فهرست مطالب
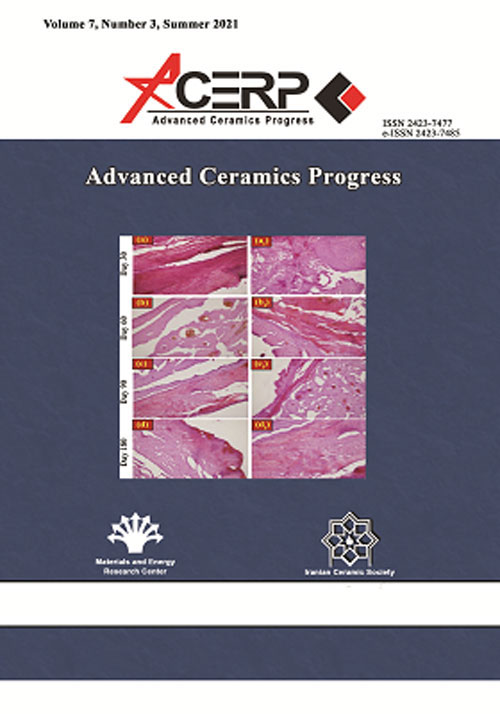
Advanced Ceramics Progress
Volume:7 Issue: 4, Autumn 2021
- تاریخ انتشار: 1401/02/08
- تعداد عناوین: 6
-
-
Pages 1-9
Recently, Alkali-Activated Concrete (AAC) as an appropriate alternative to Portland Cement Concrete (PCC) has drawn considerable attention owing to its acceptable properties and less environmental impacts. The current study presents a review of previous researches on Alkali-Activated Slag Cement Concrete (AASCC). The following issues are also covered in this study: an introduction to AASCC and its constituents, environmental impacts, hydration reaction, hydration products, mechanical properties, high temperature resistance, attack resistance of acids and sulfates, water absorption, shrinkage, and its challenges in application. The results from different studies revealed a research gap to be filled. To be specific, several different parameters affect AASCC properties; however, given that its properties are still partially unexplored, more researches are needed to find out its best engineering properties.
Keywords: alkali activated slag, Alkaline Concrete, ground granulated blast furnace slag, Mechanical properties, Chemical properties -
Pages 10-19Many researches have been conducted so far to improve the bioactivity and mechanical properties of bioceramic-based scaffolds in order to stimulate tissue attachment to the implant surface and create a stable bonding. In this research, Al2O3 scaffolds were prepared using different types of polyurethane foam through template replica method and then, they were sintered at 1650 °C. A sol of SiO2–CaO– P2O5–MgO system Bioactive Glass (BG) was synthesized where the scaffolds were soaked and heat-treated at 800 °C based on thermo gravimetry analysis. X-ray diffraction confirmed the presence of silica in the structure of BG coating diffused in alumina scaffold that caused the formation of sillimanite phase. According to Scanning Electron Microscopy (SEM) analysis, all prepared scaffolds were highly porous, and the mean porosity percentage was approximately 85 %. The compressive strength and porosity percentage of the scaffolds nearly ranged between 0.35-1.75 MPa and 79-93 %, respectively. The sample with the best result of compressive strength was considered as the optimum alumina scaffold (OAS). In vitro acellular behavior of the samples was also evaluated followed by soaking them in the simulated body fluid, and the ball-like morphology including entangled needle-like crystals were observed on the surface of the sample. Moreover, cells were cultured in alumina scaffolds with and without BG coating and in the cell studies. According to the findings, both samples supported attachment and proliferation of osteoblasts. Therefore, Based on the scaffold porosity percentage which promotes cell attachment as well as the compressive strength which is close to that of the trabecular bone, it can be concluded that application of BG-coated alumina scaffold as a bone-healing material may be beneficial.Keywords: Alumina scaffold, Bioactive Glass, cell culture, coating, porosity
-
Pages 20-27Topological characterizations and optical density of the synthesized hydrogenated amorphous carbon Cu-Ni NPs @ a-C: H nanotubes (CNTs) with different surface morphology were studied in this report. Films deposited with Ni layer thickness of5 nm have a maximum value of optical density especially in high energy range. Steps between 1800 to 2000KeV in the Rutherford backscattering (RBS) spectra are correspond to the presence of Cu and Ni elements. The thicknesses of films were measured by using SIMN-RA software. Films deposited with Ni layer thickness of 15nm have a maximum value of the lateral size of nanotubes in about 19.7nm.The grown CNTs of films deposited with Ni layer thickness15nm Ni, has a maximum value of diameter in about 16.2nm. The diagram of bearing area proportion height shows the percentage of cavities and single-layers. The cavity coverage of films was less than 5% and the layer content of films was about 90%.Keywords: Topography, Bearing Area, Nanotubes lateral size, Fractal dimensions, Optical Density
-
