فهرست مطالب
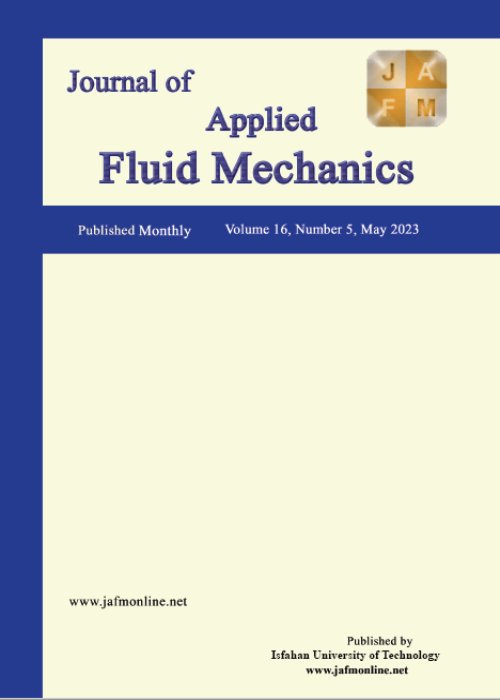
Journal Of Applied Fluid Mechanics
Volume:16 Issue: 5, May 2023
- تاریخ انتشار: 1402/02/05
- تعداد عناوین: 15
-
-
Pages 905-919The parameters of the compression wave propagating in a railway tunnel are significantly influenced by the large ambient air temperature variation throughout the year. High-speed train entering a railway tunnel produces a wave of finite amplitude to propagate at sonic speed. The wave attenuates while propagation through viscous dissipation and inertial forces nonlinearly steepen the wave. As a result of the dependence of sound speed on air temperature, the wave characteristics are altered with changing temperature. Therefore, it is crucial to comprehend the impact of ambient air temperature on the properties of the compression wave in order to construct an aero-acoustically ideal railway tunnel system. The method of characteristics (MOC) has been used to solve Euler equations with steady and unsteady friction parameters in the current study. According to the findings, wave attenuation ratio is reducing along the tunnel length, and gradient is rising as train speed increases. The case study illustrates the key distance within a tunnel where the steepening ratio is at its highest point. This critical tunnel length is estimated to be 65 times the tunnel hydraulic diameter (300 km/h) for a particular air temperature (T = 323 K), and it decreases by 15% for a 70 K reduction (323K to 253K) in temperature. Similarly, the critical length falls by 40% for greater train speeds (500 km/h).Keywords: Non-linear effect, Tunnel aeroacoustics, Unsteady friction, Wave distortion, wave propagation
-
Pages 920-931Because the helical axial flow gas-liquid mixing pump has the great advantage of conveying gas-liquid two-phase mixed medium, it has become the main core equipment for deep-sea oil and natural gas exploitation. The gas phase aggregation and bubble movement trajectory in the impeller channel have been widely studied, but the increase of medium flow resistance caused by flow separation has not been deeply discussed. Combined with the Euler multiphase flow model and the SST k-ω turbulence model, the numerical calculation of the helical axial flow gas-liquid mixed pump is carried out. Under design flow conditions Q = 100 m3/h, head H = 30 m, speed n = 4500 r/min, specific speed ns =213.6 r/min, and under different inlet gas content conditions, the influence of the bionic waveform leading edge blade on drag reduction characteristics of the helical axial flow gas-liquid mixed pump was investigated. By designing the blade with a leading-edge structure with different heights and pitches, the separation of the mixed medium and the suction surface is effectively suppressed, and the flow resistance of the medium in the 1/10 area of the inlet end of the blade is reduced. The results show that when the height A is 0.25%L and the pitch λ is 12.5%h, the maximum drag reduction rate in this region is 52.6%, the maximum increase in efficiency of the mixed pump is 2.2%, and the maximum increase in head is 4.8%. This study can provide technical support for flow drag reduction in gas-liquid mixed pump.Keywords: Helical axial flow gas-liquid mixing pump, Waveform edge, Separation, Drag reduction, Bionic waveform
-
Pages 932-946In this paper, numerical simulations have been performed to study the performance of a single fully activated flapping wing serving as energy harvester. The aims of the paper are predicting and maximizing the energy extraction efficiency by using optimization methodology. The metamodeling and the genetic algorithms are applied in order to find the optimal configuration improving the efficiency. A response surface method (RSM) based on Box–Behnken experimental design and genetic algorithm has been chosen to solve this problem. Three optimization factors have been manipulated, i.e. the dimensionless heaving amplitude h0, the pitching amplitude θ0 and the flapping frequency f. The ANSYS FLUENT 14 commercial software has been used to compute the governing flow equations at a Reynolds number of 1100, while the flapping movement combined from heaving and pitching of the NACA0015 foil has been carried out by using an in house user-defined function (UDF). A maximum predicted efficiency of 34.02% has been obtained with high accuracy of optimal kinematic factors of dimensionless heaving amplitude around the chord, high pitching amplitude and low flapping frequency of 0.304 hertz. Results have also showed that the interaction effect between optimization factors is important and the quadratic effect of the frequency is strong confirming the great potential of the applied optimization methodology.Keywords: Numerical simulation, Flapping wing, Energy extraction, Efficiency, Box–Behnken
-
