فهرست مطالب
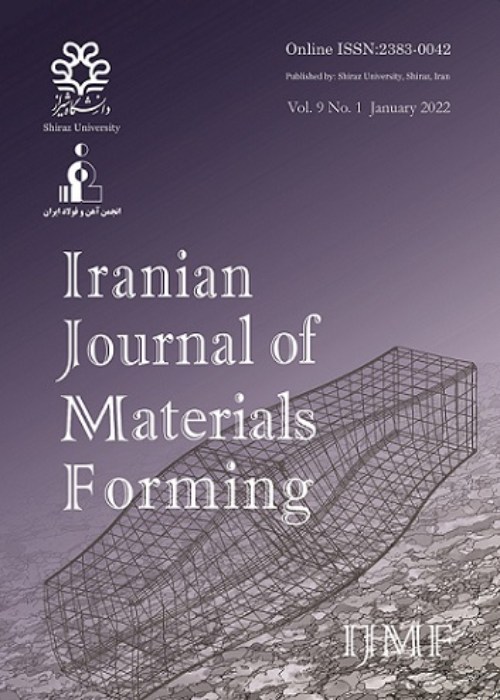
Iranian Journal of Materials Forming
Volume:10 Issue: 1, Winter 2023
- تاریخ انتشار: 1402/03/28
- تعداد عناوین: 7
-
-
Pages 2-3
The “Iranian Journal of Materials Forming (IJMF)” turned ten years old and the first issue of the 10th volume was published. This is an international open access journal in the fields of materials deformation and forming processes, which was established at Shiraz University in 2014. The journal is pleased to receive papers from scientists and engineers from academic and industrial areas related to all manufacturing processes. In addition, all deformations, including the elastic and plastic behaviors of materials and deformations due to failure, are part of this journal’s field of interest. The quality and credibility of the journal have been ensured by appointing some of the most well-known professors in the world as members of its editorial board. In addition, the wide range of the selected referees in this issue is a sign of its scientific quality. It is a matter of pride that for the third year this journal has been successfully released quarterly and the first issue of the year was published in 2023. Unfortunately, the rate of receiving high quality articles has decreased due to rising the rejection rate. In order to publish on time and maintain quality, we need the cooperation of more experts in this specialized field.
Keywords: deformation, Failure, Mechanical properties -
Pages 4-12Copper foams with open cells are suitable for use in battery electrodes, catalysts, filters, sound insulation, heat and catalytic exchangers due to the unique combination of properties such as high thermal and electrical conductivity and very low density. In the current research, copper foam containing open cells are produced using polyurethane polymer substrate with the help of electroless-electrochemical deposition, combined methods. The effect of various parameters, including the current intensity of the electro-deposition process, the presence of sulfuric acid and various additives in the electrochemical plating solution, on the microstructure of produced open-cell copper foam is investigated. The purity and microstructure of the fabricated foam are analyzed by X-ray diffraction (XRD) and scanning electron microscope (SEM). Mechanical strength of the foams are evealuted with a compression test. The results show that the current intensity in the range of 0.1-0.2 A is suitable for creating a uniform deposit. Moreover, it has been shown that, copper open cell foam with a uniform microstructure can be created by applying 0.1 A current, plating duration of 48 h and with plating solution including; aqueous copper sulfate 65 g/L, sulfuric acid 30 ml/L, phosphoric acid 2 ml/L, dextrin 20 mg/L, thiourea 20 mg/L, potassium chloride 2 g/L and sodium sulfate 25 g/L. Compression test results show that the compressive strength of the foam is about 0.82 MPa, the plateau stress is 0.52 MPa, and the absorption energy is about 0.5 MJ/m3.Keywords: Copper open cell foam, Electroless deposition, Electrochemical deposition, Microstructure, Mechanical strength
-
Pages 13-25The present research work is related to the optimal experiment selection of the bimetallic sheet hydroforming process using multi-attribute decision making (MADM) techniques. The numerical simulation of the operation has been done by applying the ABAQUS software. The studied geometrical variables include the punch tip radius (Rp), the die entrance radius (Rd) and the clearance between the punch and matrix (CL), and the target parameters are the maximum thickness reduction and thickness variation of the final product. In order to calculate the weight of the objective function in sheet hydroforming process, criteria importance through inter-criteria correlation (CRITIC) and method based on the removal effects of criteria (MEREC) techniques were employed. In the following research, a technique for order preference by similarity to ideal solution (TOPSIS) has been used to evaluate the numerical test and assess the best case. The results demonstrated that the weighting coefficients of the two objective functions, namely thickness reduction and thickness variation obtained from CRITIC and MEREC methods, was almost the same. Their values were calculated at approximately 0.6 and 0.4, respectively. Based on the optimization outcomes, the optimal values of Rd, Rp, and CL gained were 6 mm, 4 mm, and 2.2 mm, respectively.Keywords: Sheet hydroforming process, MADM, CRITIC, MEREC, TOPSIS
-
Pages 26-38A rolled sheet of aluminum 1100 was processed by two ECAE dies with inner corner angles of 90° and 135°. The samples were processed using route A up to 4 and 10 passes in ECAE 90° and 135°, respectively. The mechanical behaviors of initial and processed materials were evaluated by nano-indentation and compression tests carried out at three different orthogonal directions, at room temperature. Crystallographic texture evolution during two different ECAE processes has been also studied. A considerable reduction in mechanical anisotropy is displayed for processed materials compared to the initial material by nano-indentation tests. Though there is appreciable progress in mechanical isotropy for processed materials by 135° ECAE, compared to the 90° case. Studying crystallographic texture evolutions reveals that ECAE 135° is more capable than ECAE 90° in the development of cube components; however, the rate of texture evolution is slower in ECAE 135°. Dissimilar prominent texture components are also developed by two different ECAE processes.Keywords: Anisotropy, ECAE, Nano-indentation test, texture evolution, Aluminum 1100
