فهرست مطالب
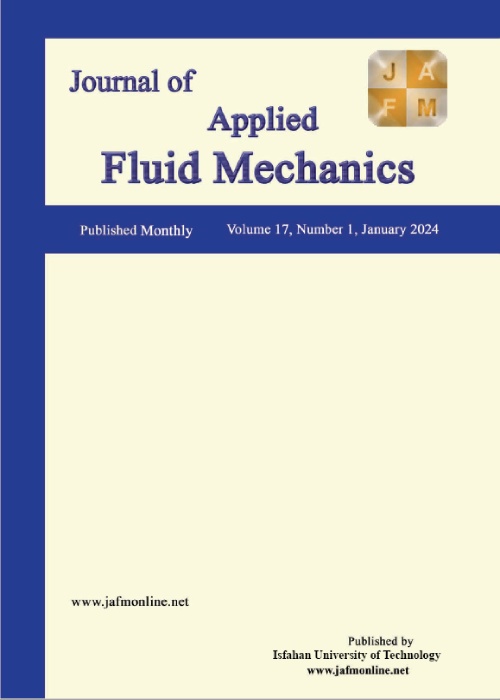
Journal Of Applied Fluid Mechanics
Volume:17 Issue: 3, Mar 2024
- تاریخ انتشار: 1402/10/14
- تعداد عناوین: 15
-
-
Pages 519-533Nowadays, axial fans participate in the most important areas of industry and research, including aviation, navy, wind tunnels, cooling towers, and even automobiles. Thus, more emphasis has been placed on improving their aerodynamic performances. It is important to notice that the parameters involved in designing a fan are mainly concerned with aeraulic power, torque and efficiency. This study investigates the utilization of flow control techniques to improve performances of an axial fan equipped with hollow blades, shroud, and hub. These features grant the fan crucial characteristics, namely, its lightweight and facilitate the blowing action by taking advantage on its hollow parts. The fan's performance is evaluated using a steady RANS numerical model with a k-ω SST turbulence closure, which was validated with experimental data. An active control air blowing through a slot was introduced with various positions and dimensions. The results demonstrate a significant improvement in the fan's performance, with an up to 56% increase in aeraulic power gain, accompanied by changes in the overall flow topology, noticed by closely analyzing the flow structure near the tip clearance.Keywords: active control, Axial Fan, Hollow blade, Hollow shroud ring, Leakage flow, Slot
-
Pages 534-547The return-channel of a preceding stage in a multi-stage centrifugal compressor has a significant effect on the aerodynamic performance of the current and subsequent stages. However, due to the relatively complex nature of the return-channel configuration with many geometric parameters, no general design guidance is available in the literature. In this study, numerical methods are used to study the effects of different geometric parameters of a return-channel on the performance of a high-flow-coefficient centrifugal compressor. A multi-objective genetic algorithm is applied to optimize the return-channel. The effects of different geometric parameters on the performance are then studied using a sensitivity analysis method. Calculation results show that the residual vortex intensity at the outlet of the return-channel is affected by the geometric angles of the inlet and outlet of the return-channel blades. The flow uniformity at the stage outlet is primarily affected by the geometric angle of the blade outlet and the number of blades. The overall performance of the compressor stage is primarily affected by the geometric angle of the blade inlet and the lateral inclination angle of the cover plate. Calculation results for a two-stage compressor consisting of the optimized first stage and its following stage show that the outlet flow field of the first stage is more uniform than the original first stage. Additionally, at the design operating condition, the polytropic efficiency and pressure ratio of the entire unit increase by 1.07% and 4.07%, respectively. The polytropic efficiency and pressure ratio for the second stage increase by 2.34% and 3.51%, respectively. The impeller head coefficient increases by 7.33%. The theoretical analysis shows that for high-flow-coefficient centrifugal compressors, reducing the residual vortex intensity of the outlet flow field of the return-channel in a stage can significantly improve the off-design performance of the following stage.Keywords: Return-channel, High flow coefficient, Geometric parameters, Sensitivity Analysis, Residual vortex intensity, Multi-objective optimization
-
Pages 548-558The aim of the present research work is to understand the intricacies of fluid flow through a rectangular channel that has been partially filled with a metal foam block of different blockage ratio (0.16-1), with a pore density (5–30 Pores Per Inch i.e. PPI), along with varying inlet velocity (6.5–12.5 m/s). For the porous region, numerical solutions are acquired using the Darcy Extended Forchheimer model. The Navier-Stokes equation is used in the non-porous zone. Different flow behaviours were seen as a function of PPI, height, and inlet velocity. The pressure drop increases with inlet velocity, PPI, and block height, with a maximum value of approximately 4.5 kPa for the case of 30 PPI, 12.5 m/s, and a blockage ratio of 1. Results show that the existence and location of the formation of eddies depends on the inlet velocity, PPI, and blockage ratio. Such studies have been reported less and will aid research on forced convection through a channel partially filled with metal foam and optimisation studies between increased heat transmission and the additional pressure drop for the same by providing a detailed fluid flow analysis.Keywords: Darcy Forchheimer, Metal foam, Pressure drop, Eddies, Partially filled channel, PPI
