فهرست مطالب
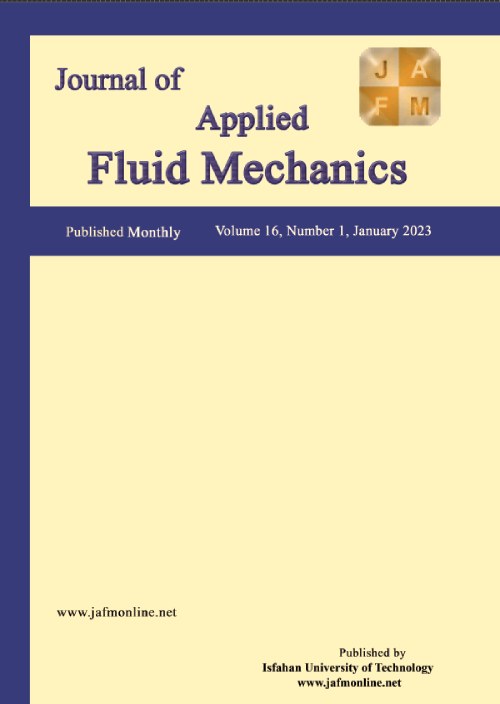
Journal Of Applied Fluid Mechanics
Volume:16 Issue: 2, Feb 2023
- تاریخ انتشار: 1401/09/20
- تعداد عناوین: 15
-
-
Pages 205-221The study focuses on heat transfer performance and flow structure associated with swirling jet on a flat target surface. The analysis is carried out with helicoid inserts of swirl number S = 1.3 by varying the number of vanes with Reynolds number between 11200 and 35600. The comparison of swirling jet with circular jet is carried out on its heat transfer performance. The heat transfer and flow structure are visualized using thermo-chromic liquid crystal sheet and oil film technique respectively. The numerical simulation is also performed at Re = 24700 for H/D distance between 1 and 4 using computational fluid dynamics. The heat transfer results reveal that the presence of axial recirculation zone at Re = 29800 and 35600 for the triple helicoid affects the uniformity of heat transfer distribution at 0 < X/D < 1.5 at H/D = 3. The axial component of velocity with respect to swirling jet is less than zero in the stagnation area and it increases at 0.57 < r/D < 0.97 for single vane and 0.63 < r/D < 0.97 for double and triple vanes. While the steep increase in tangential velocity of the triple vane jet is apparent at 0 < r/D < 0.5 at H/D = 2 and 3, the maximum value of point radially shifts inward towards the jet. The location of maximum turbulent kinetic energy approaching the surface at about r/D = 0.9 - 1.2 which characterizes the swirling jet at H/D = 2.Keywords: Heat transfer, Thermochromic liquid crystal, Swirling jet, CFD, Flow characteristics
-
Pages 223-231The overall cooling performance of turbine nozzle guide vane, with the impingement-cutback structure, is experimentally studied in the actual-scale cascade. The gas with the high temperature is used to achieve the actual dynamic viscosity coefficient and the density ratios. The coolant-to-gas mass flow ratio (KG) varies between 0.034 and 0.050 and the gas-to-coolant temperature ratio (KT) varies between 1.5 and 2.4. The local Overall Cooling Effectiveness (OCE) on the middle cross-section of the vane is obtained. The experimental results reveal that the lowest value of the OCE achieves a 10% relative arc length on the suction side of the vane; however, the highest value appears at 40% relative arc length on the pressure side of the vane. The averaged values of the OCE are respectively enhanced by 19.45%, 24.22%, and 35.57% at temperature ratios equal to 1.7, 1.9, and 2.3, with an increase of the KG from 0.034 to 0.050. Added to that, it was identified that an increase of KT from 1.7 to 2.3 leads to the decrease of the OCE. The comparison results show that this characteristic becomes dramatical while KG is 0.034. The higher KT leads to a greater influence of KG, which is illustrated clearly by the compared results of the OCE.Keywords: Turbine cooling, High temperature, Mass flow ratio, Temperature ratio, Impingement cooling
-
Pages 233-243In this study, complex processes in a typical Electric Arc Furnace (EAF) such as combustion, radiation, heat, and mass transfer were solved and the optimum injector location was found using computational fluid dynamics (CFD). The main aim of the injection optimization was to improve the thermal performance and the metallurgical process by changing the injection angle, the central angle of the injector (CAI), and injector length. Fifteen parametric cases were predicted and analyzed for optimization study. To decrease each simulation solution time of each cases, a polyhedral mesh structure was used instead of tetrahedral mesh for the EAF geometry. Thus, the total element number of the model was decreased by 1/5 while providing faster and unchanging results compared to the case with a tetrahedral mesh structure. The response surface optimization method was used for the optimization study. As a result, the optimum injector positioning was obtained as injection angle: -45°, injector length 614 mm, and CAI: 60°.Keywords: Electric Arc Furnace (EAF), Computational fluid dynamics (CFD), Fine coal combustion, Injectors, Optimization
-
