فهرست مطالب
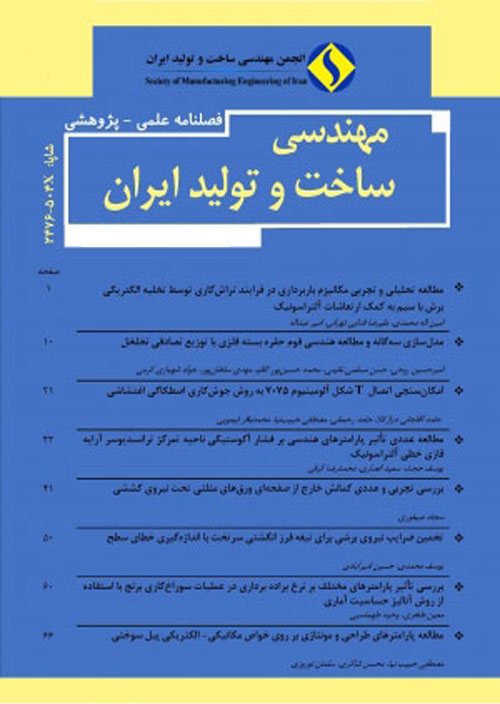
مجله مهندسی ساخت و تولید ایران
سال هشتم شماره 5 (امرداد 1400)
- تاریخ انتشار: 1400/05/26
- تعداد عناوین: 6
-
-
صفحات 1-13در این پژوهش اتصال سرامیک زیرکونیا به S.S310S با استفاده از فرایند لحیم کاری سخت کوره ای تحت اتمسفر گاز آرگون صورت گرفت. آلیاژ پر کننده استفاده شده در این فرایند، پایه نقره بوده که فاقد عناصر فعال در ترکیب شیمیایی خود است. باتوجه به این موضوع که برخلاف S.S310S، سرامیک های اکسیدی از ترشوندگی کمی در برابر پرکننده های آلیاژی برخوردارند، لذا جهت فعال نمودن سطح زیرکونیا از پوشش خالص Ti استفاده شد. ضخامت بهینه لایه پوششی nm200 تعیین شد. هدف از پوشش دهی کاهش مسیر نفوذ عنصر Ti در سطح نمونه سرامیکی و ایجاد لایه واکنشی TiO2 در آن منطقه می باشد. نمونه ها از طریق فرایند لحیم کاری سخت به مدت یک ساعت در دو دمای 1000 و °C 1100 اتصال یافتند. نمونه های اتصال دهی شده با فرایند لحیم کاری سخت در دو دمای 1000 و °C 1100 با زمان نگه داری یک ساعت صورت گرفتند. نتایج بدست آمده از آزمون برشی نمونه های لحیم کاری شده استحکام بالای نمونه های با دمای °C1000 به مقدار متوسط MPa117را نشان داد که در مقایسه با نمونه های لحیم کاری شده در دمای °C1100(MPa 96) افزایش MPa 21را داشتند. برای آنالیز ریزساختاری و متالوگرافی به ترتیب از SEM و میکروسکوپ نوری استفاده شد. نتایج آنالیز عنصری و خطی بدست آمده ازآن ناحیه نشان داد کاهش استحکام علارغم افزایش دما به دلیل نفوذ بیش از حد اجزای ماده لحیم و همچنین تشکیل لایه واکنشی غیریکنواخت (کمانی شکل) در سطح زیرکونیا می باشد. لایه های واکنشی تشکیل شده در این فرایند شامل: ترکیبات Cu57Zr4 و Tio2 (زیرکونیا) و ترکیبات FeAg و FeCrNi (S.S310S) و فاز AgCu در ناحیه لحیم می باشد.کلیدواژگان: لحیم کاری سخت، آنالیز ریزساختار، آزمون برشی
-
صفحات 14-22با توجه به اینکه پیزوکامپوزیت های با الگوی اتصال 3-0 انعطاف پذیری خوبی داشته و در ترانسدیوسرهای زیرآبی کاربرد دارند، این تحقیق ضمن مطالعه روش های مختلف ارایه شده جهت ساخت مواد پیزوکامپوزیت که اغلب در مرحله توسعه و نوآوری قرار دارند؛ با بررسی ویژگی ها، مزایا و معایب هر روش، روش