فهرست مطالب
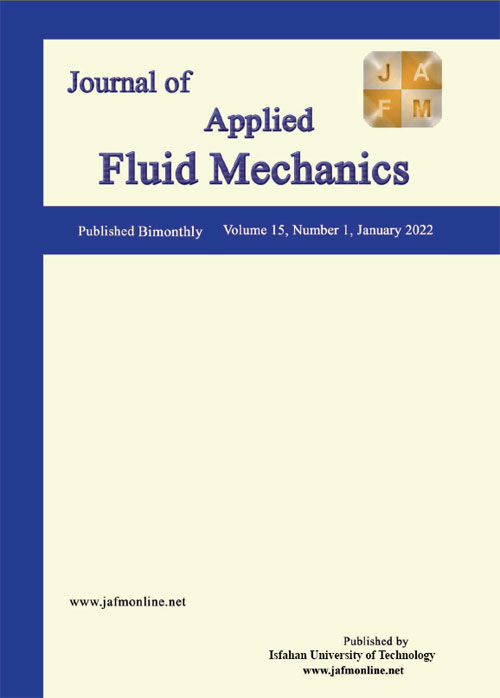
Journal Of Applied Fluid Mechanics
Volume:15 Issue: 1, Jan-Feb 2022
- تاریخ انتشار: 1400/10/08
- تعداد عناوین: 25
-
-
Pages 1-14Natural convective heat transfer of Fe3O4/graphite slurry in a square cavity is numerically examined. The slurry is assumed to be a non-Newtonian ferrofluid under a variable external magnetic field. The left and right walls of the cavity are assumed to be at a relatively low temperature (Tc), while the horizontal walls are thermally insulated. A heat source with a variable temperature distribution is located at the bottom of the enclosure. The non-Newtonian behavior of the graphite slurry (a mixture of ethylene glycol and graphite powder) has been modelled using experimental results. The control volume method and the SIMPLE algorithm were used to discretize and solve the governing equations considering the Ferro-hydrodynamics (FHD), the Magnetohydrodynamics (MHD) and the non-Newtonian fluid behavior. The heat transfer and fluid flow properties are determined for different locations of the magnetic field source, and different values of the magnetic number (Kelvin force), and the Hartmann number (Lorentz force). The results show that when the magnetic field source is located below the enclosure and near the heat source, the vortices are strengthened resulting in an increased heat transfer. The heat transfer rate is affected by FHD and MHD. When the magnetic field source is located at the corner points, the heat transfer rate is not significantly affected by the magnetic and Hartmann numbers. However, once the magnetic field source is located near the central point of the lower wall of the enclosure, the heat transfer rate is influenced by the increase of the magnetic number.Keywords: Ferrofluid, non-Newtonian, Magnetic field, Ferrohydrodynamics (FHD), Magnetohydrodynamics (MHD)
-
Pages 15-23This study explores the influence of tandem stenosis on hemodynamic constraints in idealized coronary artery models with different interspace distance between the stenosis and its severity. The blood was assumed as non-Newtonian, incompressible, and pulsatile fluid. The hemodynamic parameters of blood, such as the oscillatory shear index (OSI), wall shear stress (WSS) and time average wall shear stress (TAWSS) are obtained and compared for various degrees of stenosis and interspacing distance in various blood models. The computed results showed that as the interspacing distance between the stenosis decreases, the low wall shear stress area increases for the model P70_D70, leading to further progression of stenosis in the distal region. No significant variation was observed for the model P70_D90, whereas the low WSS region increases as the interspace distance of proximal and distal stenosis increases for the model P90_D70. The highest TAWSS sites were created across the 90% AS (area stenosis) for all the cases studied. As the higher value of TAWSS is clinically significant since it could damage the endothelial layer. It is well known that the maximum value of OSI is strongly associated with the critical areas of stenosis rupture. The maximum value of OSI was found at the proximal and distal stenosis for all the models simulated.Keywords: wall shear stress, Computational fluid dynamics, non-Newtonian, Endothelial layer
-
Pages 25-36To research the effect of the volute geometry on the radial force characteristics of the centrifugal pump during the starting process, choosing a centrifugal pump with a head of 87m as the research object. The pumping chamber is redesigned into a single-volute and a double-volute with similar external characteristics, and a circulation pipeline system is established. RNG k-ε turbulence model is employed to calculate the unsteady starting process of two kinds of centrifugal pumps. The variation trends of radial force received by the impeller and volute during the start-up process are obtained. The radial force characteristics and internal flow field evolution of two centrifugal pumps are compared and analyzed. The results show that the radial force vector distribution of the impeller changes in spiral periodicity during the startup process, and the spiral geometry is influenced by the number of impeller blades. The direction of the spiral is opposite to the rotational speed. The double-volute geometry can effectively reduce the radial force and pulsation amplitude of the impeller during the start-up process of the centrifugal pump, reducing the radial force by about 80% at rated speed. But the radial force vector distribution of the double-volute is more complicated and disordered than the single-volute.Keywords: Centrifugal pump, Volute geometry, Numerical simulation, Startup process, Radial force