-
Pages 559-570To address the issue of erosion in the control valves of blackwater flash systems in the coal chemical industry, this study investigates the dynamic erosion characteristics of one such control valve. Computational fluid dynamics is employed to compare the results obtained with a static mesh and an erosion-coupled dynamic mesh, and the valve erosion is investigated by analyzing the erosion rate, the particle impact velocity, trajectories and angle. Moreover, the relationship between the deformation caused by erosion and the dispersion of the flash vapor phase in the valve is studied, focusing on the flow resistance coefficient. The results indicate that over a period of 9 × 106 s, the impact velocity and subsequent collisions of particles reduce, and the impact angle decreases with the accumulated deformation of the valve core. Notably, the valve core is influenced primarily by the cutting that results from low impact angles, leading to a substantial decrease in the overall erosion rate of the valve, amounting to a reduction of 56.4%. The region facing the flow is at significant risk of erosion, and as the opening decreases, the erosion zone extends gradually to the annular region of the valve core and valve head, leading to increased erosion deformation. Furthermore, as the flow resistance coefficient decreases, so does the vapor volume fraction inside the valve. This study provides a theoretical basis for predicting faults and developing online monitoring solutions for high-differential-pressure control valves in blackwater flashing systems.Keywords: Computational fluid dynamics, Control valve, Erosion, Erosion-coupled dynamic mesh, Flashing
-
Pages 571-590Effective deduction of air heating load and drag is a critical issue in hypersonic vehicle engineering applications. In this research, seven various geometrical models have been proposed to study and compare the effect of each configuration on the flow field, drag, and aerodynamic heating deduction under the same flow conditions. The presented configurations in this study: (a) blunt-body geometry as a reference of comparison, (b) blunt-body geometry with a spike, (c) blunt-body geometry with an counter flow jet, (d) blunt-body geometry with a spike and counter flow jet, (e) blunt-body geometry with a spike and aerodisk, (f) blunt-body geometry with a spike, aerodisk, and root counter flow jet, (g) blunt-body geometry with a spike, four aerodisks and root counter flow jet. The Reynolds-Averaged equations have been solved using the Finite Volume Method (FVM) along with the shear stress turbulence model (k-ω SST). The flow is assumed compressible, steady-state, and axisymmetric with a free stream Mach number of 6. According to the study of each configuration’s performance related to the parameters of drag, maximum pressure, and maximum heat flux factors on the blunt-body walls, (g) configuration with a drag factor of 0.2699, maximum pressure factor of 209.8, and maximum heat flux factor of 25.1, has the most deduction on the blunt-body walls among the seven configurations. The deduction percentage of drag, maximum pressure, and maximum heat flux factors of (g) configuration to (a) configuration are %72.1, %94.5, and %79.9, respectively, which significantly diminished drag and heat flux. Also, the best configuration scenarios for drag and aerodynamic heating deduction are geometrical models of g, f, d, e, c, b, and a, respectively.Keywords: Heat deduction, Drag deduction, Hybrid method, Blunt nose, Spike
-
Pages 591-603Cavitation-induced vibration presents a significant challenge in vortex pumps, leading to potential damage to hydraulic components and adverse effects on pump performance. This study aims to investigate the long-term implications of such phenomena. To capture the vibration signals caused by cavitation, we utilized vibration acceleration sensors on the vortex pump and collected data at five predetermined measuring points under three different operating conditions. The analysis used two prominent techniques, fast Fourier transform (FFT) and adaptive optimal kernel time-frequency representation (AOK-TFR), to explore the frequency-domain and time-frequency characteristics of the vibration signals. The findings reveal a notable increase in frequency amplitude at each monitoring point as the flow rate rises. Under cavitation conditions, pronounced vibration characteristics are observed along the y-axis and z-axis of the volute, with maximum vibration intensities of 1.83 m/s² and 1.80 m/s², respectively. The frequency amplitude exhibits non-constant behavior in the time series. Moreover, variations in the time-frequency characteristics are identified with changing flow rates. A distinct signal with a frequency of 750 Hz manifests in the x-axis and y-axis of the volute when the head experiences a 3% reduction from the cavitation level.Keywords: Vortex pump, Cavitation characteristic, Vibration signal, Time-domain analysis, Frequency-domain analysis, Time-frequency distribution
