فهرست مطالب
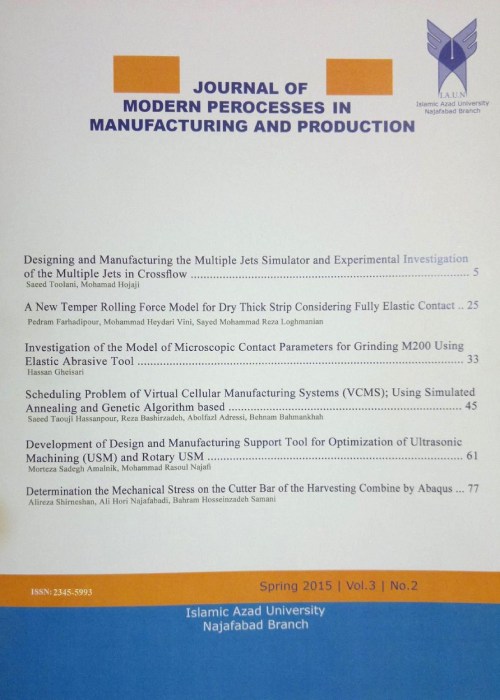
Journal of Modern Processes in Manufacturing and Production
Volume:12 Issue: 1, Winter 2023
- تاریخ انتشار: 1401/12/27
- تعداد عناوین: 6
-
-
Pages 5-16This paper is introduced new method for predicting of fatigue crack propagation (FCP) in residual stress (RS) field due to welding. If there is stress in the material and is subjected to loading, the effects of loading and RS must be considered simultaneously. For this purpose, stress intensity factor (SIF) in liner elastic fracture mechanics (LEFM) approach and J-integral in elastic-plastic fracture mechanics (EPFM) approach are used. The superposition principle based on LEFM is used to consider the RS effects on the cycle ratio and SIF. To achieve more appropriate results based on EPFM, the J-integral is modified to consider the simultaneous effects of RS and external loading. Finally, the FCP equations are modified to consider into calculation the simultaneous influences of RS and cyclic loading. Results from FCP equation based on J-integral are in good agreement with experimental results. The obtained results show that the MLPG method is suitable for calculating the residual stress and the modified J-integral method is the best method for predicting FCP in the RS field caused by welding.Keywords: Residual stress, welding, Stress intensity factor, J-integral, Fatigue Crack Propagation
-
Pages 17-29In any case, macroscale shaping cannot be transferred to microscale due to the size effect. There are different parameters to evaluate small-scale forming. In this article, the effect of flow stress and topography in two states of lubrication and without lubrication for T2 copper micro cylinder has been investigated using the numerical solution and prediction of a trained neural network. An artificial neural network model has been presented to investigate the flow stress and the effect of friction with the miniaturization of the copper microcylinder. The results show that the flow stress decreases with decreasing the initial specimen diameter in both lubrication conditions, and the flow stress decreases by 30 MPa with the initial specimen diameter decreasing from 8 mm to 1 mm. The friction factor increases obviously with decreasing the initial specimen diameter in the case of lubricating with castor oil, and the friction factor increases by 0.11 with the initial specimen diameter decreasing from 8 mm to 1 mm. However, the tribology size effect is not found in the case without lubrication. The reasons for the flow stress and tribology size effects were also discussed. The good matching of outputs and objectives in the regression graphs shows that the response of the neural network is satisfactory.Keywords: Microcylinder, Tribology, Flow stress, FEM, Neural network
-
Pages 31-43The constrained groove pressing process is one of the most effective methods of severe plastic deformation to produce very fine-grained sheet metal. Numerical simulation is performed in several steps by finite element software in such a way that the output result of each step, which is strain-hardened, is used as the input of the next step. The finite element results of the obtained plastic effective strain distribution show that the strain changes along the longitudinal direction of the sample are oscillating. The relevant results also show that in the direction of thickness, the amount of strain in the middle of the sample is maximum and as it moves away from the center of the sample, the amount of strain decreases. In addition, the results of strain heterogeneity show that the strain heterogeneity factor in the longitudinal direction is 2.8 times the corresponding value in the thickness direction whereas the average plastic strain in the two directions differs only about 13.4%. Then, to improve the strain uniformity, steel sheets are placed at the top and bottom of the sample as interface sheets, and then the constrained groove pressing is applied. Using this method, it is observed that the degree of strain homogeneity in the first stage is improved compared to the conventional method of the constrained groove pressing process. By using this method, it can be seen that the amount of strain heterogeneity factor is reduced from 6.85 to 2 in the first stage.Keywords: Severe Plastic Deformation, Constricted Groove Pressing, Copper Sheet, numerical analysis, Strain Distribution Heterogeneity
-