-
Pages 37-50The Actuator Disk Method (ADM), in its analytical formulation or combined with Navier-Stokes equations, is widely used for design and/or for aerodynamic analysis of Horizontal Axis Wind Turbines (HAWT). This method has demonstrated its capabilities for performance predictions of HAWT rotors for limited range of wind speeds with lower angles of attack values, i.e. attached flow conditions. However, for typical wind speeds that rotor encounters, under higher angles of attack i.e. stall conditions, such a method cannot describe accurately the flow characteristics around rotor-blades due to severe flow separations coupled with the effects of blades rotation as well as the radial flow over the blades. In this paper, original correction approaches have been proposed for the existing stall delay models to take into account both the blade rotation and the radial flow effects over the rotor blades. For this purpose, the ADM combined with 3D- NavierStokes equations formulation using Large Eddy Simulations (LES) model has been considered to describe the incompressible turbulent flow field around HAWT rotor blades. The resulting mathematical model has been solved using a 3D in-house subroutine developed with OpenFOAM code. The proposed numerical method has been validated against the well recognized reference measurements obtained using the New MEXICO and the NREL Phase VI experimental wind turbines. In comparison with existing stall delay models, the proposed correctionapproaches, especially the radial flow approach, have shown noticeable enhancements on performance predictions of HAWT rotors compared to the experimental measurements. It has been found very low discrepancies to the experimental torque and thrust values, up to 1% and 10% have been recorded respectively.Keywords: Actuator disk method, HAWT, Aerodynamic performances, Stall delay model, LES model, Numerical simulation
-
Pages 51-62The outrigger symmetry of a trimaran is believed to significantly affect its hydrodynamic functioning. The present study was conducted to investigate the added resistance responses and experimental vertical motion of a wave-piercing trimaran in regular head waves. A series of experiments have been carried out in the National Iranian Marine Laboratory (NIMALA) towing tank to determine the effect of side hulls symmetry on the heave and pitch motions and added resistance. The models were tested over a range of wave frequencies and Froude numbers using both symmetric and asymmetric outriggers. According to the results, the symmetric side hull form based on heave motion, the outboard form in terms of pitch motion and added resistance have better performances among these three kinds of side hull forms. Furthermore, there are local maximum and minimum points on the ship motion response curves due to heave and pitch coupling in their respective frequencies.Keywords: Wave-piercing trimaran, Side hull symmetry, Seakeeping, Experimental studies, Added resistance, RAO
-
Pages 63-72The cooling effectiveness of optical window influences the imaging quality of hypersonic vehicles. This study focuses on the supersonic film cooling efficiency on the optical window of a blunt cone in hypersonic flow. The experiments were conducted in a gun tunnel equipped with a Mach 8 nozzle providing a total pressure and temperature of 9 MPa and 900 K respectively. Three tangential 2D nozzles with different combinations of slot heights and Mach numbers were designed to detect the film cooling length under different injection pressures. The heat flux on window surface was measured by Thin Film Gauges and the flow field was monitored by schlieren technique. When the jet pressure matched the mainstream, the window was completely cooled, and the minimum mass flow rate was achieved when the slot height was 5mm and the jet Mach number was 2.5. If the pressure ratio of jet continues to increase, the heat flux density could be furtherly reduced, but the cooling efficiency of unit coolant mass flow decreased significantly. The data correlation results showed that the cooling efficiency presented a nonlinear relationship of second order polynomial with (x/Sh)λ-0.8 , and the effective cooling length of film was positively correlated with the cooling mass flow ratio (λ) and slot height of the nozzle. Besides, the increase of jet pressure resulted in thickening the mixing layer, which enhanced the heat insulation effect and reduced the heat flux as a result.Keywords: Optical window, Supersonic film, Injection nozzles, Cooling efficiency
-
