فهرست مطالب
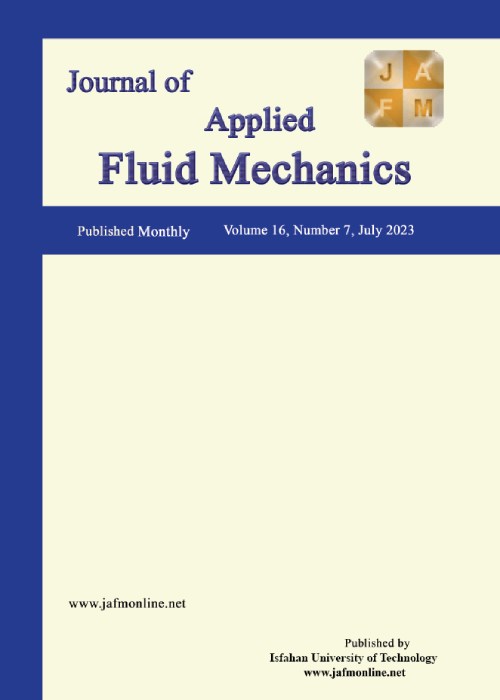
Journal Of Applied Fluid Mechanics
Volume:17 Issue: 2, Feb 2024
- تاریخ انتشار: 1402/09/13
- تعداد عناوین: 15
-
-
Pages 297-309In this paper, numerical simulation methods are adopted to explore the influencing factors of a Ceramic Catalytic Turbine (CCT) for reduced exhaust pollution from vehicles during the warm-up stage. Also, an analysis is conducted regarding the potential effects of turbulence on the catalytic reaction mechanism and the sensitivity of relevant parameters to the Arrhenius equation. It is found out that the air-fuel ratio inside the engine has a considerable effect on the reactions of CCT, with the conversion efficiency of each emission species sharply reduced under fuel-rich conditions. At 600K, the conversion efficiency declines by 11.3% for C3H6, 12.26% for CO, and 3.64% for NO. At 700K, the conversion efficiency is reduced by 6.7% for C3H6, 11.56% for CO, and 6.44% for NO. Despite increasing the concentration of reaction gas components, a high flow rate makes little difference to the reaction itself. At the same rotational speed of the turbine, the conversion rate of harmful components drops with an increase in flow rate due to the increase in space velocity. When the flow rate is constant and the temperature is kept in the control zone of chemical kinetics, the conversion efficiency of the catalytic reaction is enhanced at a higher rotational speed. Differently, when the temperature is in the control zone of mass transport and the flow rate is constant, the conversion efficiency decreases as the turbine accelerates. In practical terms, reducing activation energy within a controllable range is equivalent to further reducing the light-off temperature of the catalyst. Meanwhile, this may disrupt the convergence of numerical calculations because the catalytic reactions could occur at around the light-off temperature.Keywords: Vehicle warm-up, Emission reduction, Catalytic reaction, Turbine, Numerical simulation, Mechanism
-
Pages 310-321The phenomenon of droplets impacting droplets is common in many fields including the chemical, nuclear, and aerospace industries. In this paper, high-speed photography technology is used to obtain the variation law and evolution properties exhibited by droplets colliding with sessile droplets of varying sizes. We further explored how the Weber number (We) and volume ratio (Vp/Vi) influence the behavior of droplets colliding with sessile droplets. The phenomenon of droplets impacting sessile droplets of different volumes is different from that of droplets impacting liquid films. In terms of droplet spreading, compression and the non-splashing liquid crown, the phenomena and laws reported in the present study are applicable for 1 ≤ We ≤ 165 and droplet volume ratios of 1 ≤ Vp/Vi ≤ 6. With a low Weber number, the droplet compresses and deforms downward without coalescence at the initial stage of collision. A high Weber number results in a no-splashing liquid crown. These findings provide important insights into the dynamics of droplet-droplet interactions.Keywords: Droplet impact, Sessile droplet, Volume ratio, No-splashing liquid crown, Droplet compress
-
Pages 322-336
An analysis of the minimum pressure coefficient on the suction side of the axial-flow pump blades is presented as a design criterion. A Matlab code is used to improve the computer aided design process efficiency and quality. X-Foil software determines the blade profiles' lift and drag coefficients, and a computational fluid dynamics model is applied to certify the pump efficiency. The model is validated from the available experimental data in the literature. The finite volume method is used through the commercial software Ansys CFX, in order to solve the model equations. A case study is presented to design the axial-flow pump for a large circulating water channel that will be used to test ships, naval structures, and hydrokinetic turbines. Particular attention is given to the pump cavitation conditions. The model evaluates the minimum pressure coefficient criterion and pressure coefficient distribution on the blade span, showing satisfactory performance for the pump at the design point and at variable speed.