Pages 947-959To investigate the accidental shutdown process for a large vertical and submersible mixed-flow pump unit in a drainage pumping station, a three-dimensional numerical method for this transition process was proposed according to the angular momentum balance theorem and rigid body rotation technology. We obtained the transient performance curves of the unit and the internal flow characteristics of the full flow channel. In addition, we also analyzed the energy loss distribution of the through-flow components during this progress based on the entropy production theory. The results show that the whole runaway process needs to go through four stages: the pump mode, the pump braking mode, the turbine mode, and the stable runaway mode. The pressure amplitude changes greatly in impeller and guide vanes, and the main fluctuation frequency is the blade frequency. There are higher harmonic frequencies in the dynamic rotor-stator interface. As the rotating speed increases in turbine mode, the negative pressure area near the impeller blade’s trailing edge gradually increases. The entropy production method can be used to determine the location, intensity of energy loss during the transient process. If the rotating speed exceeds the allowed value in the runaway turbine mode, the interaction between blade tip vortex and hub vortex rope may cause loss of stability.Keywords: Vertical, submersible mixed-flow pump, Accidental shutdown, Transition process, Entropy production, Computational fluid dynamics
-
Pages 960-972The present research aims to investigate the two-phase air/water flow in a vertical pipe using an electrical resistance sensor and a high-speed camera. An electrical resistance sensor is designed and embedded in the inner wall of the tube. A flow pattern map is drawn at the height of 270 cm from the testbed inlet for 320 different phase velocities using a high-speed camera. By measuring the output voltage of the electrical resistance sensor and using the Maxwell relation, the volume fraction in bubbly and slug flow regimes are calculated for different phase velocities. The volume fraction values detected from the output signal of the electrical resistance sensor are compared with the results obtained from the high-speed camera images. The width of the output signal from the electrical resistance sensor indicates the length of the Taylor bubble. The output signal width is compared to the obtained Taylor bubble length from high-speed camera images, for several different velocities of the phases. It is noticed that at a constant velocity of the phases, the output signal width from the sensor is linearly related to the length of the Taylor bubble. The variations of the output signal width are plotted in terms of the ratio of the Taylor bubble length to the summation of air and water superficial velocities. By linear fitting of the available data, a novel equation is presented to calculate the Taylor bubble length in terms of the signal output from the electrical resistance sensor and the total superficial velocity of the phases.Keywords: Multiphase flow, Transient flow regime, Vertical tube, Electrical resistance tomography, Taylor bubble length, Electrical resistance sensor
-
Pages 973-982Gradient metal foam is an advanced heat transfer material that decreases resistance to bubble escape and enhances the transfer of boiling heat. In this study, boiling heat transfer and bubble behavior were studied in an experimental set-up with copper foam bilayers configurated either in positive or inverse gradients, utilizing deionized water as working fluid. Positive gradient refers to arranging metal foam layers with high pore density at the bottom, above the heat source, and low pore density on the top. Results show that the heat transfer is higher for gradient metal foam surfaces, of 6.14×105 W/m2, versus a uniform metal foam surface, of 3.94×105 W/m2. For the positive gradient configuration, boiling heat transfer performance first increased with the pore density, then decreased when the pore density was higher than 60 pores per inch (PPI). By contrast, for the inverse gradient, the heat transfer performance was nearly constant with increasing pore density. At the low pore density, the inverse gradient performed better than the positive gradient during the whole boiling process. At high pore density, the positive gradient structure performed better in heat transfer at the early boiling stage. Three main types of bubble escape were observed: For the positive gradient bilayer, the bubbles moved up or down without lateral interference. In contrast, for inverse gradient, the bubbles mostly escape from the sides, which is easy to induce bubble merging. The inverse gradient surface generates larger bubbles, while the positive gradient surface produces a higher frequency of bubble detachment. Accordingly, two liquid replenishment models are proposed: for the positive gradient, external liquid replenishes from the side into the copper foam, while for inverse gradient, the liquid is mainly replenished from the top.Keywords: Gradient copper foam, Liquid replenishment, Bubble behavior, Heat transfer enhancement, Multiphase flow