Pages 73-84An experimental investigation has been designed and performed to determine the fluid flow characteristics in a rotor-stator cavity with large gap ratio and inlet at low radius. In this investigation, the particle image velocimetry (PIV) technique is employed for the velocity measurements of airflow in the rotor-stator cavity. Local swirl ratios are calculated from these velocity distributions. A range of parameter combinations of interest in fluid flow characteristics is covered, including combinations of variations in axial location, rotational Reynolds number (denoted as Reφ), and inlet nondimensional mass flow rate (denoted as CW). The results indicate that the flow in the rotor-stator cavity is still dominated by circumferential motion. The velocity is basically unchanged along the circumference. However, the velocity increases with the increase of radial position. In different axial positions, the velocity distribution is different. The closer to the rotor, the more uneven the flow in the rotor-stator cavity is. The disturbance of the rotor rotating motion to the fluid mainly occurs in the high radius region, which should be paid more attention to in the process of reforming the flow field characteristics. To the circumferential velocity of low radius fluid, the Reφ is in direct proportion, while the CW is in inverse. The swirl ratio in the core region is very close to that in the high radius near the wall region of the rotor, which can be inferred to be caused by the backflow in the rotor-stator cavity.Keywords: Rotor-stator cavity, Rotational Reynolds number, Nondimensional mass flow rate, Swirl ratio, Particle image velocimetry
-
Pages 85-98A comparative study of the buoyancy-opposed wall jet has been carried out using RANS methods (including RNG model, Realizable k-ε model, and two low Reynolds number k-ε models) and LES methods (including the subgrid scale model developed by Smagorinsky et al.(1963), Germano et al. (1991) and Kim et al. (1997)). The capability of each turbulence model to predict the flow field and temperature field in mixing stage was investigated. The results show that the k-ε series model can accurately predict the velocity distribution of flow field under isothermal case. However, in the case of buoyancy, due to the assumption of turbulent normal stress isotropy, the trend of temperature change in the mixing region and transition position existed an obvious deviation with experimental data. The LES methods, solved directly the large scale vortices, take into account the influence of turbulence stress anisotropy in the mixing region on the temperature change and capture the temperature change trend over the whole domain accurately. Due to the application of the subgrid kinetic energy transport equation, KET model has certain advantages in numerical simulation of similar engineering flow phenomenon.Keywords: Buoyancy effect, Wall jet, LES, Sub-grid kinetic energy transport equation
-
Pages 99-107Wind energy is one of the abundantly available renewable energy resources. Savonius vertical axis wind turbine is better suited for small scale power generation applications with many advantages. The turbine operates independent of wind direction with good starting torque and less noise. But, the power coefficient of the Savonius turbine is less than all other wind turbines. The shape of the turbine blades plays an important role in the performance of the turbine. In this present two-dimensional numerical study, an attempt has been made to improve the turbine performance by considering three types of blade shapes. The complete design details of the proposed new blade shapes are presented. The simulations are carried out using ANSYS Fluent 15.0 with SST K-ω turbulence model. The power coefficient of the modified blade is found to have increased by 20% compared to conventional blade shape. The effect of tip-speed-ratio on power coefficient has also been studied and reported.Keywords: Computational Study, Savonius turbine, Wind turbine, Power coefficient, Blade shape, Performance improvement
-
Pages 109-116In order to solve the problem of insufficient thrust measurement accuracy of aeroengine indoor testbed, the thrust calibration experiment technology is studied. Form two aspects of engine static calibration and dynamic calibration, the mechanism of thrust calibration is comprehensively analyzed form the perspective of testbed and engine, and a complete set of operable test specifications is formed. The technical difficulties of engine consistency, inlet temperature deviation and non-standard weather are solved, and the accuracy of thrust transmission process is ensured. The test scheme of indoor test bed calibration is given, and the corresponding ideas and requirements are given according to the test conditions, test bench, calibration engine, test process and result analysis, to ensure the accuracy of calibration results.Keywords: Aeroengine, Indoor testbed, Thrust calibration, Momentum correction, Thrust transfer