Keywords: Turbomachinery, CFD, Performance optimization, CFX, Finite volume method -
Pages 337-351To improve the aerodynamic characteristics of compressor blades, a novel asymmetric leading edge (ASYLE) has been introduced and shown to offer superior performance. However, the aerodynamic robustness of such specially designed leading edge (LE) remains unclear due to the considerable uncertainty problems it presents. This paper investigates the robustness of ASYLE blade under both geometric and operational uncertainties. Profile deviations within ±0.05mm were introduced to investigate the influence of manufacturing errors. In addition, the perturbated inflow angles between ±0.375° were considered for uncertain inflow conditions. The statistic aerodynamic performance as well as operating dispersibilities at Ma=0.7 were obtained by the non-intrusive polynomial chaos (NIPC) method. The results show that considering uncertain profile errors, the operating range of ASYLE blade is 2.3° wider than original leading edge (ORILE) blade and the dispersion of total pressure loss can be reduced by 53.1% at β1=45.8°. Regarding uncertain inflow angle variations, the total pressure loss dispersion of ASYLE blade can be reduced by 93.8% at β1=50.8°. The ASYLE shows better overall aerodynamic robustness than ORILE upon considering uncertainty limits. The influence propagations in the flow fields of both uncertainties were further analysed, which revealed that the variations of separation bubble structure near LE are the direct cause to the aerodynamic uncertainties. The ASYLE design effectively controls the size and variation of LE separation bubble and thus demonstrates better aerodynamic robustness.Keywords: Asymmetric leading edge, Aerodynamic robustness, Profile error, Inflow angle perturbation, Uncertainty quantification
-
Pages 352-369This research pioneers the application of thermographic principles to diagnose faults, specifically cavitation and air entrainment, in centrifugal pumps. The study represents the inaugural investigation into the feasibility of leveraging infrared thermography for this purpose, underpinned by rigorous experimental methodologies to validate its efficacy. By capturing thermal images of pumps operating under varying conditions, a pseudo-coloring technique for precise temperature range segmentation was employed. This technique facilitated the assessment of fault severity, quantified through the computation of the . This index emerged as a quantifiable metric of fault severity, with elevated values correlating to more pronounced degrees of fault occurrence. Notably, in the case of air entrainment faults, a maximum temperature escalation of 3.9°C was recorded after 60 min run time, and the corresponding thermal index was found to be 5.12. The investigation employs the HSV model, extracting regions of thermal variation through hue differences for fault detection. This process is combined with edge detection methods like Sobel, Prewitt, Roberts, Canny, and Otsu. The Otsu technique consistently outperformed alternative approaches. Specifically, for high cavitation and air entrainment faults, the Otsu method had the highest mean of 0.1730 and 0.1253, respectively. Key findings include the effectiveness of image processing techniques, statistical measures, and edge detection methods for fault diagnosis, as well as insights into temperature differentials and motor load reductions with increasing fault severity. The research improves maintenance, enhancing efficiency and reducing downtime. It emphasizes infrared thermography's potential for fault diagnosis while identifying constraints and advocating further research.Keywords: Condition monitoring, Rotating machinery, Fault diagnosis, Image processing, Thermal imaging
-
Pages 370-383Flow-acoustic feedback is one of the main types of noise in a cavity, is caused by the instability of the cavity shear layer and is enhanced through an acoustic-wave feedback mechanism. The flow characteristics of the cavity boundary/shear layer and the characteristic frequencies of the flow-acoustic feedback in the cavities are studied numerically, with aspect ratios ranging from 1/2 to 4/3. The freestream Mach number is equal to 0.11, corresponding to an Re-based cavity length of 2.1×105. Improved Delayed Detached Eddy Simulations combined with Ffowcs Williams-Hawkings acoustic analogy are used to simulate the flow and noise characteristics of the cavities. Auto-correlation analysis of flow field fluctuations is used to establish a link between the boundary/shear layer pressure fluctuations and flow-acoustic feedback noise. For the low aspect