Pages 245-256This study reconstructed the flow field of a symmetrical variable inlet guide vane in a centrifugal compressor through the passive control method of vane slots. Based on the high-fidelity numerical simulation model verified by experiments, the influence of different slot forms on the flow field was investigated, and the passive control mechanism was revealed. The results demonstrated that the vane slot method can effectively suppress the suction surface separation and broaden the range of low-loss incidence angles. Overall, the 50_30 slotted vane achieves the best flow field control, with a 65.6% reduction in the total pressure loss coefficient and a 2.3° reduction in the deviation angle, respectively, at a 25° incidence angle. The linear characteristics of the pre-swirl grade variation curve with variable inlet guide vane incidence angles are also improved. Furthermore, changing the slot outlet angle has the most significant influence on the aerodynamic performance as it changes the throat width of the location, thereby affecting the flow rate and momentum of the jet. Finally, the impact of the velocity varies in the first self-similarity region on the slotted vane. The results indicate that, in contrast to the baseline vane, the suppression effect of the slot jet on the flow separation improves with the inlet velocity, whereas the deviation angle of the slotted vane declines with the inlet velocity. Meanwhile, the higher the incoming flow velocity, the better the slotted jet can inhibition of flow separation.Keywords: VIGV, Slot, Aerodynamic performance, Compressor, Pre-swirl
-
Pages 257-267The modern fuel injectors work with ultra-high injection pressure with a micro-size nozzle, which inevitably triggers the cavitation flow inside the nozzle. The formation of vapor bubbles and their development inside the nozzle is difficult to characterize due to its highly fluctuating spatial and temporal parameters. The numerical models can predict the temporal behavior of cavitating flow with the real-size nozzle geometry, which is fairly expensive with the experiments. A systematic study has been carried out using throttle geometry to characterize the cavitation flow. The different turbulence, multiphase, and cavitation models are extensively evaluated and validated with experimental data. A combination of numerical models has been proposed to predict the cavitation flow more accurately with low computational time. The results obtained with the k-ω SST (Shear Stress Transport) turbulence model and the ZGB (Zwart-Gerber-Belamri) cavitation model are more consistent with the experimental results. The overall structure of cavitation is well captured with both the VOF (Volume of Fluid) and the Mixture multiphase models. Although, the smaller structures like bubble formation and ligament breakup are only captured with the VOF (Volume of Fluid) tuned with the sharp interface method. The effect of pressure difference on the cavitation flow has been estimated with diesel and bio-diesel fuel. The effect of nozzle conicity on cavitation phenomena has also been reported.Keywords: Cavitation, Fuel injection, Nozzle, Two-phase flow, CFD
-
Pages 269-283A co-flow jet (CFJ), an active flow control method combining blowing and suction control, can effectively suppress the stall of airfoils. However, the streamwise jet channel along the upper surface of a conventional CFJ airfoil reduces the thickness and camber of the baseline, degrading the aerodynamic performance when the jet is inactive. The conformal slot CFJ airfoil was proposed to address this problem, but the design method is still absent. This paper proposed a general design method based on parameters including the slot angle, transition shape and distance of the injection and suction slot. The mechanism of the best parameter was analyzed. The designed conformal slot CFJ airfoil was checked under different jet intensities, and the turbine power curve was predicted when substituting CFJ airfoils for the baseline. Compared with the conventional CFJ airfoil, the designed conformal slot CFJ airfoil has three advantages: eliminating the performance loss when the jet is off, saving jet energy when suppressing the flow separation, and improving the power generation of wind turbines at low wind speeds.Keywords: Co-flow jet, Wind turbine airfoil, Conformal slot, Blowing, Suction, Flow control
-