Pages 43-55In this study, the molecular dynamics method is used to simulate the SMAT process in the AZ31 workpiece. Molecular dynamics calculations in LAMMPS software have been used to investigate the effect of size, number, and velocity parameters of carbon steel particles on the mechanical and physical properties of the surface including residual stress, hardness, and surface roughness in AZ31 matrix has been investigated at the atomic scale. The simulation results during the SMAT process show that the residual stress in the AZ31 matrix increases with increasing the diameter of carbon steel particles and the particle velocity in the SMAT process has a significant effect on improving the mechanical properties of the simulated magnesium matrix. The highest residual stress and the largest increase in Vickers hardness in the SMAT process were calculated for the largest colliding particle. The maximum surface temperature of AZ31 decreases after SMAT with the increasing size of carbon steel particles. The results show that the roughness parameter increases with increasing colliding particle size.Keywords: Molecular dynamics simulation, SMAT, AZ31, Mechanical Properties, particle size, Particle Velocity
-
Pages 55-77Connecting parts through welding as permanent connections can play an important role in various industries. Despite the favorable load-bearing capabilities of joints resulting from welding dissimilar parts, they have some limitations that need to be identified and checked to optimize their use. One of the limitations is the behavior of parts under thermal stresses caused by the welding process. Thus, it is important to consider the welding conditions of the dissimilar parts in the contact area of the electrode and the welding seam, as this can significantly affect the mechanical performance of the welds. The research conducted in this study involved using the electric welding method with non-consumable tungsten electrodes under shielding gas (TIG) to connect aluminum and carbon steel parts. Ansys software was utilized to investigate the effect of thermal stress in the welding process for different joints. To ensure accuracy, parts were welded together practically under similar conditions, and the results obtained were compared with the results of the modeled method. First, the behavior of a steel sheet under the butt and Tee Joint and then the role of various factors on welding performance were investigated by modeling the process for a pipe in different conditions. Finally, due to the significant role of T-shaped joints in various industries, heat distribution, behavior, and stress analysis were investigated.Keywords: Welding Process, Dissimilar Joints, Residual stress, Thermal analysis, Finite Element Method
-
Pages 79-92This study aimed to scrutinize the impact of the electrical discharge machining (EDM) parameters of A413 alloy for two cases of dielectric, one with alumina powder and one without, using Taguchi's experiment design method. The completed studies regarding the EDM of the metal-base composites reveal that insufficient research work has been carried out on this composite material. In this research, by using Taguchi's experiment design and through the simultaneous analysis of Total Normalized Quality Loss (TNQL) and Signal-to-Noise ratio (S/N) of the outputs, the impacts of the current intensity, voltage, pulse on-time, and pulse off-time on the material removal rate (MRR), surface roughness (SR), and tool wear rate (TWR) were investigated. The results showed that the use of 3g/L of alumina powder in kerosene dielectric averagely led to a 6.47%, 9.14%, and 19.40% reduction in MRR, SR, and TWR, respectively. Also, the results acquired using TNQL and S/N analyses demonstrated that the optimum experiment was composed of the third level of voltage (A3), the first level of current (B1), the first level of pulse on-time (C1), and the third level of pulse-off time (D3). It was concluded that the current intensity had the greatest impact on the MRR and SR. However, the pulse-on time had the greatest influence on the TWR. It was also observed that the MRR declined by adding 3g/L aluminum oxide powder in the kerosene dielectric which in turn caused a reduction in the SR and the TWR compared to the case of the kerosene dielectric without powder.Keywords: Electrical discharge machining, A413 Aluminum, Alumina Powder, Signal-to-noise ratio, Total Normalized Quality Loss