فهرست مطالب
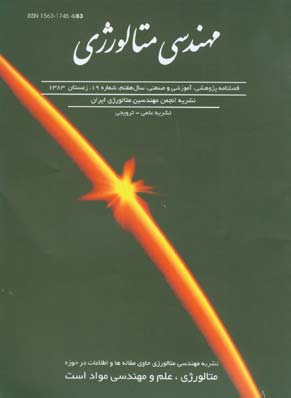
مجله مهندسی متالورژی
پیاپی 19 (زمستان 1383)
- 70 صفحه،
- تاریخ انتشار: 1383/12/15
- تعداد عناوین: 13
-
استراتژی توسعه صنایع تولید آهن و فولاد ایران در برنامه 20 سال آیندهصفحه 5در اغلب کشورهای پیشرفته صنعتی در دهه گذشته، تولید آهن و فولاد و صنایع مشابه،کاهش یافته و در زمینه تولید مواد نو و اطلاعات، فناوری های جدید و کنترل پیشرفته مواد برنامه ریزی شده است. درکشورهای در حال توسعه بالعکس در صنایع تولید آهن و فولاد و سایر صنایع سرمایه بر،انرژی بر و حتی آلوده کننده محیط زیست بیشتر سرمایه گذاری شده است. در ایران در برنامه سوم توسعه از1379 تا1383 شمسی برنامه ریزی شده بود که تولید آهن و فولاد ازحدود 7 میلیون تن یه 7/14 میلیون تن افزایش یابد. برای تولید 2/14 میلیون تن تاکنون قراردادهایی منعقد گردیده است. حتی برای 20 سال آینده بااحتساب صنایع تولید آهن وفولاد خصوصی صحبت از تولید 25 تا28 میلیون تن فولاد در سال است که افزایشی حدود700 هزار تن د رسال (معادل 5 درصد در سال یا احداث یک واحد 700 هزار تنی در سال) می باشد و این رشد بالایی رانشان می دهد. -از تولید سالانه 8/964 میلیون تن فولاد در جهان درسال 2003 میلادی،55/94 درصد از طریق روش سنتی کوره بلند بامصرف کک و 45/5 درصد از طریق روش های احیای مستقیم با مصرف گاز طبیعی و زغال می باشد. هم اکنون در زمینه زغال سنگ کک شو 140 در صد و کک 190 درصد افزایش داشته است. درایران برخلاف زغال سنگ کک شو،ذخایر گاز طبیعی به وفور یافت می شود و ایران از نظر ذخایر گاز طبیعی در جهان در مقام دوم قرار دارد. -در سال 1382 ایران با تولید حدود 43/5 میلیون آهن اسفنجی براساس مصرف گاز طبیعی در جهان در مقام دوم قرار داشت و به زودی به مقام اول ارتقاء خواهد یافت. تولید آهن و فولاد در ایران مازاد بر مصرف سرانه بین المللی می باشد و احتما برای صادرات برنامه ریزی شده است. باتوجه به برنامه ریزی و ضرورت افزایش تعداد واحدهای دولتی و خصوصی، تولید آهن و فولاد درایران با آگاهی از کمبود زغال کک شو در ایران و جهان،برای گسترش صنایع تولید آهن وفولاد، روش سنتی کوره بلند /کنورتور بامصرف کک توجیه پذیر نیست. -از 5/49 میلیون تن آهن اسفنجی در سال 2003 میلادی به روش های احیای مستقیم با مصرف گاز طبیعی حدود 6/64 درصد از طریق میدرکس،7/19 درصد از طریق HYL3/HYL1 و درصد ناچیزی به سایر روش هااز جمله قائم اختصاص داشت. درایران از حدود 43/5 میلیون آهن اسفنجی تولیدی حدود 80 درصد به روش میدرکس تولید شده است. فناوری تولید آهن اسفنجی در کوره های احیا به روش های میدرکس، HYL3 و قائم شناخته شده و بدون مشکل انجام پذیر است. تولید گاز احیا کننده در روش های میدرکس، HYL3 و قائم ازگاز طبیعی و عامل اکسایش جزئی گاز طبیعی در روش میدرکس،گاز خروجی کوره، در روش HYL3 بخار آب و درروش قائم، اکسیژن و گاز خروجی کوره است. -روش های میدرکس و HYL3 به رفورمر و لوله های فولادی مجهز هستند و لوله ها دربرابر نوسانات حرارتی و ترکیب گاز طبیعی و سنگ آهن مصرفی، حساس هستند. همچنین امکان استهلاک آنها از درون و برون وجود دارد. این لوله ها وارداتی هستند و فناوری ساخت آنها پیشرفته و انحصاری است. کاتالیزور درون آنها نیز در برا بر ترکیب گاز طبیعی و سنگ آهن مصرفی حساس می باشد و امکان مسمومیت آنها وجود دارد. کاتالیزور مصرفی درآنها نیز وارداتی است. فناوری تولید آن، اختصاصی و پیشرفته است. درصورتی که روش قائم فاقد رفورمر و کاتالیزور می باشد و از این ضعف ها مبرا است. - باتوجه به شرایط خاص سنگ آهن برای مصرف درکوره میدرکس و ضرورت تامین سالانه حدود 36 میلیون تن سنگ آهن پر عیار در 20 سال آینده (معادل 25 میلیون تن فولاد درسال)، عدم مزیت خاص فناوری روش میدرکس نسبت به روش قائم و بالعکس قائم نسبت به روش های احیای مستقیم باگاز طبیعی که از پیشرفته ترین فناوری برخوردار است،منطقی به نظر می رسد که استراتژی توسعه صنایع تولید آهن و فولاد درایران بیشتر بر اساس عدم وابستگی برنامه ریزی شود.