Pages 285-297This paper investigated the variable speed operation of a two-way contra-rotating axial flow pump–turbine in pump mode. When counter-rotating impellers operate at the same speed, a significant difference exists in the shaft power of the two impellers, thereby causing difficulties in motor selection. However, the same motor is required for both impellers in two-way pump–turbines. To solve this problem, this paper aims to determine the appropriate speed at which the two impellers operate with a similar shaft power. Accordingly, improving the performance of the tidal unit while enabling the basic functions of the pump–turbine is of considerable engineering and academic significance. An analysis of performance variations of the front and rear impellers in the pump mode reveals the law of power variation for each impeller at different speeds of the rear impeller. Under different flow conditions, shaft power of the rear impeller is found to be at least 31% higher compared with that of the front impeller. This result provides practical reference for further research on the operation of counter-rotating axial flow pump–turbine.Keywords: Tidal energy, Two-way Contra-rotating, Pump-turbine, Variable speed, Vortex characteristics
-
Pages 299-310The land needed to install wind turbines is shrinking as power generation from renewable energy sources increases significantly. A large number of studies are being conducted to maximize the power extraction from wind turbines in areas with low wind speeds. Wind turbine blades play a significant role in utilizing the maximum amount of energy from the wind. The aerodynamic performance of a wind turbine blade depends on the airfoil shape. The shape optimization of an asymmetric S2027 airfoil for a low wind speed region was investigated using the adjoint-based optimization technique. The primary objectives of this study were to maximize the lift coefficient, minimize the drag coefficient, and maximize the lift-to-drag ratio. The optimization is based on the adjoint method for Reynolds number variation in the range of 2 × 105 to 5 × 105 and an angle of attack variation from 0° to 12°. A two-dimensional Reynolds–Averaged Navier–Strokes Computational Fluid Dynamics model was created with all the operating parameters and used for optimization. The aerodynamic performance was validated experimentally. For each optimization function, approximately 16 shapes were obtained. The aerodynamic performance for each optimized shape was determined under different operating conditions. Different airfoil shapes with a specific chord, leading and trailing edges, and span arrangement was obtained. The drag coefficient was reduced by 2%–30%; the lift coefficient was improved by 2%–35%, and the lift-to-drag ratio was improved up to 40%.Keywords: Airfoil shape optimization, Wind turbine blade, XFOIL, ANSYS Fluent, Numerical Simulation Wind tunnel
-
Pages 311-323In the present study, various groove casing treatments were evaluated under a high-speed subsonic axial flow compressor using experimental and numerical simulation methods. The aim of this study was to explore the effect of inclination of grooves on compressor stability and performance. The potential flow mechanisms were also evaluated. Three different inclination grooves were designed in this study: grooves with no inclination, grooves with 30 degrees upstream inclination and grooves with 30 degrees downstream inclination. Similar effect of the grooves on the compressor stability and efficiency was observed under experimental and numerical analyses. The grooves with no inclination, 30 degrees upstream inclination and 30 degrees downstream inclination enhanced stall margin by 6.08%, 8.74% and 3.03%, respectively. The peak efficiency losses of the three types of grooves were 1.62%, 0.94% and 2.33%, respectively. Tip flow field analyses demonstrated that the radial transport effect caused by grooves effectively reduced tip loads and alleviated tip blockage. This explains why the grooves enhanced the compressor stability. The radial transport effect was enhanced, and a larger stall margin improvement was obtained when grooves inclined upstream were applied. The tip flow loss was the dominant loss observed after grooves were applied on the compressor. The grooves with upstream inclination markedly reduced the tip flow loss, indicating that they exhibited the lowest effect on reducing compressor efficiency compared with the other types of grooves.Keywords: Axial compressor, Casing treatment, Inclination groove, Stability, Tip blockage
-