-
Pages 983-991The purpose of this study is to determine whether it is possible to reduce the upstream and downstream length of a measuring pipeline by installing different types of air flow conditioners. The main goal is to investigate the distance position of these flow conditioners and thus analyze their impact on flow conditions within the pipeline. To improve the current conditions in the pipeline, an analysis was performed of how measurement accuracy was impacted by installing different types of air flow conditioners. Measurement accuracy would also be improved. The preliminary analysis included two different types of flow conditioners: Zanker and NEL. Both were inserted into a measuring pipeline for measuring velocity field and profiles, and thus reduce uncertainty during measurements. A CFD model was built for each type of the air flow conditioner that simulated its impact on velocity fields in the measuring pipeline using the ANSYS Fluent software package. Numerical results of velocity profiles were validated and compared with experimental result. The Zanker flow conditioner was selected for the installation in the measuring pipeline due to better results compared to NEL. Based on the numerical results, the air flow conditioner was optimized and the most suitable conditioner was selected, in this case D/10-V3.Keywords: Air flow conditioner, CFD, Pitot- Prandtl tube, velocity profile, Optimization
-
Pages 992-1004The load capacity and static stiffness of the existing air hydrostatic guideways are relatively low, and the static performance of the air film is degraded when external forces are increased during the process. Therefore, this study considered an aerostatic guideway of an ultra-precision micromachine tool as the research object. Single- and double-row orifice structures were designed on the guideway, and linear, extended, and X-shaped pressure-equalizing groove (PEG) structures with rectangular cross-sections were designed on the working surface of the guideway. By establishing a computational fluid dynamics model of the guideway air film, the pressure contour was obtained through simulation, and finally, the advantages of the double-row orifice structure were determined. Then, the influences of the structure, width, and depth of PEG and the diameter and number of orifices on the load capacity, stiffness, and air consumption were studied, which provided a theoretical basis for improving the load performance of the aerostatic guideway. The results showed that the design of the PEG effectively improved the load performance but increased the air consumption. The extended PEG exhibited the best load performance. When the eccentricity was large, the width of the PEG moderately increased, improving the load capacity and stiffness. While increasing the depth only improved the stiffness, it had little effect on the load capacity and air consumption. When the eccentricity was small, the diameter and number of orifices moderately increased. The experimental data were consistent with the simulation results, demonstrating the accuracy of the simulation method.Keywords: Aerostatic guideway, Pressure-equalizing groove, Load capacity, Stiffness, Air consumption
-
Pages 1005-1016Vibration and fatigue damage of pump shafts has become a prominent engineering problem, indicating the need for higher-quality reliability analysis of the pump unit in the design stage. In this study, the unsteady flow field in a large centrifugal dredge pump was numerically simulated via the unsteady Reynolds-averaged Navier-Stokes (URANS) method with the SST k-ω model. An experiment was carried out to verify the numerical method. The hydraulic radial force on the impeller and the total radial load were calculated based on computational fluid dynamics. The flow field with a double volute was simulated, analyzed, and compared to the flow field with a single volute. The stress of the pump shaft caused by the radial load was also calculated and discussed. The results show that the impeller gravity determines the time-averaged value and fluctuation frequency of the total radial load on the shaft, which must be considered in the shaft stability analysis. The total radial load fluctuating in asymmetric cycle results in stress cycles with different features at different circumferential locations. The application of a double volute effectively reduces the radial load on the pump shaft, which decreases the time-averaged hydraulic radial force by 38% and its fluctuation amplitude by 3%, decreases the time-averaged total radial load by 20% and its fluctuation amplitude by 28% in the design condition, and decreases the local stress at the narrowest shaft section by 44%. A double volute can be applied to weaken vibration and fatigue damage for a pump shaft if it is acceptable for the pump efficiency to be lowered.Keywords: Centrifugal dredge pump, Radial force, Gravity, shaft, Dynamic stress, Double volute