-
تاثیر پارامترهای مختلف ساخت بر خواص الیاف کربن تولید شده از الیاف پلی اکریلونیتریلصفحه 12برای تولید کربن از مواد اولیه مختلفی شامل الیاف پلی اکریلونیتریل(PAN)، الیاف سلولزی وقیر استفاده می شود که تولید این الیاف ازPAN، از بیشترین میزان تولید وگسترده ترین کاربرد برخوردار می باشد.فرآیند تولید به این روش شامل سه مرحله اساسی شامل پایدار سازی (درمحیط اکسیدی)، کربونیزاسیون و گرافیته کردن(هردو در محیط غیر اکسیدی)است که باتغییر پارامترها در طی مراحل مذکور و همچنین قبل و بعد از آنها می تو ان انو اع الیاف کربن با خواص مختلف تولید کرد. دراین تحقیق، تغییر پارامترها درسه مرحله مذکو ر(شامل تغییرات دما،زمان وشیب حرارتی فرآیند، نوع محیط و عملیات کشش)مورد بررسی قرار گرفته اند. به علاوه،درمرحله پیش از پایدارسازی تاثیر استفاده از عوامل فعال کننده و کاتالیزور، فرآیند کششی و غوطه وری در محلول های مختلف آلی و غیر آلی،در مرحله پیش از کربونیزاسیون تاثیر عملیات خشک کردن و غوطه وری در محلول های مختلف و در مرحله پس از گرافیته کردن تاثیر کاشت یون، عملیات سطحی با ترکیب های مختلف و غوطه ور ی در انواع محلول ها مطالعه شده اند. درمجموع، تغییرات انواع پارامترها در مراحل مختلف در قالب 35 تکنیک و فرآیند متفاوت باذکر تاثیر هر یک بر خواص الیاف کر بن، ارائه شده است. بررسی ها نشان می دهند باتغییر صحیح پارامترها درقالب فرآیند های مختلف می توان خواص مکانیکی و فیزیکی، جهت گیری ساختاری و خواص سطحی و اتصالی الیاف کربن راباتوجه به نوع عملیات انجام شده، بهبود بخشید. همچنین می تو ان زمان عملیات پایدارسازی یاکربونیزاسیون ودر مجموع زمان فرآیند تولید الیاف کربن راکاهش داد.