تلفیقی و کم هزینه ای جهت ساخت پیزوکامپوزیت های نوع 3-0 با قابلیت استفاده برای طیف وسیعی از مواد پلیمری ارایه کرده است. با استفاده از این روش پیزوکامپوزیت های PZT/EP و PZT/EP+TPU با درصدهای وزنی شامل 30 تا 70 درصد PZT ساخته شد. برای این کار ابتدا پودر PZT با رزین اپوکسی ترکیب و به منظور پراکنده سازی یکنواخت در زمینه پلیمر، از همزن مغناطیسی استفاده گردید. پس از افزودن هاردنر به محلول، جهت پراکنده سازی بهتر و جلوگیری از چسبندگی ذرات پیزوسرامیک به همدیگر در زمینه پلیمر، از همزن التراسونیک استفاده گردید. پس از افزایش ویسکوزیته محلول، مجدد از همزن مغناطیسی استفاده گردید. سپس محلول را درون قالب ریخته و در ظرف دسیکاتور متصل به پمپ خلا قرار داده تا فرایند حباب زدایی محلول انجام شود. پس از تکمیل فرایند پلیمریزاسیون، نمونه ها خشک شده و فرآیند پخت آن ها تکمیل گردید. پیزوکامپوزیت ها پس از پولیش کاری، با استفاده از لایه مسی الکترودگذاری شدند. در مرحله آخر، فرآیند قطبی سازی با استفاده از روش تخلیه کرونا انجام شد. نتایج آنالیزهای XRD، FT-IR و SEM بررسی گردید و پیزوکامپوزیت های ساخته شده را به جهت اطمینان از صحت مراحل ساخت، الکترود گذاری، قطبی سازی و همچنین عملکرد صحیح خاصیت پیزوالکتریک، به-صورت متناوب تحت تنش قرار داده و ولتاژ خروجی به وسیله اسیلوسکوپ مشاهده گردید.کلیدواژگان: پیزوالکتریک، پیزوسرامیک، پیزوکامپوزیت، ترانسدیوسرآکوستیک
-
صفحات 23-29با پیشرفت تکنولوژی و نیاز فراوان به قطعات ظریف و سبک با استحکام بالا، نیاز به جوشکاری ورق های نازک نیز بیشتر شده است. امروزه از جوشکاری نقطه ای لیزری جهت اتصال ورق های نازک فولاد زنگ نزن آستنیتی در تولید وسایل آشپزخانه استفاده میشود. استحکام و اندازه دکمه جوش دو پارامتر مهم در تعیین کیفیت جوش نقطه ای لیزری هستند. در این پژوهش ورق نازک فولاد زنگ نزن استنیتی 316 به ضخامت 7/0 میلیمتر به روش جوشکاری لیزر به صورت اتصال لبه روی هم جوشکاری نفطه ای شد. برای انجام این جوشکاری از دستگاه جوش لیزر Nd:YAG پالسی با توان متوسط استفاده گردید و اثر پارامترهای موثر بر اندازه ی دکمه ی جوش و استحکام نهایی نقطه ی جوش به صورت تجربی مورد بررسی قرار گرفت. فرکانس لیزر در