-
Pages 117-127Metal powder fuel has high energy and volume calorific values, and it is an excellent power fuel for hypersonic aircraft in the future. However, metal powder has poor flow characteristics and is difficult to be effectively mixed with air when supersonic air is injected. The mixing degree of fuel and air is an important factor to the efficiency of the engine. One way to solve this problem is to introduce a jet (the primary jet) upstream of the powder fuel inlet to improve the mixing degree of fuel and increase the residence time. In this study, a doublehole jet two-dimensional scramjet combustor structure was established, the effects of different initial jet conditions on the performance of scramjets was studied and analyzed. The results show that the introduction of the primary jet can effectively improve the mixing degree of the powdered fuel and air in the combustion chamber, prolong the residence time of the particles in the combustion chamber and improves the combustion efficiency of the metal powder. However, both the combustion efficiency of the metal powder fuel and engine thrust increase and then decrease when the mass flow rate of the primary jet increases.Keywords: Scramjet, Numerical simulation, Powder fuel, Jet, Combustion efficiency
-
Pages 129-137This work is devoted to study the Taylor-Couette flow at the early structuring stages. It is aimed to gain insight on the Taylor and Ekman vortices genesis mechanism since the first hints of presence detected at Ta=10-4. Simulations are carried out using Ansys Fluent software package. The basic system geometry is characterized bya height H= 150mm, ratio of inner to outer cylinder radii η= 0.9, radial gap δ= 0.11 and an aspect ratio corresponding to system height reported togap length, Г= H/δ = 15. Ekman and Taylor cells are tackled since the Taylor number Ta=10-4 to the first (TVF) and second (WVF) instabilities settlement at Tac1= 43.8 and Tac2= 54, respectively. It is sought to shed light on the underlying mechanism responsible for flow genesis and to identify all the intermediate successive steps from ex-nihilo when the system is at rest up to complete vortices formation. The obtained results show that presence of Ekman cells is already perceptible since a Taylor number as low as Ta= 10-4. In fact, localized overpressure zones are detected on system inner endcaps surfaces regularly distributed according to a π/2 phase lag. These overpressure zones azimuthally propagate to meet and cover the entire gap circumference when Ta~10-2 to10-1.Keywords: CFD, Taylor-Couette flow, Ekman cells, Fluent software, TVF, WVF
-
Pages 139-151The structured surface-enhanced pool boiling process and associated heat transfer enhancement characteristics are numerically investigated by using the pseudopotential multiphase flow lattice Boltzmann (LB) model coupled finite difference method (FDM). In the current study, the effects of different microstructure geometries(square structures, triangular serrated structures, triangular-raised structures) and varying spacing in triangular-raised structures (d = 0, 22, 44, 66, 88, 110 l.u. (lattice units)) on boiling heat transfer (BHT) characteristics and bubble dynamics behavior are studied in detail. The results showed that microstructure can accelerate bubble nucleation. Among the three microstructures, the heat transfer performance of triangular-raised structures was significantly better than that of square and triangular serrated structures in the nucleate boiling (Ja number is 0.124-0.145). The oscillation and deformation of bubbles led to the lateral migration of bubbles, the continuous nucleation of small bubbles. The phenomenon of re-wetting of heating surface occurred in the process of bubble migration, necking, deformation and detachment was found, which enhances heat transfer in nucleate boiling. At the same time, the growth, oscillation and detachment of bubbles also perturb the liquid and enhance the natural convection around the bubbles.Therefore the main BHT mechanism of nucleate boiling on the three kinds of structured surface is the combined action of transient heat conduction and micro-convection. The variation of the spacing between microstructures showed an important effect on the BHT performance of the heating surface and the generation of activated nucleation sites in the nucleate boiling. Triangular-raised structures can enhance transient heat conduction and micro-convection, with the strongest enhancement effect at d = 66 l.u when the Ja number is 0.124.Keywords: Boiling, Structured surface, Bubble dynamics, Lattice Boltzmann method
-