-
Pages 1017-1029In this research, we consider the influence of two kinds of domain on the numerical flow around a submarine model. A fully appended SUBOFF submarine model was used, and the structure and characteristics of the flow were investigated under a full domain and a symmetrical domain arrangement. The numerical simulation was carried out using the OpenFOAM software, and the flow was numerically modelled as single-phase and incompressible. The SST k-ω turbulence model was used in both domains, together with an insensitive Spalding wall function to represent the boundary layer near the wall. The results showed that simulations in both the full and symmetrical domains could accurately predict the total resistance. Compared to the symmetrical domain, the resistance value obtained with the full domain was more precise; the symmetrical domain under coarse grid conditions had an error value of 1.34%, whereas the full domain using the same grid size had an error value of 0.6%. Hence, the full domain was superior in terms of predicting the resistance with a coarse grid. Next, the pressure coefficient comparison at the leading edge of the rudder was calculated, where = 0.92, and the symmetric domain was found to have a value of 0.0747 whereas the full domain had a value of 0.236. Compared with the results from experiment (=0.302), the symmetric domain appears to give an underestimate for the pressure distribution at this position. In addition, the flow structures and properties in both domains differ, particularly in terms of the vortical structures generated by the sail and rudders. The simulation results for the full domain reveal that the flow around the SUBOFF model is asymmetric. The full domain was able to capture the flow structures in more detail than the symmetrical domain, and represented the velocity distribution at the propeller plane better. As a result, the full domain must be considered when carrying out propeller analysis and self-propulsion simulations.Keywords: Turbulent flow, Wall function, velocity distribution, Stern wake, Flow structures, Numerical accuracy, OpenFOAM
-
Pages 1030-1043Taking the electric eel as a bionic object, a long undulatory fin is designed. The turbulent model standard k-ε is used to solve the N‒S equation of a three-dimensional unsteady incompressible fluid. The hydrodynamic characteristics of the undulatory fin are studied, and the influence of the swing angle, wave frequency and ground effects on the propulsion performance of the undulatory fin are discussed. The mathematical models of the average thrust and average lateral force of the undulatory fin are established by using multiple linear regression. The results show that the thrust and lateral force of the undulatory fin increase with increasing swing angle and swing frequency, but in a motion period, the number of fluctuations of the thrust is approximately twice that of the lateral force. The relationship between the average thrust force and the average lateral force of the undulatory fin and the wave frequency and the maximum swing angle satisfies a specific exponential law. When the undulating fin moves near the wall (d ≤0.2 W), due to the coupling between the vortex at the lower edge and the tail vortex where part of the vortex is transferred to the two sides, the total thrust decreases, and the lateral force increases.Keywords: Bionic fin, Hydrodynamic characteristics, Propulsion performance, Wall effect, Mathematical model
-
Pages 1044-1056The vibration induced by the cooling fluid flow around the fuel rods in the fuel Assembly of nuclear reactors causes the rods to be destroyed and eventually leak due to the fretting wear in the place of contact with their supports for a long time. In this paper, the vibration caused by axial fluid flow around a specific fuel rod under elastic supports is numerically simulated. In this study, the fluid flow is modeled using the Large Eddy Simulation (LES) turbulence model in the FLUENT software. The fluid-structure interaction is also modeled using the ANSYS coupling system. To validate the implemented numerical model, the test results of the reported brass rod vibration similar to the studied problem in this research are used. Due to the long execution time of the two-way fluid-structure interaction simulations with a high grid number, the one-way fluid-structure interaction method is proposed. The results of simulations show that the one-way fluid-structure interaction method can be used in cases where the vibration amplitude of the structure is less than the height of the viscous sub-layer. Also, this method reduces the simulation time by 80%. Finally, the results of the flow-induced vibration simulation of the fuel rod show that the vibration range of the fuel rod will increase by 20 times if the contact of the elastic supports with the rod is lost, which will lead to the intensification of the wear caused by the rod oscillation. Also, the main natural frequency of the rod decreases when the rod loses contact with the supports and falls within the range of the reactor excitation frequency, i.e. 0 to 50 Hz, which should be avoided.Keywords: Flow-Induced vibration, One-way fluid-structure interaction, LES turbulence model, Fuel rod, Elastic supports