سه سطح 5، 7 و 9 هرتز، پیک توان لیزر در سه سطح 1670، 1750 و 1800وات و زمان روشنی پالس در سه سطح 6، 8 و 10میلی ثانیه به عنوان پارامترها و سطوح آزمایش مورد بررسی قرار گرفتند. در این پژوهش برای طراحی آزمایش از روش تاگوچی 9L استفاده شد. نتایج آزمایش ها نشان دادند که با افزایش توان لیزر قطر دکمه جوش کاهش یافته، با افزایش زمان روشنی پالس قطر دکمه جوش ابتدا افزایش و سپس کاهش یافته و با افزایش فرکانس لیزر قطر دکمه جوش ابتداکاهش و سپس افزایش یافته است. همچنین با افزایش زمان روشنی پالس و فرکانس لیزر استحکام جوش نقطه افزایش یافته و با افزایش توان لیزر استحکام جوش نقطه ابتدا افزایش و سپس کاهش یافته است.کلیدواژگان: جوشکاری نقطه ای لیزری، دکمه جوش، استحکام جوش
-
صفحات 30-42
در قسمت بنزین سازی پالایشگاه اصفهان از کمپرسور مدل افقی دو طرف رفت و برگشتی شرکت نیومن ایزر در سه مرحله تراکم استفاده می شود. از آنجاییکه استفاده از روغن در این نوع از کمپرسورها مجاز نمی باشد از کفشک پیستون جهت جلوگیری از سایش بین پیستون و روکش سیلندر در محفظه تراکم استفاده می شود. سرعت سایش روکش سیلندر و کفشک پیستون و به دنبال آن رینگ های پیستون در سه مرحله یکسان نبوده و لذا زمان تعمیر و نگهداری آنها یکسان نمی باشد. در این مطالعه درنظر است با استفاده از الگوریتم ژنتیک جرم پیستون را با رعایت قیود طراحی اعم از حداقل ضخامت جداره پیستون و در محدوده بودن تنش های فون میسز به حداقل میزان ممکن کاهش داد تا در نهایت عمر کفشکها، روکش سیلندر، دسته پیستون و... با کاهش وزن پیستون افزایش و به دنبال آن شدت سایش آنها کاهش یابد. یکی از دلایل سایش، وزن سنگین پیستون و ملحقات آن بوده که در این خصوص لازم است پیستون بهینه شده با کاهش جرم، تمامی معیارهای مکانیکی لازم مانند معیارهای استاتیکی، دینامیکی، خستگی و تغییرشکلهای مجاز را برآورده نموده و در محدوده مجاز طراحی قرار گیرد. لذا در این تحقیق آلیاژ آلومینیوم 7075 مورد بررسی قرار گرفته و به کمک الگوریتم ژنتیک هندسه بهینه پیستون با کد نویسی در نرم افزار پایتون تعیین شده که موجب گردید وزن پیستون چدنی از 780 کیلوگرم به 271 کیلوگرم از جنس آلومینیوم و بعد از بهینه سازی تا 261 کیلوگرم کاهش یابد.