Pages 153-167Blade lean has been extensively used in axial compressor stators to control flow separations, but its influence mechanism on transonic compressor rotors remains to be revealed. The aim of this study is to numerically explore the influence of blade lean on the performance and shock wave/tip leakage flow interaction in a transonic compressor rotor. The effects of leaned pattern (positively lean and negatively lean), leaned angle and leaned height were studied. Results showed that, compared with baseline configuration, the efficiency and total pressure ratio of the entire constant rotating speed line of positively leaned rotor were both decreased. The absolute value of peak efficiency was reduced by as much as 4.34% at 20° lean angle, whereas the maximum reduction of peak total pressure ratio was 0.1 at 20° lean angle. The tip leakage flow streamlines of baseline transonic rotor can be divided into two parts, i.e., the primary vortex and secondary vortex which arises after the shock. Due to shock/tip leakage vortex interaction, the primary vortex enlarged and low-momentum region showed up after the shock; under near stall (NS) condition, tip leakage vortex breakdown occurred after interacting with shock. As positively leaned angle increased, the shock and the shock/tip leakage vortex interaction point moved upstream. In addition, the phenomenon of tip leakage vortex breakdown was enhanced. For negatively leaned rotors, as negatively leaned angle increased, the peak efficiency and total pressure ratio showed a tendency of first increasing and then decreasing. At 5° leaned angle, the peak efficiency was increased by 0.8% at most, and the maximum increment of total pressure ratio was 0.05 at 5° leaned angle. Besides, the loading of blade tip reduced and the loading moved toward trailing edge, resulting in the downstream movements of primary vortex, shock front and shock/tip leakage vortex interaction location. The results may help to improve the near tip flow field of transonic compressor rotor with leaned blade technology.Keywords: Blade lean, Tip leakage vortex, Shock, Tip leakage flow interaction, Transonic compressor
-
Pages 169-178The possibility of suppressing laminar vortex shedding after a rectangular cylinder with a pair of rotating controllers has been investigated for Re=150. Drag and lift coefficients of the rectangular cylinder have been measured at different positions of the controller system. Numerical results show that the controller system suppresses the vortex shedding completely when installing at some suitable positions. It was found that the controller system affects the vorticity intensity in the separation bubbles at these suitable positions. The controller system may completely eliminate the separation bubble or may make them remain in attached to the cylinder. Besides, the effectiveness sensitivity of the controller system to its rotation rate and Reynolds number was analyzed when installing at the edge of the cylinder boundary layer where its position is denoted by (r/a=2,q=40o). These analyses show that the controller system can still suppress the laminar vortex shedding completely when the rotation rate of the controller system and Reynolds number of the incoming flow change by less than 50%.Keywords: Rectangular cylinder, Rotating controller, Stabilized laminar flow, Laminar vortex shedding, Unstable laminar flow
-
Pages 179-191The effects of a Trapped Vortex Cavity (TVC) on the aerodynamic performance of a NACA 0024 airfoil at a constant angle of attack (AoA) of 14◦ were investigated in this study. It was observed that mass suction (MFR) was required to stabilise the vortex within the cavity segment. Lift to drag ratio (L/D) and MFR were chosen as performance objectives, along with a fully attached flow constraint (flow separation at X/c ≥ 95% ). Parametric analysis was carried on the baseline airfoil with and without suction and compared to the airfoil with TVC with and without suction. It was observed that L/D increases as MFR increases for a baseline airfoil, and flow separation is delayed at high suction values (MFR = 0.2 kg/s). The TVC modifies the pressure distribution on the baseline airfoil when MFR is applied to the cavity section and there is a significant increase in lift; thus, L/D increases and flow separation is delayed. A lower value of MFR = 0.08 kg/s is sufficient to stabilise the vortex and improve the efficiency of the TVC airfoil. The findings of these parametric studies were used to do a multi-objective optimisation using a genetic algorithm to attain the desired cavity shape while achieving the largest L/D and the lowest MFR (that is proportional to the power required for control) with a fully attached flow constraint. It was found that mass suction and cavity shape both had an equal influence on flow control. The Pareto optimal front yielded a series of optimum designs. One of them was subjected to an off-design analysis in order to validate its performance at other incidences. It was observed that it performs better than the baseline airfoil, with an improved L/D and an increase in stall angle from 10◦ to 14◦.Keywords: Airfoil, Vortex, Cavity, Flow separation, Multi-objective optimisation, Genetic Algorithm, Mass suction, Turbulence