ratio cavities investigated in this paper, convection velocities along the shear layer development direction are obtained using wavenumber-frequency analysis. The deeper the cavity, the lower the shear layer flow velocity. Correspondingly, the characteristic frequencies of the narrowband noise generated by the flow-acoustic feedback shift linearly toward the low frequency band as the cavity depth increases. The results of the predicted noise characteristic frequencies obtained using wavenumber-frequency analysis and Rossiter's empirical formula are in agreement with the calculated results.Keywords: Cavity noise, Flow-acoustic feedback, Wavenumber-frequency analysis, Pressure fluctuation, Flow instability
-
Pages 384-397In the field of hydrogen safety and combustion, the effect of obstacles on hydrogen deflagration is a topic of general interest to scholars. In previous studies, scholars usually used uniform obstacles under various operating conditions and obtained conclusions by changing their number and positions. However, in practice, the shapes of obstacles at an accident site are often not the same and regular. In this paper, a series of obstacles with variations in length were investigated, and the effects of the obstacles on hydrogen deflagration under different working conditions were analyzed. The configuration of the obstacles with gradually increasing lengths amplified the vortices in the flow field so that the propagation direction of the flame front surface was reversed after passing three obstacles. The variations in the lengths of the obstacles had a significant stretching effect on the propagation of the flame and a considerable acceleration effect on the propagation speed of the flame. The main reason for the acceleration was the rapid propagation of the flame achieved by the vortex when rupture occurred. The change in the pressure gradient that occurred at the center of rotation caused rapid movement of the combustion gases, which ultimately led to an increase in the flame propagation speed. A configuration with gradually increasing lengths of the obstacles promoted the overpressure. A configuration with gradually decreasing lengths of the obstacles suppressed the overpressure. The reason for the formation of the local high-pressure area was that unburned gas was accumulated there by pressure waves and the obstacle walls, and then the thermal expansion formed a high pressure. The Rayleigh–Taylor and Kelvin–Helmholtz instabilities caused the overpressure to rise further. The results can provide a theoretical basis for hydrogen transportation, storage, and safety.Keywords: Explosion, combustion, Flame, Gradient, obstacle, Vortex
-
Pages 398-409A vital process for converting heavy petroleum productions is Fluid Catalytic Cracking (FCC). As a major source of CO2 emissions, the regenerator reactor in the FCC unit accounts for about 20-35% of the refinery's total emissions. A common method for reducing CO2 emissions from the FCC regenerator is oxy-combustion, which has different advantages with regard to reducing energy penalties and associated costs. In this study, a computational fluid dynamic (CFD) study was used to examine the hydrodynamic characteristics of solid particles and gas inside the FCC regenerator, allowing CO2 to be captured more efficiently. Utilizing Ansys Fluent platform, the Eulerian-Eulerian model was applied with granular flow kinetic theory. In the simulations, different mesh sizes were tested, and the hydrodynamics of the oxy-combustion regenerator were evaluated by adjusting CO2 flow rates to achieve similar fluidization behaviors. The CFD results indicated that the conventional drag model accurately predicted the density phases within the bed. In oxy-combustion, CO2, due to its density, naturally creates a smaller dense phase compared to air-combustion. Moreover, optimizing the fluidizing gas velocities resulted in enhanced particle mixing, resulting in a distributed flow with vortices within the dense phases due to a reduction in gas velocity. To improve the environmental performance of the FCC unit, this research provides valuable insight into the hydrodynamics of solid catalysts used in the oxy-combustion process.Keywords: Oxy-combustion, Computational fluid Dynamic, Hydrodynamic, Multiphase flow, Regenerator
-