کلیدواژگان: کمپرسور رفت و برگشتی، پیستون، آلیاژهای آلومینیوم، بهینه سازی، الگوریتم ژنتیک -
صفحات 43-50
فولاد های با عملیات حرارتی کوینچ - بخش بندی (Q-P) جزو نسل سوم فولادهای پیشرفته استحکام بالا هستند که به دلیل داشتن مجموعه قابل توجهی از خواص مکانیکی شامل استحکام بالا به همراه انعطاف پذیری مناسب گسترش یافته اند. بخش بندی یک عملیات حرارتی جدید مبتنی بر نفوذ کربن از فاز مارتنزیت به فاز آستنیت باقیمانده است. در این پژوهش نخست آلیاژ با ترکیب شیمیایی wt%Al054/0- wt%Si 5/1 -wt%Mn 2/2 -wt%C 21/0- Fe حاوی 08/0 % Ti بعنوان یک میکروآلیاژ در یک کوره ذوب القایی در خلا (VIM) تهیه شد. عملیات تصفیه و تخلیص آلیاژ با استفاده از یک کوره پالایش با سرباره الکتریکی انجام و پس از کاهش گوگرد و اکسیژن، آلیاژ بصورت شمش ریخته گری گردید. شمش مزبور بمدت 3 ساعت در دمای °C1200تحت عملیات حرارتی همگن سازی قرار گرفت. شمش همگن سازی شده توسط فرآیندهای نورد گرم و سرد بصورت ورقی به ضخامت mm 5/1 نورد شد. پس از اعمال عملیات حرارتی Q-T و Q-P-T روی نمونه های ورق، خواص آنها با استفاده از SEM ،XRD، ریزسختی سنجی، تست کشش و آزمون اریکسون مورد ارزیابی قرار گرفت. نتایج حاصل نشان دادند که نمونه های عملیات حرارتی Q-P-T مجموعه مطلوب تری از استحکام و انعطاف پذیری نسبت به نمونه های Q-T دارند. استحکام و کرنش شکست نمونه های Q-P-T به ترتیب برابرMPa 1050 و 24% و نمونه های Q-T برابر MPa 1185و 18% اندازه گیری شدند. نمونه های Q-P-T ضمن حفظ استحکام بالا، انعطاف پذیری بیشتری را نسبت به نمونه های Q-T از خود نشان دادند.
کلیدواژگان: کوئنچ - بخش بندی (Q-P)، آستنیت باقی مانده، استحکام کششی، کرنش شکست، میکروآلیاژ -
صفحات 51-62
در حال حاضر در فرآیندهای ساخت و مونتاژ مجموعه های صنعتی چندلایه (ساندویچی) با جنسهای مختلف، مانند قالب سازی و یا فیکسچرسازی، ابتدا باید قطعات مونتاژ و سپس سوراخکاری هم زمان شوند، در غیر این صورت دقت مورد نظر ابعادی یا هندسی حاصل نمی گردد. برای ایجاد این سوراخ ها عمدتا از فرآیندهای سوارخکاری متداول استفاده می شود که به علت شکل هندسی و صفر بودن سرعت برشی در نوک مته، موجب تغییر شکل پلاستیک شدید در موضع برش می شود. استفاده از روش سوراخکاری متداول ممکن است باعث تنزل دقتهای ابعادی، هندسی و همچنین یکپارچگی سطح دیواره داخلی سوراخ ها شود. جهت کاهش مشکلات ذکر شده یکی از راهکارهای نسبتا نوینی که برای سوراخکاری پیشنهاد می شود، روش فرزکاری مارپیچ می باشد. در پژوهش جاری، جهت مقایسه قابلیتها، مزایا و معایب این دو روش مختلف سوراخکاری، مجموعا 18 آزمایش سوراخکاری با استفاده از تکنیکهای سوراخکاری متداول و فرزکاری مارپیچ و با در نظر گرفتن 2 پارامتر متغیر سرعت برشی و سرعت پیشروی (هر کدام در 3 سطح) بر روی قطعه کار ساندویچی چندلایه فلزی که دارای 3 لایه مختلف فولادی MO40، 304L و CK45 است، انجام گرفت. بر اساس نتایج به دست آمده، می توان بیان داشت جهت حصول به تلرانسهای ابعادی (اندازه قطر سوراخ) و هندسی (گردی مقطع سوراخ) مطلوب، فرآیند سوراخکاری متداول عملکرد بهتری نسبت به روش فرزکاری مارپیچ داشته است ولی از نظر رسیدن به زبری سطح کمتر و یکپارچگی سطح مطلوب تر (عیوب سطحی کمتر)، روش فرزکاری مارپیچ، عملکرد بهتری نسبت به سوراخکاری متداول داشته است
کلیدواژگان: سوراخکاری، فرزکاری مارپیچ، یکپارچگی سطح، تلرانس ابعادی، تلرانس هندسی
-
Pages 1-13In this study, zirconia is joined to S.S310S using a brazing in a furnace under the argon atmosphere. The filler used in this process is a silver-based-alloy which has no active elements in its chemical composition. According to the fact that, unlike S.S310S, oxide ceramics have low wettability compared to alloy fillers, to activate the surface of zirconia with pure Ti-coating. The optimum thickness coating layer was determined to be 200nm. The purpose of surface coating is to reduce the penetration of the Ti-element on the surface of the ceramic sample and to create a TiO2 reaction layer in that area. The samples were joined by a brazing process for one hr. The results obtained from the shear test of brazed specimens showed high strength of specimens with a temperature of 1000˚C at an average of 117 MPa that compared to brazed samples at 1100˚C (96MPa), they had an increase of 21MPa. Then, for microstructural analysis and metallography of the joint area the SEM and OM, were performed. The results of elemental and linear analysis obtained from that area showed the reason for the decrease in strength with increasing temperature is due to excessive penetration of filler components then the formation of non-uniform reaction layer on the zirconia surface. The reaction layers formed in the process include Cu57Zr4 and TiO2(zirconia) and FeAg and FeCrNi (S.S310S) and AgCu phase in braze zone.Keywords: Brazing, Microstructure analysis, Shear strength test
-