-
Pages 39-52Incremental forming is one of the new forming methods. Single-point incremental forming (SPIF) has shown significant potential for forming complex metal parts. In the single-point incremental forming, a spherical tool head moves along a pre-defined path to form the desired geometry. The aim of this study is to optimize the fracture depth and forming forces of the three-layer metal-polymer sheet by using the single-point incremental forming process. By using response surface methodology (RSM), a series of experiments were designed in which tool diameter, step down and spindle speed were considered as process input parameters. The influencing parameters in fracture depth and forming forces have been identified by using statistical tools (response table, main effect diagram and ANOVA). Analysis of variance was used to show potential differences between the means of variables by testing the population value in each sample, which enables it to show the effects of input variables on output variables. The results show that the forming forces increased and the formability decreased by increasing the step down and the tool diameter. The highest forming force is 1476 N and the lowest value is 1045 N. Similarly, the highest fracture depth is 8.8 mm and the lowest is 7.1 mm. The best conditions are achieved when spindle speed is 2340.9 rpm, tool diameter is 7.51978 mm, and vertical step is 0.329552 mm. In this condition, the fracture depth is 8.50552 mm and the forming force is 776.03 N.Keywords: Incremental sheet forming, Metal–polymer three‑layer sheet fracture depth, ANOVA, Forming Force, Fracture depth
-
Pages 53-60In the present study, a visco-plastic self-consistent model (VPSC) was used to predict the Al0.3CoCrFeNi texture after cold rolling. The alloy under examination was produced via vacuum arc remelting and casting (VAR casting). Then, it was remelted four times to have the best structure homogeneity. However, the produced ingot was then homogenized at 1050°C for 10 h to remove the residual stress and reduce the micro-macro-segregation. This was followed by 75% cold reduction which was employed in seven passes. In order to simulate the Al0.3CoCrFeNi texture via the VPSC model, affine schemes and hardening parameters were used in this model. Moreover, this model was performed by Fortran 77 programming languages, and grain fragmentation and co-rotational effect were used in this code. In this study, a simulation process was used for 300 and 1000 grains. After that, simulation results were compared with experimental textures that were measured by the X-ray diffraction method. The results showed that both experimental and simulated textures have an acceptable compatibility. However, there are differences between the measured and simulated results, which can be attributed to the number of grains of estimated and simulated cases.Keywords: crystal plasticity, Cold rolling, High entropy alloys, Texture
-
Pages 61-69In the present work, the selective laser melting (SLM) has been chosen as a controlled thermomechanical processing route in which the required temperature and strain for the occurrence of dynamic recrystallization is provided. The 316L stainless steel as representative material was constructed by SLM under specified parameters (laser power, layer thickness, hatch spacing, scan strategy, and scan speed). The printed material’s microstructure was carefully analyzed through electron back scattered diffraction. The presence of considerable fine grains (< 20 μm) through the printed microstructure was considered as evidence for the occurrence of dynamic recrystallization during the manufacturing process. The high fraction of sub-boundaries (~79.7%) and sub-grains indicted the capability of the material for substructure development in the course of additive manufacturing process, and the fact that the new fine grains were formed through continuous dynamic recrystallization mechanism. The creation of plastic strains through the parts structure during SLM, which was required for dynamic recrystallization, was discussed relying on the expansion and contraction of the layers during repeated heating and cooling cycles. The amount of plastic microstrain was estimated to be around ~0.56 considering the layer thickness and depth of the melt pool. The hot compression tests were conducted at 1000℃ and various strain rates of 0.001, 0.01 and 0.1 s-1 and the corresponding critical strains of dynamic recrystallization (~0.2) were calculated, which was well lower than those created during additive manufacturing process.Keywords: Stainless steel, Selective laser melting (SLM), Cellular structure, recrystallization, Recovery