Pages 325-336Ice accretion threatens aircraft safety. With the wide application of unmanned aerial vehicles (UAVs), the design of ice-tolerant UAVs has become a problem that must be solved. Forty conditions for the continuous/intermittent maximum icing conditions were sampled in Appendix C of Federal Aviation Regulations Part 25. Herein, numerical simulations of icing were performed on an NACA 0009 airfoil for 5, 15, and 30 min, and the ice mass and ice shapes were obtained at different times. Numerical simulations of the aerodynamic characteristics of the iced configuration at 5, 15, and 30 min were conducted, and the coefficients of lift, drag, and pitch moment were obtained. Surrogate models of the ice shape, mass of the ice accretion, lift coefficient, drag coefficient, and pitch moment coefficient at different moments were built based on proper orthogonal decomposition and kriging interpolation. The results demonstrate that the surrogate models accurately predicted the ice shape, ice mass, lift coefficient, drag coefficient, and pitch moment coefficient at different moments. Compared with the numerical simulation results, the maximum relative errors of the ice mass, lift coefficient, drag, and pitch moment predicted by the surrogate models were 7.8%, 3.4%, 3.9%, and 7.6%, respectively. This method can help in designing the ice-tolerant UAVs and envelope determination under icing conditions.Keywords: Ice tolerance, Envelope protection, Icing, POD, Kriging
-
Pages 337-352The aerodynamic performance of four train models with different windshield configurations (i.e., internal and/or external) in three train marshalling modes (i.e., 3, 6 and 8-car groups) was numerically investigated in this study. The train's airflow characteristics at Re=2.25×106 were determined using the shear stress transport (SST) k- turbulence model. The results were validated by comparing the pressure distributions and drag forces on the streamlined heads with experimental data. The difference in windshield configuration and train length has a substantial influence on the train’s flow field and surface pressure distribution. For the trains with internal windshields, due to non-uniform geometry, the flow is separated and vortices are formed at the windshield area. The boundary layer profile increases with the increased train length, and its thickness varies with windshield configurations. Asymmetric vortices are formed in the wake at a distance close to the tail car’s nose, except for trains with external windshields. The reduction of the flow velocity as the train length increases causes a reduction of the low pressure near the tail car’s streamline transition, thus causing a decrease in the tail car’s drag and lift forces. Consequently, for trains with external windshields, the head car’s drag increases, whereas the total train drag reduces significantly as the train length increases. Therefore, employing external windshields in all the inter-carriage gap sections, irrespective of the train length, demonstrates a good ability to reduce future train’s aerodynamic drag.Keywords: High-speed train, Windshield configuration, Drag force, Flow field, Pressure distribution
-
Pages 353-361The corrugated lobed nozzle is an emerging research topic in jet flow dynamics, and little investigation has been conducted on its effect on flow characteristics. Thus, in this study, the effects of lobe count and lobe length of corrugated lobed nozzles on subsonic jet characteristics were experimentally investigated by analyzing the velocity profiles of the jets emanating from the nozzles. The Pitot tube readings were obtained by varying the count (4 ≤ N ≤ 8) and length (10 mm ≤ L ≤ 20 mm) of corrugated lobes. These measurements were then compared with the experimental readings obtained for a baseline circular nozzle. The nozzle pressure ratio (NPR) and exit nozzle area were kept identical at 1.5 and 600 mm2, respectively, for all nozzle configurations. The most striking observation was the ‘W’-shaped radial velocity profile of the corrugated nozzle, which differed from the ‘Top hat’ profile of the baseline circular nozzle. Additionally, the length of the potential central region of the corrugated nozzle was always shorter than that of the baseline circular nozzle, indicating the early occurrence of turbulence in the former. It was found that the lobe length had a meagre effect on the velocity variation in the jet issuing from the corrugated nozzle, whereas the lobe count had a significant effect on the velocity profile. However, as the lobe count increased, the velocity profile of the corrugated nozzle gradually resembled that of the circular nozzle. The findings of this study would be beneficial for selecting a proper lobe count and lobe length while designing and implementing a corrugated lobed nozzle.Keywords: Corrugation, Jet, Lobe, Pitot tube, velocity profile
-