Pages 14-22Since piezocomposites with 0-3 connectivity are flexible and commonly used in acoustic transducers, we review some of their fabrication methods, which are mainly under the development stage, and evaluate cons and pros of each method. We then suggest a budget type solution casting method to prototype 0-3 piezocomposites which can be used with a wide range of polymeric materials. Using this method, we fabricate PZT/EP and PZT/EP+TPU piezocomposites with PZT weight fractions from 30 to 70 percent. First, PZT powder was mixed with the epoxy resin, and a magnetic stirrer was used to achieve a uniform dispersion of PZT particles in the polymer. After adding the hardener to the solution, a sonicator were used to avoid agglomeration of PZT particles and prepare a uniform solution. The solution was then poured it into a mold and placed in a desiccator container, connected to a vacuum pump, to perform the degassing process. After the polymerization process was completed, samples were dried to complete the curing process. After polishing, the copper electrode plates were placed on both sides of the piezocomposite elements. Finally, the polarization process was performed using the corona discharge method. The results of XRD, FT-IR and SEM analysis depict the uniform dispersion of the PZT particles within the polymer. The prototyped specimens generate electric charge, measured by an oscilloscope, under a dynamic loading.Keywords: Piezoelectric, Piezoceramic, Piezocomposite, Acoustic transducer
-
Pages 23-29With the advancement of technology and the great need for thin and light parts with high strength, the need for welding thin sheets has also increased. Nowadays, laser spot welding is used to connect thin sheets of austenitic stainless steel in the production of kitchen wares. The strength and size of the weld nugget are two important parameters in determining the quality of laser spot welding. In this study, thin sheets of stainless steel 316 with a thickness of 0.7 mm were laser spot welded. To perform this welding, a medium power Nd: YAG laser welding machine was used and the effects of effective laser parameters on the strength and size of the weld button were investigated experimentally. Laser frequency at three levels of 5, 7 and 9 Hz, peak laser power at three levels of 1670, 1750 and 1800 W and pulse ON time at three levels of 6, 8 and 10 milliseconds were selected as parameters and test levels. Taguchi L9 method was used to design the experiments. The experimental results show that with increasing laser power, the diameter of the welding button decreases, with increasing the pulse ON time, the diameter of the welding button first increases and then decreases, and with increasing laser frequency, the diameter of the welding button decreases and then increases. In addition, with increasing pulse ON time and laser frequency, the strength of weld nugget increases, and with increasing laser power, the strength of weld button increases firstly and then decreases.Keywords: Laser spot welding, weld nugget, Weld strength
-
Pages 30-42
Double action horizontal Neuman Esser reciprocating compressors are utilized during three steps of compressing hydrogen in gasoline production section of many refineries including Esfahan refinery. Since application of any lubricant during compression process are not permitted in these compressors, Teflon ridder rings are placed between piston and cylinders to act as a lubricant and prevent any direct contact between pistons and cylinders. The wearing rate of the ridder rings in these three stages are not equal and consequently the time for their maintenance is not the same. In this research it is intended to increase the life of ridders by reducing the weight of pistons. After studying the effects of replacing the cast iron material of pistons by 7075 aluminum alloy, genetic algorithm is implemented to optimize the design of these pistons. Maximum von-Misses stress and minimum allowable thickness of various sections of piston are the constraints considered during optimization process and Abaqus finite element technique using Python script are utilized during optimization. Replacement of the material reduces the piston weight from 780 kg down to 271 kg and by optimizing the piston design, it was further reduced down to 261 kg which totally could considerably reduce the wearing rate of riders by reducing the total normal force on riders.