Pages 410-423Intake system structure design is categorized under gas turbine marine technology, and its performance affects the inlet flow field of the compressor, thereby impacting the overall operation stability of the gas turbine. Therefore, this study analyses the structural characteristics of various types of intake systems and establishes a computational domain model. Numerical simulation methods are used to systematically study the internal and external flow fields of the intake system. By varying the structure of the intake system, we compare and study the distribution form of the flow field inside and outside the intake system, velocity and total pressure distribution of the compressor inlet section, and flow loss inside the intake system. The speed and total pressure distortion of the compressor inlet section are analysed quantitatively. It was concluded that inlet distortion causes the leakage flow from some channels to spill into adjacent blade channels at the leading edge of the higher span, resulting in an early compressor stall. Specifically, the compressor stall and working flow margins are reduced by 2.51% and 2.76%, respectively.Keywords: Ship intake structure, Inlet distortion, Structural modification, Axial compressor, Compressor performance
-
Pages 424-441In the routine maintenance of each main pump in the oil transmission station plant, abnormal erosion wear was found at the flushing port of the mechanical seal of Sulzer pump casing. For the sake of stable and safe unit operation, this study explored the mechanism and process of erosion formation in the pump casing at the microscopic level using SEM (scanning electron microscope) and EDS (energy dispersive spectrometer) techniques. And ANSYS Fluent was used to numerically simulate the unconventional turbulent flow in the special location of Sulzer pump to obtain its flow field characteristics. The trajectory tracking of solid phase particles based on Finnie erosion model was also carried out to obtain the influence law of different particle sizes on the wear degree of each area of the pump casing, and to point out the influence of the motion behavior of particles at the flushing port position on the erosion. The results show that there is unconventional turbulence in the flushing port of the Sulzer pump mechanical seal, and the solid particles are affected by turbulent diffusion and fluid adhesion, and some particles deviate from the velocity direction and continuously impact the surface of the pump casing, which is the direct cause of the erosion wear here. By optimizing the location of the flushing port, severe erosion wear at the flushing port can be avoided. This study can provide guidance and recommendations for the production, operational stability and wear protection of Sulzer pumps.Keywords: Erosion, Centrifugal pump, Eds, Sem, Failure Mechanism
-
Pages 442-460The aim of this study is to evaluate the aerodynamic efficiency of a Savonius vertical-axis wind turbine. The approach used relies on resolving the Unsteady Reynolds Averaged Navier-Stokes equations (URANS), the turbulence being modeled by the k-ω SST model. The flow around the wind turbine is simulated using the arbitrary sliding interfaces technique. First, the study investigates the impact of blade shape on wind turbine efficiency by examining seven Savonius rotors constructed with distinct blade configurations. The results indicate that the highest aerodynamic performance is provided by the rotor with the elliptical blades, with a notable increase in the power coefficient of about 80% in comparison to the classic semi-circular profile. To further enhance the efficiency of the Savonius wind turbine, a twin-rotor configuration using the elliptical blades was studied. The results indicate a further enhancement in the power coefficient, reaching 110% compared to a single rotor with semicircular blades.Keywords: Vertical axis wind turbine, Savonius, Blade shape, twin-rotor, URANS, SST k-ω Model
-
Pages 461-473The hydrodynamic coefficients of underwater manipulators constantly change during their operation. In this study, the hydrodynamic coefficients of an underwater manipulator were calculated using the finite volume method to better explain its hydrodynamic performance. The drag, lift, and moment coefficients and the Strouhal number of an underwater manipulator for different postures were investigated. The results indicated that in each motion range, the coefficients first increase and then decrease. Meanwhile, when the attitude of the underwater manipulator is axis-symmetric or origin-symmetric, the hydrodynamic coefficients and the Strouhal number obtained are approximately the identical. The drag coefficient, lift coefficient and moment coefficient reach their maximum values of 3.59, 3.29, and 1.78 at angles of 30°, 150°, and 150°, respectively, with minimum values at 90°, 50° and -30°. Furthermore, the leading-edge shape of the underwater manipulator had a significant