فهرست مطالب
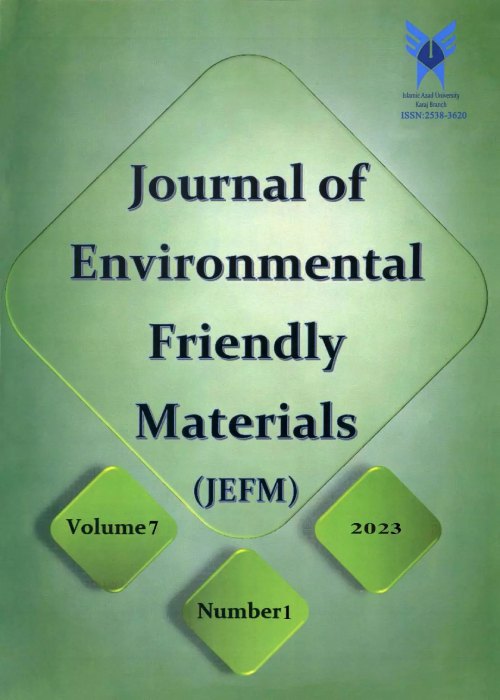
Journal of Environmental Friendly Materials
Volume:7 Issue: 1, Winter-Spring 2023
- تاریخ انتشار: 1402/03/27
- تعداد عناوین: 9
-
Page 0
-
Pages 1-6
Under water friction stir welding (UWFSW) is one of the modern and advanced manufacturing technologies of solid state joining and it is used for welding a wide range of materials. The energy-efficient technique used to the 6061 aluminum alloy joint and it has been demonstrated to be an effective method to improve the mechanical properties of joints. To illuminate the characteristics of underwater FSW, the microstructural evolution and its effect on mechanical performance of an underwater joint were investigated in the present paper. This work compared the parameters of normal friction stir welding (FSW) and UWFSW on the weld joint. In this investigating FSW used in underwater environment, for this operations research pin covered and shielded from contact water by hollow shaft spin (HSS), the HSS controlled the heat conduction of pin and disconnect with water, applying for the first time a novel underwater FSW technique developed in various industries. The metallographic exams indicate that weld nugget grain size has been decreased. The mechanical testing illustrated that hardness and tensile strength have been increased, on the other hand the percentage of elongation and impact energy have been diminished.
Keywords: Advanced Manufacturing, Under Water, Friction Stir Welding -
Pages 7-12
In this research, firstly, an oxide coating was created on the aluminum 2024 substrate by anodizing method, and then, with the aim of improving the surface properties of the aluminum alloy as much as possible, an electroless nickel-phosphorus coating was applied on this oxide coating. This hybrid coating was further heat treated at 450 degrees Celsius. Coatings were characterized Field-Emission Scanning Electron Microscopy (FESEM), X-ray Diffraction (XRD) and Energy-dispersive spectroscopy (EDS). The results indicated the formation of amorphous alumina by anodizing method on an aluminum substrate that contained some sulfur according to the sulfuric acid solution used in the anodizing process. The nickel-phosphorus electroless coating had 9.4 wt.% of phosphorus. The effect of coatings on corrosion resistance was also evaluated using TOFFEL polarization test. Examining the results of these tests has shown that the corrosion performance of the aluminum substrate has improved because of the application of the hybrid coating. Conducting heat treatment of hybrid coating at 450 degrees caused a decrease in corrosion resistance because of the production of small galvanic cells on the surface of the coating.
Keywords: electroless, Coat, polarization, phosphorus, anodizing -
Pages 13-23
A novel hybrid multi-generation system consisting of the following parts is proposed and thermodynamically analyzed: one gas turbine, one wind turbine, a district hot water, and a heat pump system for district heating, and a proton exchange membrane (PEM) electrolyzer to produce hydrogen as energy storage. This modeling is based on both one steam Rankine cycle and one organic Rankine cycle. The analysis for both energy and exergy is conducted, in order to comprehend the system performance, where values of 80.19% and 52.63% for energy and exergy efficiencies are found, respectively. Also an environmental impact assessment is performed and the effect of some parameters (ambient temperature, air compressor pressure ratio and wind speed) on carbon dioxide emission is investigated. During our investigation, some fuel is examined for combustion and fuel changes are reported. Furthermore, a study on the influence of enhancing renewable energy and reducing conventional system portion on production of a specified amount of electricity in an integrated system is carried out.
Keywords: gas turbine, Multi-Generation System, Exergy Efficiency, Wind turbine, CHP Systems -
Pages 25-33
Precipitation Hardenable Aluminum Alloys are suitable alternatives in electric vehicle bodies due to their lower specific weight compared to steel. Therefore, the development and understanding of the properties of aluminum alloys help to develop electric vehicles, reduce greenhouse gas emissions, and control global warming. In this research, we investigated the heat treatment of AA2024-T4 and AA6061-T6 alloys at a temperature of 453 °C for 210 minutes in a tube furnace with a heating rate of 5 oC/min in a vacuum (7.5×10-13 Torr). The alloys were assessed by optical microscopy (OM), scanning electron microscopy (SEM), and hardness test. The effect of heat treatment was investigated on the particle size as well as the phases. The particle diameter and hardness value of AA2024-T4 decreased after heat treatment. The number of precipitates in AA2024-T4 increased after heat treatment. Precipitates size in AA6061-T6 alloy remained almost unchanged after the heat treatment.