-
Pages 193-207The flow fields around vehicle drag reduction devices are three-dimensional, complicated, and unsteady. Meanwhile, the small scale of the drag reduction device brings more challenges to the simulation. An Improved Delayed Detached Eddy Simulation (IDDES) was applied to study the effect of two types of drag reduction device. First, the flow field of an Ahmed body at a 25° slant was simulated in detail using IDDES and verified by experiment data. Afterwards, the flow field structures of adding-on vortex generators (VGs) and riblets on the rear and slant surface of the Ahmed body were studied. The simulation results of the velocity, pressure and vortex structure on the controlled case are presented by comparing with the baseline model to illustrate the drag reduction mechanism. The two drag-reduction devices had different flow mechanisms and significantly affected the development of the separation vortex near the rear and slanted surface. A maximum drag reduction of 6.21% could be achieved using VGs on the rear surface. Finally, four combinations of those two devices were investigated. The results demonstrated that suitable combinations can further decrease the aerodynamic drag, and an 8.62% drag reduction is achieved.Keywords: Passive flow control, Vortex generators, Riblets, Combined flow control, Detached eddy simulation
-
Pages 209-219In the wind tunnel test of trains, the scale size changes the Reynolds numbers of trains, which may affect the aerodynamic characteristics of the train. Based on computational fluid dynamics (CFD), numerical models of train aerodynamics with five different scale sizes are established. The five different scale sizes are λ=1/1, 1/2, 1/8, 1/16 and 1/25, respectively, and the aerodynamic characteristics of trains running in the open-air operating condition and crosswind operating condition with different scale sizes are numerically simulated. The results show that the pressure drag coefficients and pressure lift coefficients of the train tend to decrease with the decrease of the scale size. In the open-air operating condition, compared with the full-size train, the pressure drag coefficient of the 1/25th scaled train is less by 14.4%, and the pressure lift coefficients of the head car, middle car and tail car change 16.1%, 46.6% and 12.3%, respectively. The scale size affects the velocity gradient near the train surface and the position of flow separation changes. The decrease of the scale size leads to the decrease of Reynolds numbers and the increase of viscous drag coefficient. When the scale size is 1/25, the viscous drag coefficient of the train is 0.186, which is 48.6% larger than the one of the full-size train. Compared with the open-air operating condition, the trend of the pressure drag coefficients and viscous drag coefficients is consistent except for the head car in crosswind operating condition when the scale size decreases. In the range of scale size λ between 1/1 and 1/25, the aerodynamic drag coefficient of the head car, middle car and tail car increase with the decrease of scale size, and the difference in the aerodynamic drag coefficient of the train is 12.9%. In addition, the train’s aerodynamic lift coefficient shows an increasing trend with the decrease of scale size.Keywords: CFD, Scale size, High-speed trains, Aerodynamic force coefficient
-
Pages 221-230In the process of petrochemical production, the catalyst particles in the hydraulic conveying pipeline often cause wear failure accidents due to collisions with wall. Compared with spherical particles, non-spherical particles’ trajectory would be different due to its geometric shape, and thereby affecting the flow wear characteristics. In this paper, the shape of catalyst particle model with real aspect ratio was constructed by using multi-cluster method, and a CFD-DEM coupling method was adopted by considering the interaction between particle-particle and particle-wall. The study focuses on the effect of particle shape, radius of curvature and angle of bend in terms of the wear characteristics of liquid-solid two-phase flow. The results indicate that with the increase of the particle aspect ratio, the wear rate and the impact density of particles decrease while the impact velocity increases, the wear area of the elbow mainly distributes in the middle part of the outer wall, and its maximum position appears between 78° and 90° in polar coordinates; With the increase of pipe’s curvature radius, the main wear area changes due to the direct collision and the sliding friction of the particles along the pipe wall, and its maximum wear rate shows a downward trend due to the reinforce of buffering effect; With the decrease of bending angle, The main wear area decrease because of the changes in particle flow patterns and it is mainly located in the center of the outer wall.Keywords: Catalyst particles, CFD-DEM, Liquid-solid flow, Non-spherical particles, Numerical simulation
