فهرست مطالب
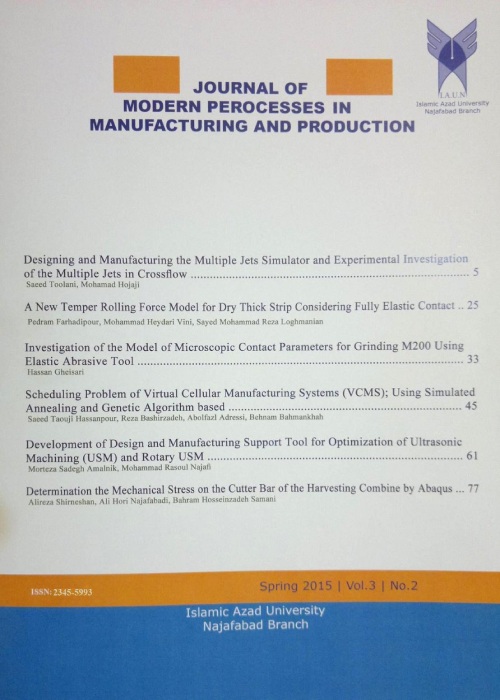
Journal of Modern Processes in Manufacturing and Production
Volume:12 Issue: 4, Autumn 2023
- تاریخ انتشار: 1402/11/21
- تعداد عناوین: 6
-
-
Pages 5-26
Attempts at research across various industries to achieve high-quality surfaces have led to the development of new finishing processes. Magnetic Abrasive Finishing is a novel technique where a magnetic field is employed to control an abrasive tool. Gas turbine compressor blades are among the industrial components requiring high surface quality due to their exposed surfaces. The reduction in surface roughness on these components has a significant impact on the efficiency of motor turbines. This paper focuses on studying the Magnetic Abrasive Finishing process parameters for the free surfaces of Titanium blades. Using a mass Magnetic Abrasive Finishing machine, the influence of powder weight, type of abrasive particles, and gap on the variation of surface roughness is investigated through statistical methods such as the response surface. The fabrication of the machine and determination of magnet polarity are carried out using Maxwell simulation software. The Factorial method is employed for experiment configuration. Mechanically alloyed powders produced by ball mills are used in this study. Results demonstrate that employing the magnetic abrasive method can reduce the surface roughness of the blade by up to 33%. The empirical model derived from regression analysis is utilized to predict the variation in surface roughness. Variance analysis of the experimental results indicates the significance of all studied parameters. Scanning Electron Microscopy (SEM) and Atomic Force Microscopy (AFM) are employed for a qualitative evaluation of the results.
Keywords: Response Surface Method, Magnetic abrasive finishing, Free Form Surfaces, Compressor Blade, Magnetic Flux Density -
Pages 27-38
Friction Stir Welding has significantly transformed the metal joining industry, and an innovative variation known as stationary shoulder FSW has emerged. This study aimed to compare various aspects, including force, temperature, and strain, between conventional friction stir welding (CFSW) and stationary shoulder friction stir welding (SSFSW). To accomplish this, the finite element method was employed, utilizing the lagrangian technique to model the welding process. The findings revealed that in SSFSW, the highest temperature was observed in the vicinity of the rotating pin. This was attributed to the absence of a rotating shoulder in SSFSW, which played a major role in heat generation during welding. Moreover, the longitudinal forces on the tool in SSFSW were significantly higher compared to CFSW, approximately ten times greater. In the CFSW process, the affected area showing strain usually forms a basin-shaped pattern. However, in the SSFSW process, the strain distribution is confined within the range of the tool pin.
Keywords: FSW, SSFSW, Force, Strain, Temperature -
Pages 39-56
In this research, two methods of conventional Friction Stir Welding (FSW) and two-pass friction stir welding have been used to weld AA6061-T6 alloy parts with a copper interlayer (copper foil. Based on the results, it was determined that the number of welding passes, the presence or absence of copper foil as an interlayer, the number of welding passes, the direction of tool rotation and the direction of tool movement in the second pass strongly affect the strength and ductility of FSW. According to the results, the highest tensile strength and ductility belong to TP-D(Two-Pass, type D), TP-B(Two-Pass, type B), TP-C(Two-Pass, type C), TP-A(Two-Pass, type A), CF-Cu and CF(Conventional FSW) samples, respectively. The mentioned samples have growth of 21, 29, 45, 36 and 58% respectively compared to the CF sample. The highest strength growth was related to the TP-D sample, which experienced a 58% increase in tensile strength compared to the CF sample. The tensile strength efficiency of this sample is 89.3% compared to the base metal. The highest increase in ductility was related to the TP-D sample, which experienced a 35% increase in ductility compared to the CF sample. The ductility efficiency of this sample is 81.1% compared to the base metal.