کلیدواژگان: الیاف کربن، پلی اکریلونیتربل، پایدارسازی، کربونیزاسیون، خواص -
تاثیر ناخالصی های گازی بر ساختار میکروسکوپی و سختی آلیاژ حافظه دار نایتیونلصفحه 21آلیاژ نایتینول از دو عنصر نیکل و تیتانیم با درصد اتمی مساوی یا نزدیک به هم درست شده است. این آلیاژ به سبب داشتن خواص منحصر به فردی هم چون حافظه داری، زیست سازگاری، نرمی وسفتی انتخابی مورد توجه مهندسین صنایع جدید و متخصصین رشته های پزشکی و بیو مواد قرار گرفته است. لازمه تولید آلیاژ نایتینول با خواص مطلوب،دقت در انتخاب ماده اولیه و بهینه سازی فرآیند ساخت است. به هم خوردن ترکیب شیمیایی و یاجذب ناخالصی از محیط، تاثیرات عمده ای بر خواص آلیاژ می گذارند. این مقاله به تاثیر تغییر ترکیب شیمیایی و نفوذ ناخالصی های گازی بر خواص آلیاژ پرداخته و اهمیت این تاثیرات هنگام به کارگیری آلیاژ رامورد بحث قرارداده است. درنتیجه معلوم شده که حضور گازهایی همچون نیتروژن، اکسیژن،هیدروژن،و آرگن در هنگام ذوب آلیاژ سبب افزایش سختی، کاهش کارپذیری و تغییر ویژگی های حافظه داری آلیاژ می گردد. تصاویر میکروسکوپی آموزنده ای از مورفولوژی رسوبات حاصل از ترکیب شدن گازهای باآلیاژنیز در مقاله ارائه شده اند.کلیدواژگان: نایتینول، حافظه داری شکلی، مورفولوژی، سختی، ناخالصی، گاز
-
بررسی ریزساختار فولاد میکروآلیاژ ریختگی زیرکونیم دارصفحه 29فولادهای میکروآلیاژی از خانواده فولادهای کم آلیاژ با استحکام بالا بوده که دارای خواص مکانیکی مناسب و مطلوبی هستند. دراین فولادها، دستیابی به خواص مورد نظر مرهون حضور عناصر میکرو آلیاژ و تاثیر این عناصر بر ریز ساختار فولاد می باشد. فولاد های میکرو آلیاژ ریختگی، دسته ای از فولادهای میکرو آلیاژ بوده که در مقایسه حالت نوردی و فورج،مطالعات به مراتب کمتری را به خود اختصاص داده است.از طرفی زیرکونیوم نیز عنصری است که کمتر به عنوان یک عنصر میکرو آلیاژ مورد توجه قرار گرفته است و دربسیاری از موارد به عنوان کنترل کننده شکل آخال های سولفیدی در فولاد های آرام شده استفاده گردیده است.اما مشخصات ترمودینامیکی زیرکونیوم نشان از تمایل شدید این عنصر برای ترکیب با اکسیژن، نیتروژن و کربن دارد.براین اساس با اکسیژن زدایی مناسب مذاب،زیرکونیوم می تواند تشکیل رسوبات کاربیدی،نیتریدی و یا کربو نیتریدی دهد. دراین تحقیق، نقش زیرکونیوم،به عنوان یک عنصر میکرو آلیاژ، بر ریز ساختار فولاد ساده کربنی ریختگی مورد بررسی قرار گرفته است.بر همین اساس نمونه هایی با درصد های مختلف زیرکونیوم تهیه شد.سپس فرآیندهای عملیات حرارتی لازم بر روی آنها انجام گرفت.برای ارزیابی نتایج از میکروسکوپ نوری،SEM وXRDاستفاده گردید. در بررسی میکروسکوپ نوری، حداکثر کاهش اندازه دانه های فریت درنمونه با 005/0درصد زیرکونیم به میزان 39 درصد بدست آمد. در حالی که برای نمونه های حالت کوئنچ و پیر برگشت شده تغییرات محسوسی مشاهده نگردید. از طرفی مطالعات SEMو XRDنمونه ها نیز حضور رسوبات حاوی زیرکونیم راتایید می نمایند.
کلیدواژگان: فولاد میکروآلایژ ریختگی، زیرکونیم، عملیات حرارتی، ریزساختار -
تغییرات ریزساختاری و رفتار سیلانی آلیاژ آلومینیم A356 با ساختار غیر دندریتی در حالت نیمه جامدصفحه 35ساخت قطعات صنعتی از آلیاژ های آهنی و غیر آهنی در حالت نیمه جامد امروزه به عنوان روشی نوین مطرح است. بررسی ریز ساختاری نمونه های تهیه شده از آلیاژ آلومینیم A356نشان می دهد که ساختار دندریتی فاز جامد اولیه شکسته شده و به صورت نزدیک به حالت کروی در می آید. تفاوت اندازه ذرات اولیه و میزان کرویت ذرات مختلف، ضرورت عملیات اصلاح ریز ساختار را آشکار می سازد. عملیات ذوب جزئی مجدد به عنوان یک فرآیند اصلاحی درریز ساختار مورد آزمایش قرار گرفت و تاثیر آن بر ریز ساختار و میزان جدایش فاز مایع از جامد دراکستروژن معکوس نمونه ها بررسی گردید. نتایج نشانگر این است که بعداز یک ساعت نگهداری درحالت نیمه جامد، جدایش فازها از یکدیگر در مرحله اکستروژن تا حد زیادی کاهش پیدا می کند.