Keywords: reciprocating compressor, Piston, Aluminum alloys, optimization, Genetic Algorithm -
Pages 43-50
Steels with quenching-partitioning (Q-P) heat treatments are the third generation of advanced high strength steels (AHSS) which have been developed due to their interesting combination of mechanical properties including high strength with good flexibility. Partitioning is based on carbon diffusion from martensite (M) to residual austenite (γ_R). In the present investigation, an alloy with a weight composition of % Al 0.054- % Si 1.5 -% Mn 2.2 -% C - 0.21 - Fe containing 0.08% Ti as a micro-alloy was prepared using a vacuum induction melting (VIM) furnace. Purification was performed using an eletro-slag refining (ESR) furnace to reduce sulfur and oxygen and then the molten alloy was cast as an ingot. The ingot was then homogenized at 1200 ° C for 3 hours. The homogenized ingot was then rolled to 1.5 mm thickness sheet by hot and cold rolling processes. After quenching-tempering (Q-T) and quenching-partitioning-tempering (Q-P-T) treatments, the properties of the samples were evaluated by scanning electron microscopy (SEM), X-ray diffraction analysis (XRD), micro-hardness, tensile and Erichsen tests. The Q-P-T samples showed more favorable combination of strength and flexibility in comparison to Q-T samples. The strength and fracture strain of Q-P-T and Q-T samples were 1050 MPa, 24%, and 1185 MPa, 18%, respectively. The Q-P-T samples with remarkably higher strength, showed significantly higher flexibility.
Keywords: quenching-partitioning heat treatments (Q-P), retained austenite, tensile strength, fracture strain, micro-alloy -
Pages 51-62
At present, in the processes of manufacturing and assembling multi-layer (sandwich) industrial complexes with different materials, such as mold or fixture production, firstly the parts must be assembled and then drilled simultaneously; otherwise, the desired dimensional or geometrical accuracy will not be achieved. To make these holes, conventional drilling processes are mainly used, which due to the geometric shape and zero cutting speed at the drill tip, cause severe plastic deformation in the cutting zone. The use of conventional drilling process may reduce the dimensional and geometrical accuracy as well as the surface integrity of the inner wall of the holes. To reduce the mentioned problems, one of the relatively new methods proposed for drilling is the helical milling technique. In the present study, in order to compare the capabilities, advantages and disadvantages of these two different drilling methods, a total of 18 drilling tests using conventional drilling and helical milling processes and considering 2 variable parameters of cutting speed and feed rate (each in 3 levels) on metal multi-layer (sandwich) workpiece with 3 different layers of steel including MO40, 304L and CK45 was performed. Based on the obtained results, it can be stated that in order to achieve the desired dimensional (hole diameter) and geometrical (hole roundness) tolerances, the conventional drilling process has a better performance than the helical milling method, but in terms of achieving less surface roughness and better surface integrity (less surface imperfections), helical milling method has better performance than conventional drilling
Keywords: Drilling, Helical Milling, surface integrity, Dimensional Tolerance, Geometrical Tolerance