Pages 28-35Nowadays, Response Surface Methodology (RSM) is widely used for modelling and optimizing the performance of manufacturing technologies. Obtaining the optimum process parameters based on powder metallurgy methods is of great concern in manufacturing. In this paper, appropriate milling time for fabrication of Cu/SiC nanocomposites was determined to maximize the densification and hardness of the nanocomposite samples. The samples were prepared by high-energy planetary ball milling of the powders and conventional uniaxial pressing and sintering method. Microstructural characterization was carried out using scanning electron microscopy and optical microscopy, and the hardness of the samples was measured through Vickers microhardness tester. The highest hardness of 170 HV and minimum densification of 0.74 were obtained for the sample milled for 25 h. In addition, the effects of milling time on the hardness and density of the sintered samples were evaluated using one-factor RSM. Polynomial mathematical models were successfully developed to determine the relative density and microhardness of the sintered samples. The analysis of variance confirmed that the suggested models could be satisfactorily employed to predict the relative density and microhardness.Keywords: copper, SIC, Composites, Powder Metallurgy, Response Surface Methodology
-
Pages 36-51The current study aims to analyze the thermal and residual stress distributions in both duplex and functionally-graded thermal barrier coatings (TBCs) of yttria-stabilized zirconia (YSZ) and gadolinium zirconate (GZ) during a realistic heating regime. To this end, finite element model was employed to model the effects of thermal loading on the thermomechanical response and stress distribution. In addition, three different YSZ-based TBC systems, one duplex, and two FG-TBCs were fabricated using the APS method. The coatings were characterized based on SEM/EDS, map analysis, and XRD. The residual stress, elastic modulus, microhardness, and fracture toughness of the coatings were determined using nanoindentation method. The obtained results revealed that the microstructure, porosity, and chemical composition changed gradually due to the functionally-graded coating. Examination of the surface of the samples after the application of thermal shock showed that the separation of the layers occurred more frequently in the cases of two-layer coatings than in the graded ones. The contours of the heat flux and nodal temperatures confirmed that most of the damaging thermal residual stresses were concentrated in the ceramic top coat, thus resulting in less damage and life-shortening of the substrate. The magnitude of the residual stress in the FG-TBC was lower than that in the duplex TBC, and the stress distribution was more uniform, hence improvement in the performance and extention of the life of the thermal barrier system. According to the findings, the YSZ-based TBC outperformed the gadolinium zirconate-based TBC in terms of thermal shock resistance and residual stress.Keywords: Functionally Graded Thermal Barrier Coating (FGTBC), Thermal shock, Residual Stress, Nano-indentation, Finite element method
-
Pages 52-58The main objective of this study is to assess the structure and mechanical properties of amorphous aluminum phosphate (AlPO4) ceramic specimens prepared through Spark Plasma Sintering (SPS) method. To this end, AlPO4 powder was synthesized through sol-gel process and consolidated by SPS at the sintering temperature range of 800-1300 °C. Ceramic specimens were characterized by X-Ray Diffraction (XRD) and Scanning Electron Microscopy (SEM) analyses. Bulk density of the samples was measured using Archimedes’ principle. In addition, hardness and indentation fracture toughness of the samples were determined to identify the mechanical properties. The results from XRD analysis, SEM images, and density measurement revealed that the sintered sample was characterized by an amorphous structure with the porosity of ~ 3 % and relative density of 97 % after SPS at 1000 °C for 15 min. Increasing the temperature to 1300 °C made the amorphous AlPO4 crystallized. The fracture toughness was obtained to be 5.75 MPa.m1/2 under this sintering condition. Crack deflection around porosities was identified as the main toughening mechanism involved.Keywords: Amorphous AlPO4, Spark Plasma Sintering, Mechanical properties, Fracture toughness