Keywords: Friction stir welding, Double pass welding, Copper interlayer, Aluminum alloy, Weld strength -
Pages 57-70
Metal tubes are widely used in various forms in engineering structures. Local deformation of the tube is required due to design considerations or the tube's location in the machine or structure to facilitate its installation. This paper investigates the process of locally laterally compressing aluminum tubes using experimental and numerical simulation methods. The tube is positioned horizontally on the fixed lower die and is subjected to compressive load by the upper die, which is connected to the movable ram of the press machine, resulting in plastic deformation. Both upper and lower dies are semi-cylindrical with equal radii, and their axes are perpendicular to the tube's axis. For the experimental and numerical analysis, two types of aluminum 6061-T6 tubes with the same outer diameter but different inner diameters were chosen, and three similar samples were created for each type. The true stress behavior, based on the true strain of the aluminum material, was determined from a simple tensile test. Subsequently, the geometric dimensions of the deformed area of the tubes were measured for various press strokes. The geometric shape of the deformation zone and the experimental forming load data were compared with the simulation results obtained using ABAQUS software. A comparison between the results from the two experimental and simulation methods demonstrated good agreement.
Keywords: Tube Lateral Compression, Compression Force, Deformation Zone -
Pages 71-91
In this paper, the nonlinear buckling behavior of two types of functionally graded sandwich beams was studied using a high-order sandwich beam theory. Type I consists of functionally graded layers coating a homogeneous core, while type II features an FG core covered by homogeneous face sheets. All materials are considered temperature dependent, with FGM properties modified through even and uneven porosity distributions modeled by a power law rule. The sandwich beam theory was adjusted to account for nonlinear Lagrange strains, thermal stresses of the face sheets, in-plane strain, and the transverse flexibility of the core. The governing equations were derived from the minimum potential energy principle, and a Galerkin method was employed to solve them for simply supported and clamped boundary conditions. Comparisons with existing literature demonstrate good agreement. The resultes showed that critical load parameter decreases with increasing temperature, power law index, length-to-thickness ratio, thickness, and porosity volume fraction in both distributions, but increases with the wave number. Additionally, the stability of type II sandwich beams surpasses that of type I in high-temperature conditions.
Keywords: Porosity, FGM, Boundary Condition, High-order Sandwich Beam Theory -
Pages 93-113
The correct selection of input parameters in the electric discharge machining (EDM) process leads to improvements in the material removal rate (MRR), dimensional accuracy of the parts, quality of the surface finish, and reduction of tool wear. The main goal of the research was to investigate the type and extent of the influence of input on output parameters in EDM operations. Experimental data and the contribution of parameters were obtained using the Taguchi test design with three levels. The tool used was made of copper. Samples were selected from three types of alloy steel: 4340, Ti6Al-4V, and AISI D2 steel. The test variables included maximum current (Ip), gap voltage (Vg), and duty factor (DF). In these experiments, Ip values of 5, 10, and 15 amps, Vg values of 25, 50, and 75 volts, and DF values of 0.3, 0.6, and 0.9 were selected. The number of machining operations was 81 tests, and the L9 orthogonal array related to the Taguchi approach used for Design of Experiments (DOE) reduced the number of machining operations from 81 to 27 tests. The results indicated that the current parameter of 5 amps had the highest effect on surface roughness (SR) in samples of AISI4340 steel. The current of 15 amps had the greatest impact on MRR, while the duty factor (DF) of 0.6 played the highest role in electrode wear rate (EWR). Maximum Ip contributed 36.77%, Vg contributed 31.03%, and DF contributed 32.18% to EWR.
Keywords: EDM, Surface Roughness, MRR, EWR, Taguchi Method