 °C. X-ray diffraction (XRD) results showed that all the prepared films were amorphous and the structural properties of films didn’t vary by annealing temperature. Also, atomic force microscopy (AFM) images demonstrated that the surface morphology of the films was affected by annealing temperature. The root mean square (Rms) roughness and average roughness (Ra) values were obtained from AFM observations. FTIR analysis shows the peaks in the wavenumber of 528 cm-1 and 742 cm-1 which are related to Ni-O stretching mode and Cu-O bond bending vibrations.
Keywords: Sputtering, Cu, Nickel oxide, Thin films, FTIR -
Pages 21-25
In this research, the influence of boron content on microstructure and dry sliding wear resistance of as-cast FeAl-based alloys was evaluated. The alloying process was carried out using vacuum induction melting and four specimens having different boron content of 0, 0.1, 0.5 and 1 at% were produced. As-cast specimens then were teste using standard pin-on-disk wear tester machine in 20 and 40 N applied load and a distance of 1000 m according to ASTM G99 standard. The surface of worn specimens then were examined using scanning electron microscope to determine the dominated wear mechanism. The investigations revealed that at lower applied load of 20 N, the governing wear mechanism is oxidative wear and for higher applied load of 40 N, delamination is the governing mechanism. Increasing the boron content increases the hardness as well as the wear resistance of the alloy which is related to the formation of Fe2B compounds in the material and increasing the hardness.
Keywords: Iron Aluminide- FeAl, Boron Content, Casting, Microstructure, Wear Properties -
Pages 27-33
The focused of this investigation is on the modification of Fe-rich intermetallics morphology and wear and friction properties of eutectic Al-Si alloys. Eutectic Al-Si specimens were fabricated by tilt casting technique after addition of different amounts of iron and manganese to the melt alloy. Dry sliding tribological behavior of the samples were investigated using a reciprocating wear tester at the room temperature in atmospheric environment. It is found that the addition of iron up to 1.5 wt.pct to the alloy decreased the wear resistance of alloy owing to the formation of brittle plate-like β-Al5FeSi intermetallic compounds. As Manganese is added to the β-containing alloy up to the half of iron content (corresponding to a Mn/Fe ratio of 0.5), the platelet phases are completely replaced by the star-like α-Al15(Fe,Mn)3Si2 intermetallics resulting in improved wear resistance of the alloy. Introducing 0.8 wt.pct Mn to the alloy containing 1.6 wt.pct Fe did not convert the plate-like beta intermetallics to the modified alpha compounds completely and had no impressive impact on the wear rate of the alloy.
Keywords: Eutectic Aluminum-Silicon Alloys, Intermetallic Morphologies, Mn Modifier, Friction Coefficient -
Pages 35-43
In this investigation, different amount of carbon and chromium content of Fe-Cr-C hardfacing alloys with the constant ratio of Cr/C=6 were used. These alloys were fabricated by GTAW on AISI 1010 mild steel substrates to achieve hypo/eutectic/hyper compositions. OES, XRF, OM, SEM, XRD techniques and HV method were used for determining chemical composition, hardness and studying the microstructure of hardface alloys. The metallographic examination results indicated that all hardface samples had three metallurgical zones with different thickness, microhardness, chemical composition and solidification modes. The microstructures of all hardface samples in thicker Zone consists of austenite and chromium-iron carbides (Cr,Fe)7C3. Moreover with increasing of carbon and chromium content of thicker zone in hardface samples, the volume fraction of (Cr,Fe)7C3 increased and resulted in the decreasing of austenite volume fraction and increasing hardness of the top surface. A multiple regression model was used to determine the relation between microstructure, chemical composition and hardness
Keywords: Alloys, Cr, C, 6, Surface modification, Microstructure, SEM -
Pages 45-49
Knowledge of the measurable parameters in an electric arc furnace can effectively increase efficiency while declining energy consumption, hence leading to positive environmental consequences. This issue has been frequently addressed in various studies, but the extent of these effects and their cause-effect relationships have been rarely explored. In decision-making procedures that depend on various factors, the extent of the effect could be also effective in addition to the priority. The optimization and the effect intensity, as well as affectability of some effective parameters of an electric arc furnace, can dramatically influence the quality of the produced steel, energy consumption of the process, and consumption of electrode and refractory substances. The aim of this study is thus to examine the mutual effects of various carbon injection contents, electrical power consumption levels, slag, and other effective parameters of the electric arc furnace during different charges including material and energy consumption, volume and quality of the slag, and pollutant emission using the DEMATEL mathematical model. To this end, calculations of some of the recorded parameters of a 110-ton electrical arc furnace in the Khorasan steel complex were studied and compared.