Keywords: Aluminum Alloys, AA2024-T4, AA6061-T6 -
Pages 35-40
Various fusion welding methods can be used to create a successful jont. However, with the increase in the thickness, fusion welding processes have limitations. Therefore, solid-state welding methods have been developed and in the meantime Resistance Butt Welding method has been chosen as a suitable method. In this study, joining of 1.6582 alloy steel has been investigated and analyzed, and the effect of the electric current parameter has been investigated in this welding method especially on Fatigue parameter. The results have shown this method is suitable for connecting (Joining) parts with symmetrical geometry. Also results shown that increasing the current to an optimum current leads to increasing the strength, As a result, the fatigue properties increase similarly to the strength. The noteworthy point here is that at stresses less than 220 MPa, the mentioned sample has a fatigue limit after welding, and this joint can be useful in various industries, including tool making.
Keywords: Resistance Butt Welding (RBW), 1.6582 Steel, Fatigue behavior, Solid state -
Pages 41-46
In recent years, selective laser melting (SLM) has attracted the attention of engineering active in this field due to its controllability, the possibility of producing parts with complex shapes and good surface properties. It has been found that by performing the next operation that takes place after the production of parts by SLM method, its surface properties such as corrosion and tribological properties can be improved. In this research, two types of subsequent treatments including heat treatment and surface mechanical treatment (shot peening) were investigated on the microstructure and corrosion behavior of the 316L sample produced by SLM method. Examining the microstructure of the samples with the help of optical microscope images showed that surface treatment and heat treatment make the grains rougher and finer, respectively. The XRD pattern of the samples indicated the austenitic nature of the alloy produced by SLM method, which did not show any phase change on it by mechanical operation. While heat treatment caused the formation of oxide compounds such as chromium oxide. The corrosion behavior of the samples was evaluated using the cyclic polarization test. The results of this test showed the positive effect of the oxide layer formed during heat treatment on the corrosion behavior of the SLM sample. Also, the sample with both surface treatments showed the highest corrosion resistance due to having the lowest roughness and the presence of chromium oxide.
Keywords: Corrosion, Phasing, Heat treatment, Selective laser melting -
Pages 47-63
Thermal barrier coatings (TBCs) are a crucial technology in thermal stability. Their use to achieve surface temperature reduction of the underlying superalloys surpasses all other achievements in the field of material technologies that have taken place in the last three decades. The technological advances in TBCs make them suitable for operation in the most demanding high-temperature environment of aircraft and industrial gas-turbine engines. The performance of these multi-layered and multi-material systems, tailored for high-temperature applications, is closely linked to their microstructure evolution. Many factors influence the durability of TBCs; therefore, in order to tailor these engineering materials for high-temperature applications, it is required to have a comprehensive understanding of the effects of the contributing factors and their interaction with the development of advanced TBCs. Improvements in TBCs will require a better understanding of the complex changes in their structure and properties that occur under operating conditions that lead to their failure. This article overviews the intrinsic and extrinsic degradation mechanisms, including TGO growth, thermal shock, CMAS attack, hot corrosion, erosion, sintering and phase transformations, thermal fatigue, thermo-mechanical tensile and foreign object damage.
Keywords: thermal barrier coating, Air Plasma Spray, Electron-Beam Physical Vapor Deposition, Degradation Mechanism -
Pages 65-79
Thermal Barrier Coatings (TBCs) are used to protect the surface of hot components of gas turbines. TBCs usually have three layers and include a Top Coat (TC) ceramic layer, an intermediate metallic Bond Coat (BC) layer, and a Thermally Grown Oxide (TGO) layer. In the present study, a brief survey of the microstructure of the ceramic layer produced by Air Plasma Spray (APS) and Electron Beam Physical Vapor Deposition (EB-PVD) has been done. Due to the inherent microstructure of the top coat ceramic layer, Diffusion aluminide bond coats are widely used in thermal barrier coatings for oxidation and hot corrosion resistance of Ni-base superalloy components of advanced gas turbine engines. Modifying these coatings by Pt addition considerably improves their high-temperature oxidation resistance. This effect of Pt has prompted intense research on the microstructure and oxidation behavior of Pt-modified aluminide coatings (Pt-Al) over the past several decades. The present review is to collate the available information on the subject. The study includes traditional b-(Ni, Pt)Al bond coats as well as the Pt-modified g–g¢ type of bond coats that have gained prominence in more recent times. A brief description of typical process steps involved in the formation of Pt-aluminide coatings is provided followed by a detailed assessment of coating microstructures reported under various processing conditions. The influence of prior diffusion treatment, on the coating microstructure, is highlighted. The various mechanisms of the role of Pt in enhancing the oxidation and resistance of aluminide coatings, as suggested in the literature, are discussed.
Keywords: Pt-Aluminide Bond Coat, Diffusion Coating, thermal barrier coating, Air Plasma Spray, Ni-Based Superalloy