-
Pages 604-615In order to further extend understanding of the heat transfer characteristics under an enclosed area, the influence of backpressure on a single impingement jet with small nozzle-to-plate spacing (H/D) is studied. Particle image velocimetry (PIV) technique and a commercial fluid dynamics solver (CFD) are respectively employed to investigate the fluid dynamics of the impinging jet, with a Reynolds number (Re) of 3462–6125, at a small nozzle-to-plate spacing (H/D) of 0.25–1.25. Experimental data are in well agreement with numerical simulation data. The findings indicate that the H/D ratio significantly influences the formation of backpressure in the flow field. The backpressure then influences the boundary layer velocity on the impingement surface, in turn affecting the impingement surface's heat transfer characteristics. In addition, a turning point in the horizontal velocity curve of H/D = 0.4 is found for an entire range of jet heights, which is independent of the Reynolds number (Re).Keywords: Backpressure, Small nozzle-to-plate distances, Impingement cooling, Flow characteristic, Heat transfer performance
-
Pages 616-627Liquefied petroleum gas (LPG) is considered one of the gases widely used in many industrial and residential sectors. Still, due to its different compositions, mainly propane (C3H8) and butane (C4H10), it can have other combustion characteristics. This paper aims to conduct an experimental analysis to study the impact of LPG composition on the stability map (limits of blowoff and flashback) of the premixed flame in a tangential swirl burner. Four LPG mixtures were used with different proportions of ethane (C2H6), propane (C3H8), butane (C4H10), and pentane (C5H12). Three burner nozzles at diameters of 20, 25, and 30 mm have been used, which gave three swirl numbers of 0.918, 1.148, and 1.377, respectively. The results indicate that increasing the swirl number (S) from 0.918 to 1.377 for all LPG mixtures accelerated the flashback propensity (getting worse) while the blowoff resistance improved; thus, a rising S gave a better stability map. As for the effect of the LPG composition, it was found that the maximum flame temperature was for the LPG mixture containing high percentages of butane (C4H10), while the lowest was for the mixture containing fewer percentages of butane. Changing the LPG composition had an apparent effect on the flashback limits and a slight effect on the blowoff limits; it was found that mixtures containing high percentages of butane increased flame speeds and increased the flashback propensity. Compared to LPG mixtures, the flame stability map was widest for LPG mixtures containing lower percentages of butane. Therefore, LPG with propane (C3H8) proportions higher than butane (C4H10) reduces flame temperature, flame speeds, and flashback propensity, thus improving the stability map.Keywords: Flame stability, LPG, Swirl number, Flashback, Blowoff
-
Pages 628-645Cycloidal propellers constitute a specialized category of underwater propulsion devices, widely employed in vehicles requiring exceptional maneuverability. The parameters of the blade-driving mechanism directly impact the propeller performance. Hence, the effect of variations in the geometric parameters of the blade-driving mechanism on the hydrodynamic performance of cycloidal propellers must be investigated. In this study, a specific set of four-bar and mixed four-bar/five-bar mechanisms are taken as examples, and the effect of linkage-length variations on the hydrodynamic performance of cycloidal propellers was analyzed using numerical simulation methods. First, we established a physical model of the cycloidal propeller, and then derived the relationship between blade-rotation and revolution angles. Subsequently, by solving the Navier–Stokes equations and employing computational fluid dynamics simulations based on viscosity, an analysis is conducted to reveal the trends in the impact of different linkage-length combinations on the hydrodynamic performance of the cycloidal propeller. Finally, the outcomes of the numerical simulations are interpreted using the wing element theory. In similar blade-driving mechanisms, the effects of varying linkage lengths on propeller hydrodynamic performance are determined through alterations in the blade rotation angle range and equilibrium position. An increase in the range of the blade-rotation angle significantly enhances the hydrodynamic performance of the cycloidal propeller. This research employs a more realistic auto-propulsion mode for numerical simulations, establishing a mapping relationship between the blade-driving mechanism and hydrodynamic performance of the cycloidal propeller, while analyzing the underlying influencing mechanisms. Furthermore, crucial numerical simulations and theoretical foundations are employed for designing the four-bar and mixed four-bar/five-bar mechanism cycloidal propellers. The findings of this study could also be used in similar cycloidal propellers with multilinkage mechanism.Keywords: Cycloidal propeller, Four-bar mechanism, Mixed four-bar, five-bar mechanism, Numerical simulation, Self-propulsion