Keywords: Electric Arc Furnace, Modeling, Extractive Metallurgy, Pairwise Comparison Method, DEMATEL Method -
Pages 51-54
Mesoporous silica SBA-15 was synthesized by liquid crystal method and then was functionalized by amino acid L-Cysteine in presence of N,N'-Dicyclohexylcarbodiimide (DCC) as coupling agent. The functionalized nanoporous material has been utilized for adsorptive removal of heavy metals such as Copper, Cadmium, Silver, Cobalt, Nickel, and Lead cations from aqueous solution. The synthesized adsorbent has been also characterized by means of BET/BJH surface area, TEM and FT-IR methods. Moreover, adsorption capacities of the functionalized material were calculated by heavy metal ions analysis with atomic absorption spectroscopy (AA). The pH of the solution has been optimized for each element. The results explored the L-Cysteine functionalized mesoporous silica (SBA-15) is a suitable adsorbent for almost completely removal of Cu and Ag. It is also an efficient adsorbent for some other heavy metals. According to this study, adsorption capacity of the nanostructured material for heavy metals removal is (Cu+2, 99.6%; Ag+, 99.4%; Cd+2, 84.4%; Pb+2, 89.2%; Ni+2, 60.1%; Co+2, 86.9%).
Keywords: Mesoporous silica, Heavy metals removal, amino acid, L- Cysteine, DCC -
Pages 55-64
Blades of a gas turbine are the main and most important parts of turbine machines that work in very difficult and complex conditions. Existence of discontinuities and defects in the structure of these parts cause sudden and irreparable damage. It can completely take a turbine out of operation and impose huge costs on a power plant. Therefore, pre-installation controls and inspections for these parts are of great importance. One of the safest and most reliable methods of control and inspection is the use of non-destructive tests. One of the methods that has been considered in recent years is the use of infrared waves, which in this method; Surface defects and sometimes even internal defects can be detected by using infrared cameras that operate within a certain range of the electromagnetic wave spectrum (0.8-14 nm). In this paper, we try to review the conventional methods of non-destructive testing that are used in troubleshooting blades of gas turbines, and the method of using infrared waves as an alternative method to conventional methods to be discussed.
Keywords: Non-Destructive Tests (NDT), Thermography, Gas turbine blades -
Pages 65-69
Underwater friction stir welding (FSW) has been demonstrated to be an effective method to improve the mechanical properties of joints. To illuminate the characteristics of underwater FSW, the microstructural evolution and its effect on mechanical performance of an underwater joint were investigated in the present paper. This work compared the parameters of friction stir welding (FSW) and under water friction welding (UWFSW) on the weld joint .In this investigating Friction stir welding (FSW) used in under water environment, for this Operations research pin covered and shielded from contact water by hollow shaft spin (HSS), the HSS controlled the heat conduction of pin and disconnect with water, applying for the first time a novel under water FSW technique developed at marine structures.The novel technique acceptance given by the experimental setup on Al X4000 series, for studied the mechanical and metallographic exams. The metallographic exams indicate that weld nugget grain size has been decreased. The mechanical testing illustrated hardness and tensile strength have been increased, on the other hand the percentage of elongation and impact energy have been decreased.
Keywords: Under Water, Friction Stir Welding, Mechanical Properties, Weld Nugget, grain size