Pages 363-374A simple model consisting of a mirror-housing and its cylindrical foot is applied to represent the automobile side-view mirror that causes unwanted aerodynamic noise and wind drag during high-speed driving. An additional slot is made on the solid foot to modify the flow around the mirror and thus reduce the side wall pressure fluctuation and aerodynamic drag. Flow fields and wall pressure fluctuations of these side-view mirror models have been investigated experimentally in a wind tunnel. The airflow rate through the slot varies with the changing of the slot area. Wall surface pressure sensors, particle image velocimetry (PIV), and six-component balance were applied to measure the acoustic and flow characteristics. The results demonstrated that, with the increase of slot airflow rate to 30%, the side wall pressure fluctuations were reduced by 5.1 dB and the drag coefficient decreased by 10.2%. The PIV measurements showed that the vortex cluster center behind the mirror was moved upward from the wall surface due to the slot airflow injection into the wake. The turbulent kinetic energy in the side-view mirror wake near the wall decreased with the increment of the airflow rate, reducing the side wall pressure fluctuations and thereby suppressing the noise generation.Keywords: Automobile side-view mirror, Wall pressure fluctuation, Aerodynamic Drag, Wind tunnel test, PIV
-
Pages 375-388The steady and unsteady characteristics of the internal flow in a high-speed centrifugal blower are studied by computational fluid dynamics (CFD) approach at low flow rates. It is demonstrated that as the flow rate decreases, the separation of flow in the blade passage becomes serious, and separated vortexes always occur on the suction surface of the blade which gradually expand and block the passage. The stall cells move downstream and generate vortices at the exit of the passage, resulting serious loss to the performance of the blower. Q-criteria is used to analyze the flow field and explore the evolution of the vortex structure in the impeller. It is further found that strong pressure fluctuations are caused by the rotating stall in the impeller. At the stall conditions, the instability characteristics are particularly obvious. At flow rates of 0.65Qn and 0.47Qn, the pressure fluctuation in the blade passage is dominated by the blade passing frequency, while a lower frequency dominates at 0.26Qn. Moreover, the flow on the suction surface of impeller blades fluctuates substantially. The characteristics of steady flow and unsteady flow can clearly explain the internal flow of centrifugal blower for vacuum cleaners at low-flow conditions, which can be widely used in various engineering designs of vacuum cleaners.Keywords: Centrifugal blower, Unsteady flow, Rotating stall, Spatiotemporal characteristics, Pressure fluctuations
-
Pages 389-399The outlet blade angle is a key geometrical parameter that governs how the impeller directly influences centrifugal pump performance. Therefore, a reasonable angle selection is crucial. To investigate the effects of the outlet blade angle on centrifugal pump internal flow field characteristics under cavitation conditions, this study employs a combination of a modified SST k-ω turbulent model with a Zwart-Gerber-Belamri cavitation model to perform transient flow simulations. Outlet blade angles of 15°, 20°, 25°, 30°, and 35° were tested. The results indicated that as the outlet blade angle increased, the relative liquid flow angle, vapor volume, and corresponding fraction first increased, then decreased, and finally increased again. Meanwhile, the distribution scope of each stall vortex on the suction surface became smaller, then larger, and smaller again, whereas the scopes of the pressure surfaces grew constantly as the outlet blade angle increased. Pressure fluctuations at all monitored points in the volute became weaker over time, and variations in the pressure fluctuations alternated with the outlet blade angle. The main frequency amplitude increased and the frequency doubling decreased as the outlet blade angle increased. Although the energy corresponding to the main frequency was unstable, it consistently held the dominant position. The duration that cavitation compliance was less than 0 first decreased and then increased as the outlet blade angle increased. For the impeller with an outlet blade angle of 25°, stall vortices accounted for the smallest regions, and the duration of negative cavitation compliance was minimized. In this case, the overall performance of the centrifugal pump was optimal.Keywords: Centrifugal pump, Outlet blade angle, Cavitation, Net positive suction head available, Net positive suction head required, Computational fluid dynamics