-
Pages 231-243This study investigated the effect of blowing on vortex shedding and aerodynamic noise due to flow over a circular cylinder. The flow simulation is performed by the URANS equations using k-ω-SST turbulence model. Calculations of the aerodynamic noise are performed through F-fowcs Williams-Hawkins analogy. The cylinder’s cross-section with a diameter of D=16mm, and the blowing jet is applied through slot windows that are located on the cylinder back surface. In this study, three positions for slot windows are considered. Verification of the numerical results is confirmed by comparing numerical results with the reported experimental ones (Uncontrolled case). The results showed that the optimal blowing position could reduce noise, lift coefficient, and drag coefficient; this result occurs for a slot window located near the cylinder horizontal axis of symmetry. On the other hand, if the blowing slot is located at the cylinder symmetric vertical axis, the aerodynamic noise increases by approximately 4 dB. In this case, the average lift and drag fluctuations are increased by more than 200%. The present study gives a new idea to the reduction of noise of the single body systems.Keywords: Circular cylinder, Reduction noise, Aerodynamic noise, Vortex shedding
-
Pages 245-253A cavitator, with a structure of an annular conical aperture, a throat and a collapse cavity, was proposed to form a choking cavitation flow for pollutants degradation in wastewater treatment. Experiment was conducted in this new cavitator to investigate its flow characteristics and pollutant degradation ratio by employing Mythylene blue (MB) as a pollutant in pure water. It was found that choking cavitation flow appears in the throat by controlling the pump pressure and liquid flow rate in a rule. The pollutant degradation ratio in choking cavitation flow is much larger than that in normal cavitation flow, because plenty of cavitation vapours are born, grow up, and finally collapse in this cavitator in the choking cavitation condition. Gemetrical parameters also affect pollutant degradation ratio, and the optimal gemetrical parameters for this proposed cavitator are suggested.Keywords: Cavitation, Choking flow, Degradation, Throat, Pollutants
-
Pages 255-269The effect of Gurney flap height and mounting position on the head coefficient of a centrifugal fan at different Reynolds numbers is investigated experimentally. Quarter round Gurney flap of 1.0, 1.5, 2.0 and 2.5 mm height is mounted at three different positions, S=1.00 (impeller tip), S=0.95 and S=0.90 on the pressure surface of the impeller blade tip. Performance tests are carried out on the centrifugal fan at five Reynolds numbers corresponding to five rotational speeds of 1100, 1500, 2000, 2500 and 2900 rpm respectively. From the performance curves it is found that the fan head coefficient increases significantly with Gurney flaps at low Reynolds numbers and increases marginally at high Reynolds numbers. Effect of Reynolds number on the head coefficient is considerable for the baseline fan and found to be negligible for the fan with Gurney flaps, for all combinations of Gurney flap mounting position and height. The head coefficient of the fan improves as Gurney flap height increases but the improvement is marginal after certain height of Gurney flap. The head coefficient of the fan deteriorates when Gurney flap is mounted away from the impeller blade tip.Keywords: Centrifugal fan, Gurney flap, Gurney flap height, Gurney flap mounting position, Reynolds number, Head coefficient, Flow coefficient
-