-
Pages 1057-1073In this study, the flow field of a new secondary-grooved cylinder is determined by using particle image velocimetry (PIV) to understand the wake characteristics at different depths of the secondary grooved cylinders. In order to analyze the wake characteristic behind the secondary grooved cylinder with different depths, time-averaged streamlines, time-averaged velocity, RMS velocity, Reynolds stress, turbulent kinetic energy, and instantaneous flow structures are employed. The recirculation zone for secondary grooved cylinders with different depths decreases when compared to the smooth cylinder; the peak magnitudes of flow velocity fluctuation intensity and transverse velocity fluctuation intensity for secondary grooved cylinders with different depths are reduced and the locations appear delayed. Furthermore, in contrast to the smooth cylinder, the secondary grooved cylinders with different depths' Reynolds stress and turbulent kinetic energy are increased by the wake flow, and the transient large-scale vortex is split into several smaller-scale vortices behind the secondary grooved cylinders. The results obtained for the above flow structure are more significant when h/D = 0.05 for the secondary grooved cylinder.Keywords: Wake characteristic, Secondary grooved cylinder, PIV, Recirculation region, Reynolds stress
-
Pages 1074-1088The Counter-Rotating Fan (CRF) offers higher aerodynamic performance, in terms of pressure head and aerodynamic efficiency, compared to the single rotor fan, thus making it an attractive solution for equipment cooling and ventilation of mines and tunnels. Nevertheless, further investigations are required to understand the flow interactions between the front rotor (FR) and the rear rotor (RR), as these interactions are sources of noise emission. This numerical study used the Unsteady Reynolds Average Navier-Stokes (URANS) flow simulations and the Fast Fourier transformation (FFT) to analyse the rotor-rotor interactions and consequences on the aero-acoustic performance. The static pressure fluctuations were recorded at several locations and analysed by FFT to reveal the mechanisms of flow interactions and the effects of axial inter-distance between the two rotors. The inter-distance seems to influence the aerodynamic loading of RR more than that of FR and the total-to-static isentropic efficiency tends to drop. Over one chord distance, the noise level decreases but at the expense of isentropic efficiency. The balanced performance does not seem to improve for an inter-distance greater than 1.5 chords, considered the optimum distance in this study. Finally, a graphical correlation which can be used to estimate the Sound Pressure Level (SPL) is developed for this category of CRF.Keywords: CRF, Aero-acoustic performance, Rotor-rotor interaction, Axial inter-distance, FFT
-
Pages 1089-1098Improving the output flow quality of the high-precision micro bidirectional gear pump can effectively improve the position control accuracy and dynamic characteristics of the electro-hydraulic actuator. In order to meet the appeal requirements and reduce the vibration and noise of the gear pump and prolong its working life, this paper starts with the research of the key part of the gear pump–the unloading groove structure. The three characteristics of trapped oil phenomenon, cavitation phenomenon, and flow were used as key indices to evaluate gear pump performance. Using numerical simulation analysis, the dynamic grid simulation method was used to explore the influence of unloading groove spacing on the transient multi-flow field characteristics of the gear pump under conventional design range. Our results show that reducing the distance between unloading grooves can greatly reduce the trapped oil pressure and the amount of gas precipitation in the flow field, while reducing flow pulsation and improving volumetric efficiency. However, when the unloading groove spacing is too small, the instantaneous flow curve loses the pulsation characteristics and the flow stability decreases. Considering the influence of the gear pump on the accuracy of the electro-hydraulic actuator and the performance of the gear pump itself, the analytic hierarchy process was used to obtain the 1 mm unloading slot spacing, which best meets the engineering requirements of high flow accuracy and low vibration noise. The results provide a basis for work on the structural optimization of high-precision micro gear pumps.Keywords: Bidirectional gear pump, Unloading groove spacing, Numerical simulation, Dynamic mesh, Flow field characteristics