effect on the hydrodynamic coefficient. Maximum reductions of 44%, 25%, and 50.5% were obtained in the drag, lift, and moment coefficients, respectively, by comparing the semicircular leading edge with the right-angle leading edge. A maximum Strouhal number of 0.219 was obtained when the semicircular leading edge of the underwater manipulator was the upstream surface. This study will provide theoretical guidance to reveal the hydrodynamic performance of the underwater manipulators. It also serves as a reference for the structural design of the underwater manipulators.Keywords: Underwater manipulator, Drag Coefficients, Lift coefficients, Moment coefficients, Strouhal number, Leading-edge shape
-
Pages 474-486The impact of the column number of ellipsoidal dimples on a highly-loaded compressor cascade (NACA65-K48) under design conditions was investigated by using a numerical simulation method. Ellipsoidal dimples with a thickness of 0.2 mm were located at the position of chord length ranging from 10% to 36%. The span-wise interval was 5.0 mm. The performance and flow field structures of cascades with 1 to 5 ellipsoidal dimpled columns were compared, and the results showed that the turbulent kinetic energy intensity near the wall was enhanced and the fluid separation resistance was consequently improved. The total pressure loss was reduced by all modified ellipsoidal dimples. In addition, the separation bubble of the suction side was broken or weakened, the corner separation was improved, and the influence range of the passage vortex was reduced. Moreover, the improvement effect of cascade performance parameters initially increased with the increase in the number of dimple columns and then reduced as the number of columns was further increased. The reductions in the total pressure loss of the cascade were 0.59%, 1.47%, 1.69%, 1.91%, and 1.73% for column numbers 1 to 5, respectively.Keywords: Highly-loaded compressor cascade, Ellipsoidal dimple, Flow loss, Transition, Corner separation
-
Pages 487-496The vibration of water injection pipeline systems in oilfields creates challenges in terms of safe long-term operation. To fully understand the vibration mechanism of plunger-powered high-pressure water injection pipelines, we conducted fluid pressure pulsation calculations and fluid structure coupling modal evaluations using finite element analysis software to study the effects of pressure, pipe length, and pipe clamp on the vibrations. The results indicate that the total displacement increases with increasing pressure, although the magnitude of the increment gradually decreases. The pipe length has a significant impact on the natural frequency. Based on the findings of the present study, we proposed that pipe clamps could be introduced to reduce the vibrations in an existing high-pressure plunger pump water injection pipeline, and the overall design was optimized. Comparative modal analysis revealed the most practical number and position of the pipe clamps to be suitable for a pressure range of 42–70 MPa.Keywords: High-pressure water injection pipeline, Pipeline vibration, Modal analysis, Pipe clamp, Vibration reduction optimization
-
Pages 497-518How the high-rise (HR) building affects the pedestrian-level wind environment (PLWE) is of great significance to urban planning. Therefore, the effects of the HR building on the wind and the thermal environments in the urban array with different planar densities are studied numerically. The planar densities are 0.25, 0.4 and 0.6. The simulation results reveal that the HR building can strongly affect the flow dynamics and the heat transfer mechanisms in the urban array. Compared with the low-rise (LR) buildings, the presence of the HR building in the surrounding buildings creates high-speed downwash airflow in the upstream street, and the velocity of downwash airflow increases with the increase of planar density. The turbulent kinetic energy at pedestrian level around the HR building increases. When the planar density is large, the direction of the wake airflow behind the HR building is alternating. And long periods of high-speed airflow are observed, which do not occur in the wake of the target LR building. The temperature around the HR building is lower than that around the target LR building. The surface heat flux around the HR building is greater than that around the target LR building. The surface heat flux around the HR building increases with the increase of the planar density, which is contrary to that around the target LR building.Keywords: Numerical simulation, Wind, Thermal environment, High-rise building, Urban array, Planar density