-
Pages 646-657In order to study the unsteady flow and vortex characteristics of tongue cavitation, numerical calculation is carried out for the whole flow channel given different conditions. Then, the calculation results are verified experimentally. The results show that after the occurrence of tongue cavitation in the centrifugal pump, it deteriorates with the decrease of NPSHa. However, when NPSHa is reduced to 3.78 m, it does not change significantly anymore with the decrease of NPSHa. The extrusion of fluid by the vapor at the tongue promotes the formation of the separation vortex, and the re-jet flow caused by the separation vortex leads to vapor shedding. The frequency of cavitation shedding is consistent with the frequency of vortex shedding. In the vorticity transport equation, the relative vortex stretching term and the relative vortex dilatation term dominate the vapor shedding by controlling the change in vorticity. The baroclinic torque term mainly affects the change of vorticity at the vapor-liquid interface, but to a much lesser extent than the first two terms.Keywords: Centrifugal pump, Tongue cavitation, Vortex, Vorticity transport equation, Stability
-
Pages 658-671The present work reports a CFD study of the magneto-convection of a ferrofluid (Fe3O4/water) circulating in a mini-channel under the influence of different vortex generators (fins and permanent magnets). The lower surface of the mini-channel is maintained at a constant temperature, while the upper surface is thermally insulated. The influence of fins, magnetic field intensity, and Reynolds number on the thermal and dynamic characteristics of the flow was numerically investigated using the finite volume method. The obtained results show that the coexistence of these two types of vortex generators considerably affects the flow structure; Entropy generation and heat transfer rate. Finally, the analysis of the different results shows that the concurrent presence of both the magnetic field and the fins results in a notably more efficient system. Using magnetic sources and fins simultaneously in a system with an intense magnetic field and a low Reynolds number can lead to a large gain in heat transfer.Keywords: Ferrofluids, Vortex generator, Magnetic source, Magnetic body force, Entropy generation
-
Pages 672-683This paper studies the evolution and fluid distribution characteristics of a high-speed projectile’s cavity in the water based on joint research, a method involving experiment and numerical simulation. Specifically, we develop an experimental platform and a numerical calculation model for a high-speed projectile to observe its initial cavity evolution characteristics in the water at different velocities and close ranges. Additionally, this work investigates the evolution mechanism of the cavitation process and its fluid distribution law inside the cavity and studies the evolution characteristics of the cavitation stage under different velocities. The results reveal that after the projectile enters the water, the cavity is gourd-shaped and symmetrical, with a necking phenomenon at the tail and the cavity falling off. The cavitation process can be divided into the surface closure, saturation, deep closure, and collapse stages according to the fluid distribution changes in the cavity. Suppose the projectile has a certain speed with the water, its velocity increases. In that case, the cavity generation rate decreases, the growth rate of the water vapor volume in the cavity decreases, the peak water vapor volume content reduces, and the volume of air in the saturation phase of the cavity becomes increases having a range of 6% to 9%. Additionally, the cavity surface closure dimensionless time grows logarithmically as the velocity changes from 0 m/s to 500 m/s, the cavity saturation dimensionless time decreases approximately linearly, and the cavity depth closure dimensionless time is unaffected by velocity changes.Keywords: Cavity, Velocity, Fluid distribution characteristics, Projectiles, Numerical simulation
-