Pages 271-281We investigate the effect of an axial Poiseuille annular flow on the stability of Taylor vortices via numerical simulation using CFD Ansys Fluent software. The working conditions are identical to those of the Taylor-Couette experimental device of the LaSIE laboratory, where the inner cylinder is rotated. An incompressible fluid of density ρ= 998 kg/m3, with a kinematic viscosity m2/s at a temperature T= 19.5 °C is considered. The geometrical parameters of the flow system are characterized by a height H=275 mm, a radius ratio η=0.804, and an axial aspect factor Γ=45.45. The axial Reynolds number and Taylor number are respectively in the ranges of , and . Flow control is carried out according to two distinct protocols to bring out the effect of axial flow on the evolution of the Taylor vortex Flow (TVF). The first consists of superimposing an azimuthal flow around the critical TVF threshold with increasing axial flow until the Taylor vortices disappear. In the second, an axial field is set and the Taylor number is varied until onset of the TVF mode. It is predicted that in the presence of an axial flow, the critical threshold for first instability triggering (TVF) is delayed. In addition, the ratio of the axial phase velocity to the mean axial velocity of the axial base flow is 1.16. This value agrees well with previous results reported in literature.Keywords: Taylor-Couette flow, Axial flow, Taylor vortex, simulation
-
Pages 283-292The biological surface structure comprising fish scales and a mucous membrane exhibits good turbulent drag reduction ability. Based on this structure, a bionic frictional drag reduction model composed of a grooved structure and mucous membrane was established herein, and its efficacy in reducing the resistance of a turbulent boundary layer was analyzed. Accordingly, the drag reduction performance of the bionic structure was investigated through large eddy simulations. The results revealed that the mucous membrane was evenly distributed on the groove wall through secretion, and effectively improved the drag reduction rate of the groove wall. The bionic grooves and mucous membrane structure successfully inhibited the turbulent kinetic energy, turbulence intensity, and Reynolds stress. The grooved structure improved the shape of the Λ vortex structure and the mucous membrane reduced the number of three-dimensional (3D) vortex structures. Furthermore, the streak structure near the bionic structure wall was reduced and its shape was regularized, which intuitively demonstrates the turbulence suppression ability of the proposed bionic structure. This paper presents the results of a hydrodynamic analysis of the frictional drag reduction characteristics of a bionic structure consisting of grooves and viscous membranes acting on the turbulent boundary layer of a wall.Keywords: Mucous membrane, Bionic drag reduction, Viscoelastic fluid, Turbulence statistics, Coherent structure
-
Pages 293-309Aiming at better controlling the ventilated supercavity flow for drag reduction, the experimental and numerical researches of supercavity by rear gas reflux are proposed in this paper. Several experiments with different test bodies have been carried out to study the formation and collapse conditions of jet-reflux supercavity. An open-circulation water tunnel for ultra-high-speed jet experiment and air jet system is employed to form jet-reflux supercavity around the bodies installed in the forward strut. The experiment results show that the supercavity can be maintained by the reflux of tail jet flow when an initial supercavity covering the jet outlet is formed. However, the supercavity will be destroyed when the jet intensity is further enhanced. Under the same jet coefficient, the scale of jet-reflux supercavity extends as the increase of the body length, while the critical jet coefficient for the collapse of the supercavity decreases as the increase of the body length. The multiphase flow model coupling the VOF model and the level-set method is applied to capture the air-water interface. Then, the flow field characteristics of the jet-reflux supercavity are analyzed and compared with the ventilated supercavity. The streamline inside the cavity presents considerable three-dimensional asymmetry inflating flow characteristics. The variation of the gas reflux coefficient along the axial direction is obtained, which indicates that a handful of reflux gas are required to sustain the head cavity. Therefore, the jet-reflux supercavity can be formed within a certain range of the tail jet intensity. Although jet intensities are not equal to each other, the scale of cavity head is roughly maintained under the same reflux coefficient. When the supercavity gets closed to the nozzle outlet, the maximum scale of cavity is decreased, which leads to a weaker reflux at the outlet. The cavity interface will be impinged by the high-speed gas and mixture liquid, which obviously causes deformation and final collapse. In order to improve the stability of the jet-reflux supercavity, it is necessary to use the gas re-directed structure to control the reflux.Keywords: Supercavitation, Ventilated supercavity, Gas jet, Tail jet reflux, Entrainment, Water tunnel