کلیدواژگان: ریخته گری نیمه جامد - تکامل ریزساختار، جدایش فازها، ذوب جزئی مجدد، اکستروژن معکوس -
افزایش توان کوره های پلاسما با افزودن CO2 به اتمسفر آنصفحه 43استفاده از کوره پاتیلی مجهز به الکترودهای گرافیتی به علت احتمال افزایش کربن برای فولادها مناسب نمی باشد. دراین مورد استفاده از الکترودهای فلزی مشعل پلاسما که با آرگن کار می کنند مناسب تر است. هم اکنون حداکثر توان مفید با استفاده از جریان متناوب حاصل از سه مشعل پلاسمای آرگنی حدود 4mw است. برای بررسی چگونگی افزایش ولتاژ قوس ناشی از افزودن co2 به اتمسفر کوره روی 200kg بار درکوره آزمایشگاهی مجهز به دو مشعل پلاسمای آرگنی تجربیاتی انجام شده است.با افزودن 20 درصدco2 ولتاژ قوس 30 سانتیمتری از 100 به 173 ولت افزایش یافته است. با توجه به تجزیه فولاد و آنالیز گاز خروجی، میزان اکسیژن منتقل شده از دی اکسید کربن موجود در پلاسما به مذاب نیز اندازه گیری شده است. پس از تشکیل لایه سرباره حدود 10% اکسیژن وارد مذاب می شود. مقادیر اندازه گیری شده حاکی از افزایش توان و انتقال اکسیژن درپاتیل 50 تا 150 تنی کوره های پلاسمای سه شعله 12KA AC بوده است. درکوره ای با اتمسفر دارای 60 درصد CO2، توان مفید موجود درسیستم پلاسما باید برابر 10MW در مقایسه با MW 3/5دراتمسفر آرگن خا لص بوده باشد. به تجربه ثابت شده که به علت هدایت کم گاز دراین کوره و انتقال اندک جرم، میزان اکسیژن منتقل شده نسبتا نا چیز می باشد. افزودن 40 درصد CO2 توانایی حرارت دادن به 110 تن فولاد با سرعت گرم کردن 3K/min رادارد. درحالیکه مقدار اکسیژن در30 دقیقه تا حدود 10ppm افزایش می یابد. دراین حالت میزان دی اکسید کربن لازم 012m3t-1 می باشد.
-
رسم منحنی سختی بر حسب عمق برای قطعات کربوره شده به کمک کامپیوترصفحه 49امروزه دربسیاری از فرآیندهای تولید استفاده از برنامه های کامپیوتری رایج است. به کمک این برنامه ها و نرم افزار های خاص، کنترل شرایط تولید و تغییر در آنها میسر می باشد. از جمله فرآیندهای مهم درصنعت، کربوراسیون قطعات فولادی است. پس از این عمل درصد کربن قطعه درطول سطح مقطع آن تغییر می کند. درنتیجه سختی درعمق های مختلف از سطح قطعه متفاوت خواهد بود. با توجه به اهمیت سختی درسطح و عمق این قطعات، نیاز به برنامه ای است که بتواند قبل از انجام فرآینداین مقادیر راتخمین بزند. دراین تحقیق با استفاده از زبان برنامه نویسی فرترن و نرم افزار ORIGIN برنامه ای کامپیوتری نوشته شد که با دریافت داده های مربوط به شرایط کربوراسیون، مقادیر سختی در سطح و عمق قطعه را به عنوان خروجی به ما می دهد. بنابراین بسته به سختی مورد نیاز می توان قبل از انجام عملیات کربوراسیون، شرایط کاری را تنظیم کرد.کلیدواژگان: کربوراسیون، سختی، نرم افزار، فرترن
-
ارزیابی علم و فناوری - اولین ارزیابی کلان، 1382صفحه 54
-
شخصیت های متالورژی، علم و مهندسی مواد ایرانصفحه 57
-
آینده صنعت در ایرانصفحه 58
-
آشنایی با دانشکده های مهندسی متالورژی و مواد / مجتمع صنعتی اسفراین (تولید کننده فولاده ای آلیاژی آهنگری در ایران و خاورمیانه)صفحه 61
-
آشنایی با دانشکده های مهندسی متالورژی و مواد / دانشگاه تهرانصفحه 64
-
همایش های داخلی و خارجی متالورژی و موادصفحه 66