Pages 684-696An oscillating water column (OWC) is typical of axial rotor turbines, which are used to convert ocean wave energy into electrical energy. This device impacts downstream pressure pulsations when its rotor becomes eccentric. This study compared the details of pressure pulsations downstream of eccentric and non-eccentric rotors under three operating conditions: low flow A, high-efficiency flow B, and high flow C. Computational fluid dynamics (CFD) simulations based on the pulsation tracking network (PTN) method were used for the OWC device to compare the experimental results. The results indicate downstream pressure pulsations were mostly dominated by the blade frequency in non-eccentric low-flow cases. In the other eccentric operating conditions, downstream pressure pulsations were mainly dominated by the 2-, 3.6-, 6-, and 7-times rotation frequencies and the 0.5-times blade frequency. The phase change of downstream pressure pulsations in eccentric and non-eccentric conditions is consistent with the flow direction. The phase change is relatively uniform and steady before eccentricity and becomes turbulent after eccentricity, which affects its steadiness. In this study, the OWC device did not significantly change with or without rotor eccentricity at a 1-time blade frequency intensity; however, at a 1-time rotation frequency, the OWC device showed a significant increase in the pressure pulsation amplitude after rotor eccentricity. The study of the dominant frequency, amplitude, and phase of pressure pulsations in OWC devices with eccentric rotors can help prevent excessive pressure pulsations that can lead to incidents.Keywords: Oscillating water column, Rotor eccentricity, Tip leakage, Radial force, Pulsation tracking network pressure pulsation
-
Pages 697-712Current study presents an experimental analysis of nucleate pool boiling on the GNP/Ni-TiO2 (GNP-graphene nano particle) nano-composite coated copper surfaces. In order to produce the microporous surfaces, a two-step electro-deposition process is used. This deposition results in the formation of a modified surface structure, and various surface morphological characteristics of this modified structure, like wettability, roughness and surface structure are studied. The results reveal an improvement in CHF (critical heat flux) and BHTC (boiling heat transfer coefficient) in case of GNP/Ni-TiO2 coated surfaces. The main elements influencing the improved heat transfer of the GNP/Ni-TiO2nano-composite coating are its increased wettability, roughness, and high thermal conductivity. The SNCCC (superhydrophilic nano-composite coated copper) surfaces have the maximum BHTC of 97.52 (kW/m2K) and CHF of 2043 (kW/m2), which are 93% and 88% higher than the base Cu surfaces respectively. Here, it is analysed how the performance of SNCCC surfaces are enhanced by the impact of different parameters, like the roughness of the surface and wettability. The bubble characteristics at the time of boiling is noticed using a high-speed camera, and several factors such as nucleation site density, bubble departure diameter, and bubble emission frequency are statistically studied for SNCCC surfaces.Keywords: BHTC, Bubble dynamics, CHF, Electrochemical deposition, Superhydrophilic surface
-
Pages 713-725The hydraulic turbine has been used extensively in the field of energy conservation. For turbines that have low heads and large discharge, improving recovery efficiency and stability is crucial due to their significant hydraulic impact. This paper provides a detailed analysis of the correlation between the influence of radial guide vanes on the stability of low-head, large-discharge turbines focusing on hydraulic performance and energy dissipation before and after the implementation of guide vanes. Moreover, in this paper, two types of turbines, with and without guide vanes, were designed considering the desulfurization scenario. Hydraulic efficiency, radial force, and internal flow field mechanics were numerically studied, and validated through experiments. The results reveal that the working range of the hydraulic turbine could be widened and the energy recovery efficiency improved by a maximum of 3.11% in the small flow rate under the action of guide vanes. Furthermore, it results in a substantial reduction in the radial force of the impeller. Subsequently, the variation in entropy production of different components under full flow rate conditions was compared between the models with and without guide vanes. The total energy consumption decreases sharply under overall working conditions due to the flow control ability of guide vanes affecting the flow state. The entropy production rate of the impeller remains the largest regardless of the presence of a guide vane in the turbine. The vortices inside the guide vanes increase obviously with the flow rate increase.Keywords: Guide vane, Low-head, large-discharge, Hydraulic turbine, Hydraulic stability, Entropy generation rate, Vortex characteristics